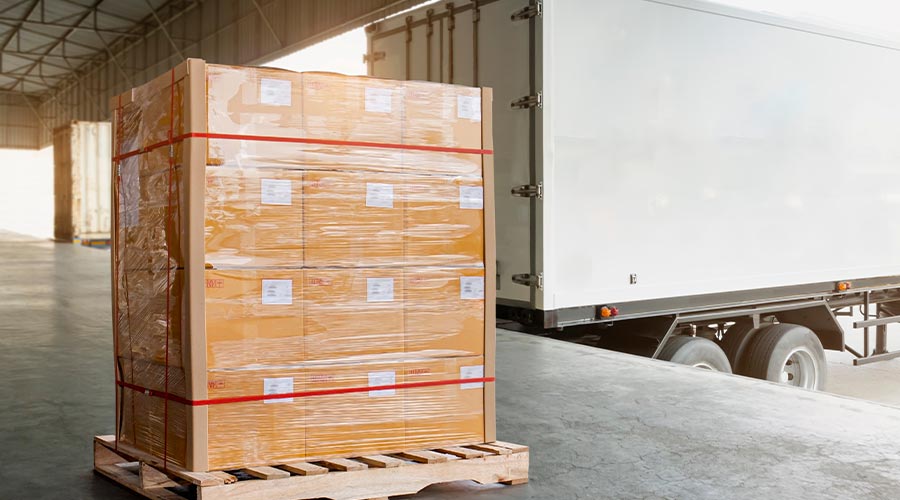
Contributed by Justin Malone.
Safety should be top of mind for every facility leader, especially with the rising trend in accidents within facilities across industries. An often-overlooked area is the loading dock, where vehicle, pedestrian and forklift traffic converge to move shipments in and out of the facility. An alarming 25 percent of facility accidents occur at the loading dock, with an estimated 600 near-misses for every incident that ends up happening.
Safe loading docks need to operate with properly monitored and maintained equipment without wear and tear. A $5,000 investment in equipment maintenance can be the prevention of a $1M insurance settlement or $200k fine from the Occupational Safety and Health Association (OSHA).
In past partnerships, our team worked with a national retailer to inspect and correct unsafe dock conditions in a distribution center with 71 dock positions. In that inspection, our team found no assets without evidence of wear, 80 assets that would need replacement in the next 2-4 years, and four assets requiring immediate replacement to avoid worker injuries. The proactive approach provided valuable data and solutions that immediately avoided costly accidents and fines.
Within the Hierarchy of Controls — elimination, substitution, engineering controls, administrative controls, and PPE — the proper equipment implementation and maintenance can be major drivers in eliminating or reducing safety risks from the top down. Figuring out where to start or what equipment needs attention first can be the most difficult part of improving. Here’s a list of equipment facility leaders should consider when setting up their loading docks for safety and efficiency:
Safety Railings: Fall protection issues are historically the most cited OSHA violations, so improving the fall prevention equipment can go a long way in improving facility safety. Safety railings not only eliminate the risk of falls, but they can also separate pedestrian and vehicular traffic within the facility. The important things to consider when installing safety railings are the proper height and resistance rating, and correct installation for the specs of the facility. Cutting corners here or going for looks alone won’t improve safety, so allowing a professional to inspect and install the right solution for the facility is important.
Dock Levelers: The dock levelers in the facility eliminate the gap between trailers and the loading dock and create a smooth transition for the lift trucks. When these levelers aren’t up for the job, they might not have the rating for the proper weight capacity or can cause back injuries from abrupt level changes on the forklift. Because of these risks, getting the right dock leveler on the front end will significantly reduce the risk of injury or major downtime events.
Trailer Restraints: These restraints keep trailers locked into the loading dock to prevent accidents or premature movement while crews operate. They eliminate the all-too-frequent risk of trucks pulling away from the loading dock while personnel are still inside or trailer tip-overs when the trailer becomes unstable during loading and unloading. During lift truck operation in and out of the trailer, they cause momentum that can gradually scoot the trailer further from the dock and create a gap in instances where trailer restraints are not used or used improperly. Wheel chocks should be used in conjunction, but they are not a replacement for operational trailer restraints and should never cause an override.
Dock Bumpers: From a safety standpoint, these take care of equipment and ensure a longer lifespan by absorbing impacts by up to 80 percent. They reduce the wear and tear on the building itself and the trucks attached to it by putting a layer of rubber between contact points of metal and concrete. This also significantly reduces noise and should be highvisibility so drivers can see exactly where they should drive the truck while they reverse. Dock bumpers need to be replaced when they show signs of wear, since there is no preventative maintenance in their case.
Control Panels: The dock levelers and trailer restraints mentioned above work together to keep trucks and the people working around them safe, but how can you know they’re working together correctly? Control panels serve as the communication channel to give the green light when crews can work in a safe environment. They can also work as a fail-safe in the chain of safety to shut down operations when equipment malfunctions or improper uses are detected. These should only be installed and maintained by those certified for control panel work due to the electrical risk and the possibility of disturbing the safe functionality through overriding mistakes.
When companies don’t think ahead and invest in proactive care, they harm their ROI due to riskof extended downtime costs and emergency repairs, along with falling out of line with OSHA guidance. While they can’t completely remove reactive maintenance from operations, a comprehensive maintenance strategy will create an optimized balance reducing reactive care to as little as 20 percent of work performed. Currently, 55 percent of facilities are still primarily reactive in the way they repair equipment.
Through careful monitoring and the comparatively minimal up-front investment in proper equipment maintenance, facilities can ensure their facilities are safer for workers and avoid costly accidents and downtime.
Justin Malone is Corporate Field Safety Manager at Miner, the only national service partner for smarter, safer loading docks. As the premier expert in docks, doors and more, Miner’s coast-to-coast team of best-in-class service professionals help facilities mitigate risk, improve efficiency and achieve consistency.
posted on 5/15/2024