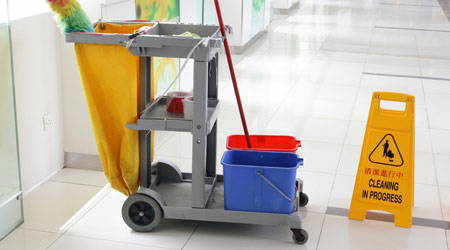
For smaller routes that cannot accommodate a full size custodial cart, the worker should be provided a utility bucket that allows them to carry the cleaning products, swab and cloths safely without possibility of spillage. A major source of carpet damage can be traced to workers carrying damp bowl swabs or leaking bottles that can ruin a carpet in seconds.
They could, in turn, have a microfiber flat mop system (possibly with a carafe on the handle) that allows them to perform low moisture floor work. Pre-moistened mops can reduce time and increase the clean + clean factor, as opposed to using the same traditional mop over and over.
I do not recommend rinsing and wringing out mops in sinks or toilets, which can produce its own set of issues as to cross-contamination.
A well-stocked, set up vehicle that allows the worker access to products (thinking rolling janitor closet) as well as tools and other supplies can increase productivity, enhance results and reduce complaints. There can also be benefits regarding safety when chemicals and systems are standardized. The vehicle should have its own set of SDS information readily available for ALL products in the vehicle.
One key point to remember is to only use approved products that are provided by your vendors. Do not purchase chemicals (even with the same product name) from a retail store unless you can get SDS information that matches the product. I have seen workers purchase bleach (which is not recommended in most cases) from a retail store and then try to use a bleach SDS from their vendor. Although it may be the same chemical formula, it is not wise or legal to do this
Your comments and questions are important. I hope to hear from you soon. Until then, keep it clean...
Mickey Crowe has been involved in the industry for over 35 years. He is a trainer, speaker and consultant. You can reach Mickey at 678-314-2171 or CTCG50@comcast.net
posted on 8/30/2016