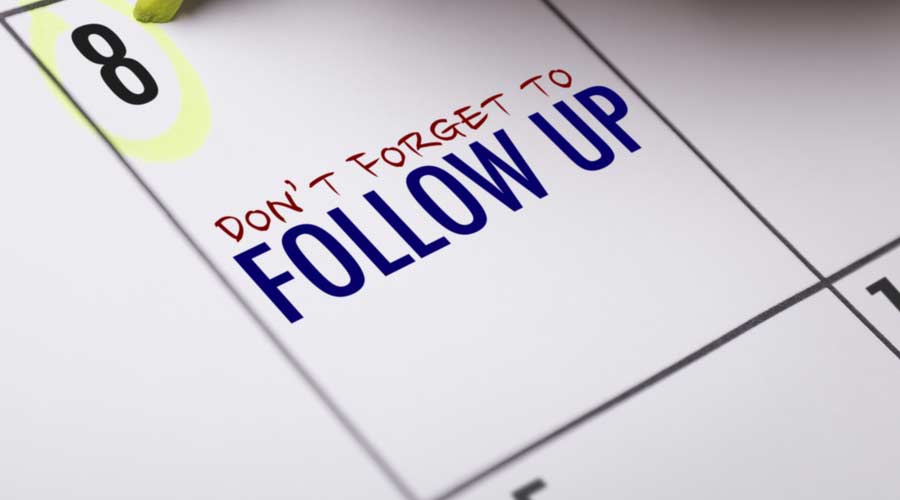
Keeping on top of training and implementing the right products and equipment that reduces injuries leads to fewer workers’ compensation claims. That’s essential because part of what makes the cost of workers' compensation claims so daunting is the multiple avenues in which it affects BSCs. Not only are there the medical replacement costs, which includes paying for any ailments related to the injury, but there’s also the income replacement cost, which comes from still needing to pay the injured employee and filling in for the loss of production on the frontline cleaning team.
Injuries will be inevitable, and some cases will unfortunately result in long recovery times. There are steps, however, that BSCs can take to ensure that those losses are mitigated as much as possible. St. John recommends implementing a case management strategy for every worker compensation claim on file for the company. Whether it be an in-house representative or a third-party hire, the primary goal of case managers is to make sure the afflicted employee is staying true to their recovery process.
SMG goes with the in-house route, appointing a director of safety the sole responsibility of handling managing workers' compensation claims and conducting follow-ups. Weintraub says having one dedicated employee to the task goes a long way to making sure injured employees aren’t abusing the system and getting paid to recover when they could already be back to work.
“You can't be everywhere, and there's going to be accidents,” says Weintraub. “I think the next-most important part — besides the proactive safety of your company — is how you follow up.”
Case managers will routinely check in to see how the employees are doing, when they are scheduled to visit the doctor or physical therapist, and then follow up with those offices to verify that a session or appointment took place.
While a BSC has every right to verify if an employee completed their appointment with a doctor, St. John stresses that the BSC itself should avoid discussing any medical specifics on the case.
“That opens the opportunity for HIPPA violations, and no one would want to touch that with a 10-foot pole,” she warns.
Doing due diligence regarding employee recovery progress equips the business with a record that proves the employee is being looked after, while also ensuring that the staff completes every step of the process for their own benefit.
“The faster you can get them engaged at some level, maybe starting with light-duty work, the faster you will get them back full time,” says St. John. “The longer they are out without any work, the more expensive it's going to be — and it's going to be worse for the employee who isn’t making their full income.”
Weintraub concurs, adding that many insurance companies utilize a return-to-work policy that will pay injured employees just to get out of the house and do something active — minimal as it may be. Examples include having them visit an animal adoption center or nursing home just to get them on their feet.
“You’d be surprised at how quickly people get better when they're going to these places,” he says. “It can really get the ball rolling.”
With the sheer amount of physical labor required to get cleaning jobs done, accidents and the subsequent workers’ compensation claims will be an inevitable part of business. The best defense comes through optimized safety protocols, ergonomic equipment, consistent training and a well-prepared team to minimize the cost of incidents when they do occur. If done correctly, BSCs will have healthier and happier employees — along with less strain on the budget.
James DeGraff, senior associate editor, has spent four years creating and overseeing content for Contracting Profits, Facility Cleaning Decisions and Sanitary Maintenance magazines, as well as CleanLink.com.
How BSCs Can Mitigate Workers' Compensation Costs