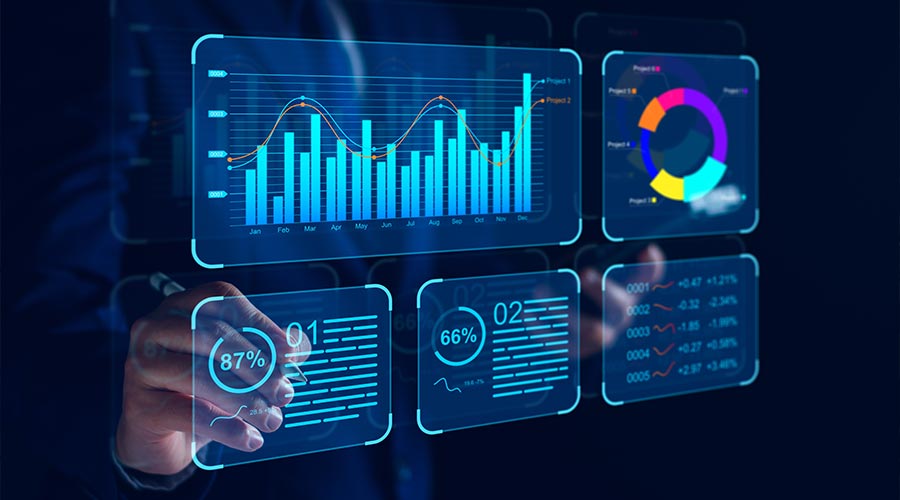
Contributed by Robert W. Powitz and Allen Rathey
The formal definition of Integrated Cleaning and Measurement (ICM) is an open-source, product-neutral framework in which best practices are defined by scientific measurement of cleaning outcomes and continuous improvement.
If that sounds a bit too formal, here is a better approach. When we make changes in cleaning products, cleaning equipment or even cleaning systems, our decisions should be defensible. Just because something is “new and improved”, doesn’t necessarily mean that it is better. There is no company that does not claim that their product is the ‘best’.
A questionable housekeeping-related purchasing decision can have far reaching consequences through lowered customer satisfaction and poorer cleaning outcomes; not to mention the potential of increased cost and decreased workforce efficiency. And in some occasions, illness and injury to the workers using the product as well as doing harm to the environment.
In this modern age when we watch every penny and when a professional error can result in serious litigation, we need to do everything possible to justify our actions. For these reasons, we need to compare what we already have and do to what we intend to change. In other words, we need to ask the questions: “Are we doing a reasonable job with what we have?”, and, “Is there a real benefit in what we propose?” Part of the answers lie in comparing some of the not-so-obvious cleaning outcomes through inspection and a simple series of experiments using measurements. In short, the overarching aim of an ICM system is to clean better.
The concept of using measurement tools to validate our decisions really took off some twenty-odd years ago with the introduction of Integrated Cleaning and Measurement (ICM). ICM put measurement in the forefront to give us unbiased comparisons between one product and system to another. Basically, the measurement portion of ICM provides us with objectivity rather than a subjective opinion. It lets us compare new to old, before and after, and most importantly, good measurement can justify our decisions. As a bonus, measuring housekeeping outcomes can answer the question: “How clean is clean?” for customer satisfaction and economy.
When we begin to consider measuring anything, we need to determine several basic issues beginning with “Why are we cleaning”? Realistically, are we cleaning for aesthetics (appearance), health (infection control), safety (prevention of slips and falls), or to control contaminants (preservation of surfaces)? We also have to include questions such as: Why we are measuring? What are we measuring? How do we eliminate bias when we measure? And, what will we do with the measurements once we have them?
We start by defining the problem. Namely, what do we hope to accomplish by measuring? Quite simply, we measure to make comparisons. A good measurement strategy helps us make an informed judgment in choosing the better of two alternatives. For example, we can use measurements to compare the performance of one cleaning chemical to another; measurements can contrast cleaning methods such as wet-mopping to touch-less cleaning or measure the effectiveness of using microfiber versus cotton cloths.
The possibilities are endless. Keep in mind, when we use measurements for comparative analysis, we need to clearly establish a single objective. We cannot compare apples to oranges. For instance, no measuring tool can compare biological cleanliness to slip resistance or appearance (aesthetic cleanliness). The biological cleanliness outcome of one system or product can only be compared to the biological cleanliness outcome of another. Slip resistance of one can only be compared to slip resistance of another. Both of these criteria can be measured objectively. However, aesthetic cleanliness is rather subjective, and any comparisons need both logical guidelines and simple surrogate measurements.
Now that we’ve defined the measurement objective, we have to consider how to set up our sampling plan, this includes the selection and use of the measuring tools, and, interpretation of the outcomes.
Good measurement begins with sampling. The objective of sampling is to get a set of measurements that are representative of the source under investigation. To do this, we need to develop a sampling plan that accomplishes three very important goals. The first is to match the sampling methods and tools to the questions we want answered. While this may seem intuitive, all too often we sample for one thing or at a given site, when we want something completely different. For instance, we sample mold when we actually should be looking for the source of wetness, or we sample for cleanliness without defining the type of soiling.
We need to target our actions to meet the questions we are trying to answer. Sampling for sampling sake, really makes no sense. Secondly, we need to eliminate bias. Sampling should ensure neutrality. We should never predict the outcome before we actually take the measurements.
Finally, we need to develop a sampling scheme and sampling strategy that is repeatable, so that we can go back and verify our findings if needed. If we plan it well, we can use the same sampling scheme in a similar situation or even expand on what we do without redoing everything. Repeatability is also credibility.
Before we leave this topic, there are two important things to remember: First, we need to encourage sharing of the data we generate. The more information we share with one another, the better the feedback. In fact, by sharing your findings, you may get some excellent suggestions and recommendations. Secondly, never use sampling or monitoring data punitively. Always use these data constructively to change methods, materials and behaviors for the better.
Contributor Information
Robert W. Powitz, PhD, MPH, RS, DLAAS
Forensic Sanitarian
R.W. Powitz & Associates, PC
http://www.sanitarian.com
Allen Rathey
President
Winning Environments (WE), LLC
http://www.winningenv.com
posted on 6/19/2024