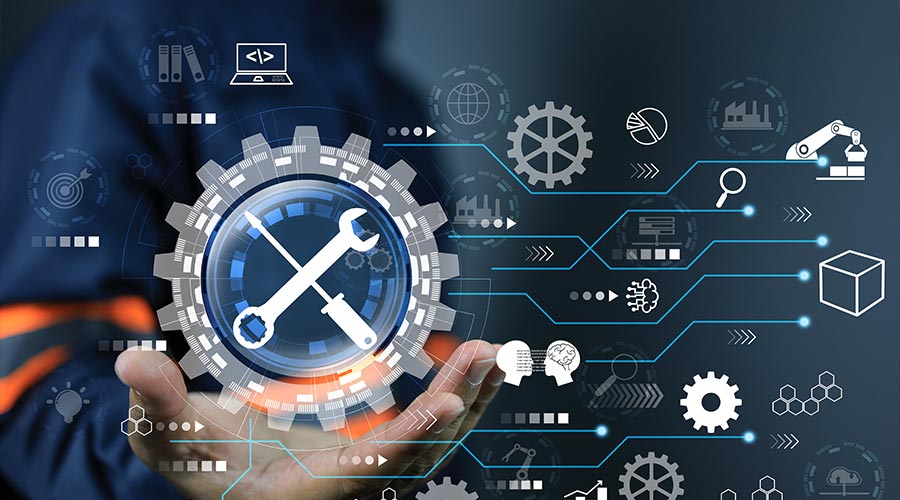
Contributed by Phil Carrizales, I.C.E-T, A.C.T., Director of Hygiene and Facility Solutions, ACME Paper & Supply Co.
Equipment breaks down. It’s almost inevitable. But when it happens, do you have a strategy for minimizing or eliminating downtime in your facility cleaning and maintenance schedule?
With building owners and facility managers increasingly turning to sophisticated robotic cleaning equipment for their fleet of cleaning machines, the businesses that implement a Preventative Maintenance (PM) program have a leg up. Ensuring that cleaning equipment remains in optimal working condition can directly impact efficiency, safety, and cost management.
Preventative Maintenance: Why You Need It
Preventative maintenance refers to the regular, scheduled service of equipment to reduce the risk of unexpected failures and extend the life of machinery. PM programs are a proactive approach to catching issues such as mechanical breakdowns or parts failures before they turn into costly problems that result in equipment and crew downtime.
You expect your facility’s cleaning equipment to be ready to use when needed, just like how you expect your car to start every day. With a car, for example, skipping routine oil changes, brake and battery inspections, and fluid checks can result in the failure of the vehicle and a major inconvenience. Regular maintenance alerts you to excessive wear and tear and impending problems. The same principle applies to cleaning equipment like robotic floor scrubbers and vacuum cleaners. Think about all the moving parts that should be routinely inspected to prevent a problem such as worn belts or faulty electrical connections. A bit of forward thinking and inspection can help preserve a fleet of equipment for years.
The Benefits of a PM Program: Less Downtime
One of the biggest advantages of a PM program is that it minimizes downtime. When equipment breaks down unexpectedly, it disrupts cleaning schedules and often leaves facility managers scrambling for expensive replacements or parts. The cost of renting replacement equipment while awaiting repairs can equal or exceed the total cost of an annual PM program. Finding and ordering parts, which can take weeks or even months due to supply chain delays, is another worry that can be avoided with a well-structured PM plan.
How a PM Program Benefits Facilities
ACME works with a large school system that has 16 autonomous scrubbers and eight autonomous vacuum cleaners. Before they had a PM plan, they frequently had equipment breakdowns at one school or another, preventing the cleaning of the floors on schedule. After implementing a quarterly maintenance program four years ago, the school system has had less than one day of downtime across all their machines system-wide. That’s huge— saving time, money, and stress.
In this case, the school system found the PM program so valuable that they have built preventative maintenance into their annual budget to keep their fleet of equipment running smoothly.
Protecting Your Investment
Cleaning equipment, especially robotic or autonomous machines, is a significant capital investment. A single robotic floor scrubber or autonomous vacuum cleaner can cost tens of thousands of dollars, and without regular maintenance, that investment can quickly decline. Acme’s customers with a PM program find their machines last years longer because they are regularly and properly maintained, providing a higher return on their initial investment.
Certified Technicians for Maintenance
The complexity of today’s cleaning equipment makes the need for certified technicians even more important. To better service our clients, Acme employs a certified technician with specialty training and expertise to maintain and repair today’s high-tech cleaning equipment. Even traditional machines such as walk-behind vacuum cleaners have advanced circuit boards that require a high level of expertise to maintain. One wrong move can short a circuit board, which can cost thousands of dollars to replace, demonstrating the need for certified maintenance specialists.
A Tailored Approach to Maintaining Equipment
A facility’s preventative maintenance program should be specifically tailored to the building’s cleaning needs, ensuring that even the most advanced machines receive the right care every time. A tailored PM plan helps facility managers avoid costly repairs, extend the life of their equipment, and focus on what matters most: keeping their facilities clean, safe, and operational.
Phil Carrizales is the Director of the Hygiene and Facilities Solutions Division at Acme Paper and Supply Company, one of the nation's largest suppliers of sanitation solutions, disposable food service packaging, restaurant equipment and supply, retail and industrial packaging, and custom-designed packaging. Phil has over 20 years of experience in account management for major cleaning suppliers and is ISSA certified. Phil can be reached directly at pcarrizales@acmepaper.com. For more information visit https://www.acmepaper.com/index.html.
posted on 11/11/2024