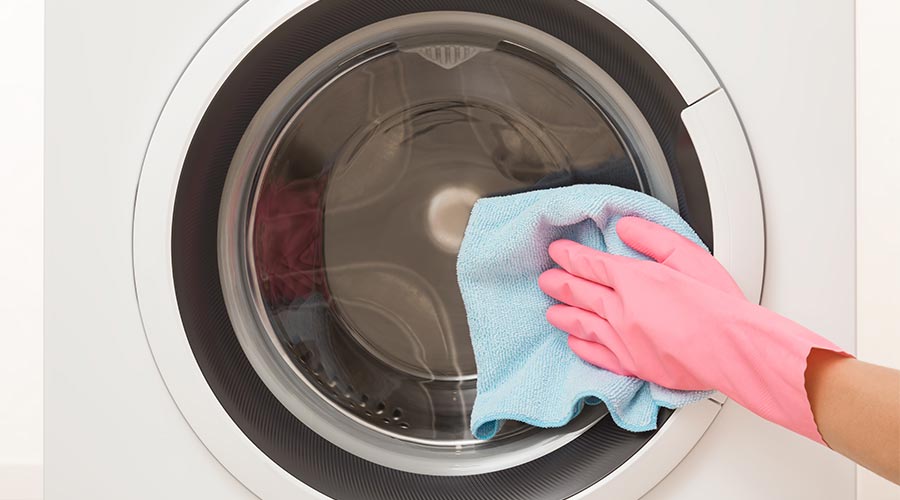
Contributed by Phil Carrizales, ACME Paper & Supply Co.
When it comes to microfiber cloth, is reusable better than disposable? That was the question one of the largest hospital systems in the Maryland/Washington D.C. region grappled with as it worked to ensure infection control and disinfection as well as cost efficiency.
Acme Paper & Supply Co.’s audit of the health system’s utilization of reusable microfiber cloths and mops looked closely at various factors affecting the maintenance of reusable microfiber including laundering, sanitation, replacement costs, and infection prevention. We compared the effectiveness and efficiency of reusable versus disposable microfiber materials to help the health system find a long-term solution.
A Closer Look at the Numbers
A closer examination uncovered hidden costs associated with reusable microfiber materials. With more hospitals turning to third-party laundry services to address labor shortages and mitigate the expense of maintaining and replacing commercial laundry and sanitation equipment, facilities are losing the ability to quality check and control the laundering process.
Consider this scenario: A hospital receives a shipment of reusable microfiber mops, only to discover discrepancies in the count upon return from the laundry service. With no tracking systems in place, hospitals are often faced with excessive replacement charges. In some cases, these costs amount to over $100,000 annually per hospital.
Addressing Sanitation Concerns
Beyond cost efficiencies, sanitation of reusable microfiber materials is becoming a more pressing concern. Despite stringent laundering standards set by manufacturers, studies have shown that a portion of laundered mop heads tested positive for pathogens upon return to the hospital.
A 2013 study conducted by CleanLink found that 27 percent of laundered microfiber mop heads from 11 hospitals tested positive for pathogens and bacteria. The risk of cross-contamination and hospital-acquired infections (HAIs) associated with improperly washed reusable microfiber cloths poses a potential threat to patient safety.
CDC guidelines state that the water temperature in the washing machine must be at 160 degrees Fahrenheit for a minimum of 25 minutes to kill all the bacteria. If contaminants are not removed during the wash process, mops and cloths can transfer germs around the surfaces they are meant to be cleaning. Many manufacturers specify that reusable microfiber cloths and mops can get anywhere from 100 to 500 washings before they need to be replaced. But, that’s if these materials are being washed properly and according to specifications and CDC guidelines. There are also no guarantees that the same microfiber being sent out for laundering is returning to the hospital it originated from.
The Disposable Advantages
Considering these facts, the case for disposable microfiber cleaning materials is growing. Disposable options offer many benefits that outweigh any upfront costs including:
• Convenience. Having pre-wrapped and easy to store packaging of individual microfiber cloths, towels, and mop heads helps cleaning teams meet and possibly exceed efficiency and hygiene requirements.
• Cost savings. Disposable microfiber can cost less overall when you look at eliminating replacement charges for materials that are damaged, lost, or past their prime. There are also no third-party commercial laundry and delivery fees for disposable microfiber materials.
• A substantially lower risk of cross-contamination and hospital-acquired infections caused by sanitation processes that do not meet industry standards.
• The elimination of potential quat binding. Quaternary ammonium chloride (quat) is an active ingredient in many of the disinfectants used in hospitals. Quat binding occurs when the active ingredient is absorbed into the microfiber material. This results in less of the disinfectant chemical being distributed to contaminated surfaces.
A Change May Be Coming
Disposable microfiber is emerging as a viable solution for many types of healthcare facilities seeking to enhance cleanliness and reduce HAIs while reducing long-term operational costs. And, as manufacturers explore ways to address the environmental impact of disposable materials, the case for their adoption grows stronger.
The integration of disposable microfiber materials in healthcare is certainly a trend worth watching.
Phil Carrizales, I.C.E-T, A.C.T is the Director of the Hygiene and Facilities Solutions Division at Acme Paper and Supply Company, one of the nation's largest suppliers of sanitation solutions, disposable food service packaging, restaurant equipment and supply, retail and industrial packaging, and custom-designed packaging. Phil has over 20 years of experience in account management for major cleaning suppliers and is ISSA certified. Phil can be reached directly at pcarrizales@acmepaper.com. For more information visit https://www.acmepaper.com/index.html.
posted on 5/15/2024