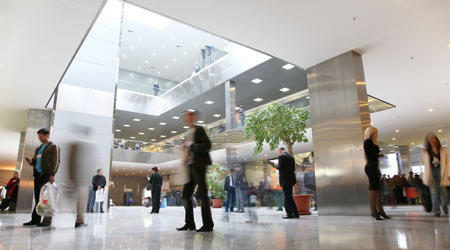
A reader writes: “We have a customer who expects us to keep a high gloss on VCT (Vinyl Composite Tile) with stripping/waxing once per year and buffing once per year. They also are concerned about black marks from shoes and carts. Are their expectations reasonable?”
Following is a summary of suggestions that may or may not apply since there may be other factors in play that we did not discuss. The most important aspect is for both parties to commit to eliminating or reducing the black marks and maintaining a clean, safe floor throughout the year. This issue can be improved if not completely resolved in many different ways subject to budget constraints. The points I am suggesting are based on commonly accepted industry practice.
Vendor/Contractor:
1. Review the products and processes being used to strip/recoat the floor annually.
a. Note that a soft finish (18 percent) will shine better but not last as long
b. Consider using a harder (25-30 percent) finish that may not shine as well but should last a lot longer. There are products specifically designed for long wear.
c. How many coats of finish is your floor crew applying? This is very important due to the length of time between stripping and buffing.
2. Review the current dust mopping and damp mopping processes since it is very important that all grit is removed from wheels and foot traffic.
3. Make sure walk off mats are kept clean by means of vacuuming and our cleaning systems.
4. Consider a semi-annual or quarterly scrub/recoat to keep enough finish on floor.
5. Consider using the Stop Lite system (colored dots) to know how many coats of finish are on floor during year in different areas of building.
6. Consider utilizing an old tennis ball (or buffing pad center piece) to remove scuff marks.
7. Make sure you are using a neutral detergent, clean mop and clean solution.
8. Consider converting to microfiber flat mop system including double bucket and appropriate laundering.
9. Apply Mickey’s 80/20 Rule that stipulates that since 80 percent of wear and tear is on 20 percent of area; once that area is identified, 80 percent of effort should be expended there to maximize labor/supply investment.
10. Bring in chemical/equipment supplier to verify that all chemicals, pads, solutions, mops are correct for job.
Customer:
1. Purchase and maintain quality walk off mats to capture grit/soil from feet and wheels.
2. Inspect/service/lubricate the wheel bearings of carts to make sure they are not sticking.
3. Verify the carts can handle the weight of the items being moved.
4. Coordinate with vendor during inclement weather to increase dust/damp mopping frequencies.
5. Consider modifying specs to require a “matte” low luster finish rather than high shine/gloss.
6. If high shine/gloss is preferred, consider modifying specs to increase frequency of scrub/recoat and buffing/burnishing procedures throughout year.
Your comments and questions are important. I hope to hear from you soon. Until then, keep it clean…..
Mickey Crowe has been involved in the industry for over 35 years. He is a trainer, speaker and consultant. You can reach Mickey at 678-314-2171 or CTCG50@comcast.net.
posted on 12/5/2016