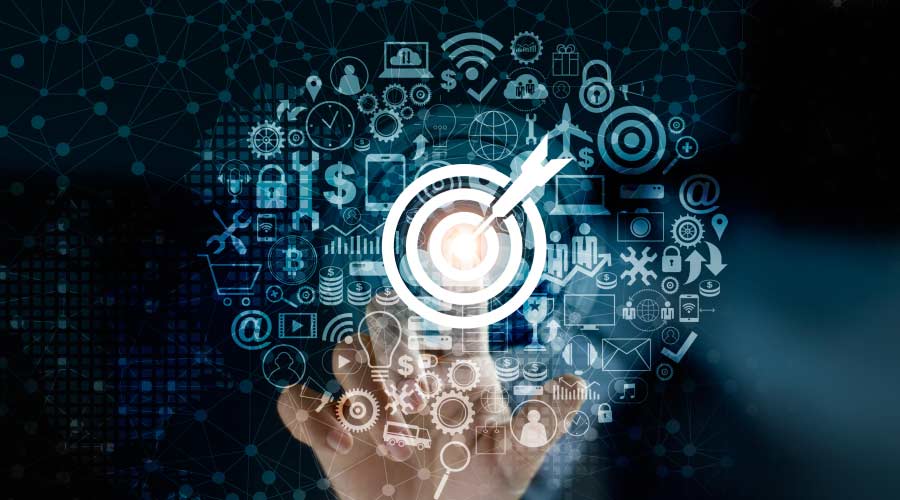
Located in Ontario, Canada, Lexus Cleaning Services Inc. has 182 employees and specializes in janitorial services for high-end retailers, shopping malls, and multi-purpose office spaces. To validate cleaning practices, the building service contractor (BSC) has previously relied on adenosine triphosphate (ATP) testing. However, the tests were not successful on all surfaces, outcomes were often inaccurate, and the results lacked the level of detail necessary to pinpoint problem areas.
Fast-forward to the height of the pandemic when Managing Partner Mario Sequeira learned about Optisolve janitorial software while servicing a shopping mall food court for a property management company.
“Once a month, an individual would come to the food court and test 10-15 surfaces, and the client would share the reports with us,” says Sequeira. “We saw that over 2-to-3 months, our numbers from a bacterial perspective were not looking good compared to the rest of the mall.”
Sequeira learned that the surfaces were being tested with Pathfinder surface imaging technology, which captures photographs of contamination in high-risk areas via a mobile tablet and assigns each image a numerical pass/fail value. Quality management software gathers the data and generates reports that allow managers to monitor and assess cleaning quality for remediation and validation purposes.
Sequeira admits that he was skeptical of the technology at first. His cleaning crew kept failing the tests, and no one could figure out why. Then, one of his supervisors came up with an idea to test the technology’s validity. Using a dilution of bleach and water, frontline workers would disinfect the same high-touch surfaces prior to the inspector’s arrival.
“All of a sudden, our numbers were in the high 90s versus the 60s we were getting before,” says Sequeira. “That’s when I realized the technology was working, and I needed to incorporate it into our cleaning operations.”
Shedding Light
At the time, the software was not available to BSCs, but after extensive negotiations with the supplier, Sequeira was able to purchase it for his business. Optisolve trained two of his employees to take images using the mobile tablet, and they began rolling out the new solution at the offices of a multinational roofing company.
“We usually test very early in the morning on a monthly basis after everything has been cleaned,” explains Sequeira. “The idea is to not test the same surface every time. For instance, we may test a boardroom table and then a latch in a washroom cubicle.”
By analyzing data gathered over several months, Sequeira can discern areas where bacterial counts are low — as well as areas where counts are high and require further attention.
“We look at the reports and try to understand what happened,” he explains. “For example, is it cross-contamination that took place, or is it negligence? Then we decide whether to shift labor or offer training — or maybe there is something else that’s required going forward.”
During one test at the shopping mall food court where Sequeira first encountered the technology, one of the surfaces that repeatedly failed was the elevator buttons.
“Because the buttons are in a vertical position, it’s difficult to keep them wet for an extended period of time,” notes Sequeira. “Once we looked at the images and understood what was causing the problem, we started paying attention to our dwell times, spraying and wiping the same button three or four times to keep our numbers down.”
Door latches on restroom cubicles were also a pain point across all accounts and proved difficult to test prior to using Optisolve.
“One of the most important high-touch points is the door latch in a restroom, because you’re going to close and open it prior to washing your hands,” says Sequeira. “We couldn’t use an ATP meter because it was too difficult to swab the small piece of metal, but with Optisolve, we were able to get a fantastic image.”
Cutting boards were also challenging to test with an ATP meter. The microscopic cuts from knives harbored high concentrations of bacteria that often went undetected.
“Those were one of our biggest problems, because it was hard to get into those areas when testing,” recalls Sequeira. “With the Optisolve, we were able to take a photo and actually see the red lines where the highest percentage of bacteria was located because it was very hard to reach and eradicate.”
Armed with these images, Sequeira was able to offer his clients evidence of the contamination as well as possible solutions, such as submerging the cutting board in bleach or replacing it with a new one.
A Learning Experience
Although frontline custodians do not use the software program, Sequeira includes them in the process by having them present when testing occurs. This way, the staff has a better understanding of the technology and the importance of adhering to dwell times.
“At the end of the day, we have to justify this to our custodians,” stresses Sequeira. “We start with the perspective that you have to see it to believe it. A lot of them have language barriers, and this was new to them, so we had to introduce it slowly.”
Sequeira uses before-and-after images as an educational initiative for frontline staff. At first, some doubted the technology’s validity, but their skepticism was soon replaced with excitement. In fact, some employees started requesting tests to validate their cleaning efforts.
“I look at it as a motivational tool,” says Sequeira. “It motivates frontline staff to perform their tasks in a more effective way from a disinfection perspective.”
In addition to efficiency improvements, the program has helped the BSC classify disinfectants and verify dwell times. For example, on one occasion, workers divided a boardroom table in half and disinfected each side with a different product. After adhering to the manufacturers’ dwell times, they used the digital imaging solution to test the surfaces at different points.
“The results help us understand the effects of different disinfectants and whether or not we are using them correctly, because that is key,” says Sequeira.
Combining Cleaning Technology with Professional Instincts