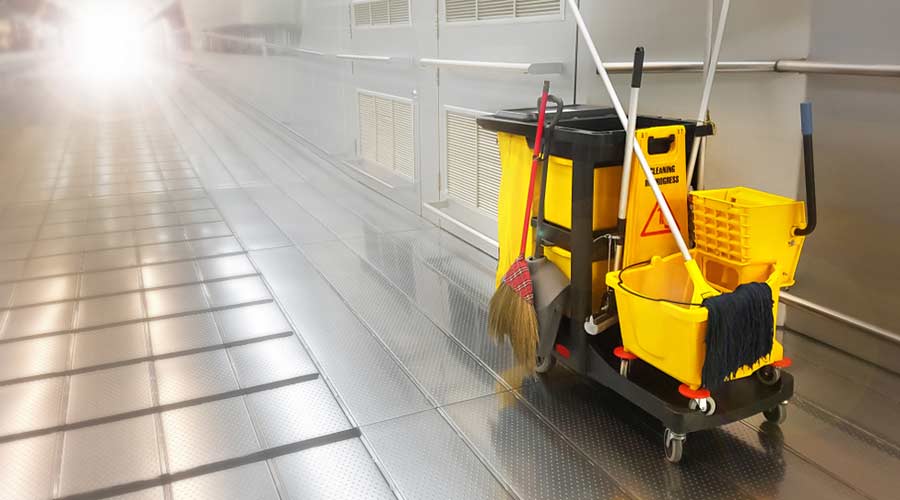
In theory, cleaning carts are supposed to make life easier for custodial staff — containing everything workers need to complete the day-to-day cleaning tasks in one highly mobile format. But the reality is often annoyingly different.
According to Keith Schneringer, senior director of marketing, JanSan + Sustainability for BradyPLUS, Las Vegas, these carts try the patience of many cleaning staffers.
“Some of the common complaints about cleaning carts include a lack of capacity to carry stuff needed to get their jobs done; carts that are too difficult to push — which is a function of bad design either because of poor balance of the cart, bad handle placement, and/or poor performing wheels; poor durability; and a lack of ability to secure products to prevent theft,” Schneringer explains.
Unfortunately, carts and mobile units aren’t frequently purchased items, leaving frontline workers to fend for themselves and make the most of existing equipment.
Contributing to the somewhat questionable appeal and functionality of these carts is the fact that they’re difficult to keep clean and sanitized — if the attempt is even made. However, experts stress that it is virtually impossible to achieve effective cleaning results using carts and tools that are dirtier than the surfaces workers are trying to clean.
“Trash, dirty water, dirty rags, dirty brooms and pans are all collected on these carts, and they are difficult to clean. Unused cleaning items and supplies should not be on the same cart as dirty tools. Collection of trash and soiled items should be separated,” says David Thompson, director of the Academy of Cleaning Excellence, Orlando, Florida. “Personally, I believe that trash collection should be on a separate cart.”
Ron Segura, president of Segura & Associates, San Bruno, California, agrees, stating that cart cleanliness and organization should follow a routine schedule. He warns that carts that aren’t cleaned and maintained regularly can become damaged or sources of cross-contamination. Either of these results could prevent a worker’s ability to maintain a hygienic environment.
“When cleaning closets are inspected, the inspection should also include janitor carts,” Segura adds. “It is essential to have a system in place to keep the cart clean and tidy at all times.”
Cart Organization
Organizing a cleaning cart can be a daunting task. Careful planning and attention to detail are required. Since one of the primary obstacles is a lack of space, cutting back on the number of products transported on the cart will help. Aiding in this process is the fact that now many chemicals can be used for multiple purposes — an advancement that not only reduces their numbers, but also makes these carts more versatile.
When assembling and organizing what should go on a cart, Segura says the facility’s needs, surfaces and cleaning frequencies must be considered first. Even so, there are some basic items he says most carts should contain, including microfiber cloths, sponges, scrub brushes, mops/brooms, dustpans, vacuums, cleaning solutions/chemicals, disinfectants, trash bags and gloves.
“Building service contractors should opt for high-quality products tailored to the surfaces being cleaned,” he advises. “The goal is to make all tools and supplies easily accessible and available for efficient and effective cleaning.”
Accessibility is one thing, but organization is another. Properly organizing, or even color-coding tools and cloths, can make or break infection prevention processes by minimizing cross-contamination threats.
“Care should be taken to separate cleaning tools and cloths by color so that restroom materials are used in the restroom, general materials are used in general areas, and foodservice cleaning materials are used in foodservice areas,” says Schneringer.
To improve productivity, BSCs could also consider the order in which the cleaning happens, positioning necessary items “front-to-back” depending on that sequence. For example, trash is usually collected first, followed by floor tools. Then comes stocking items and finally wiping surfaces.
Optimal cart organization will have some variability to it, says Schneringer, but there are generalities he offers to help in the effort. For example, the top of the cart should be stocked with the most frequently used items. It should be possible to keep dirty and clean items separated as well as wet/dry items, and there should be an ability to collect and separately hold waste that is considered landfill, recyclable, and compostable — if applicable.
When considering organization, it’s important to evaluate supplies and identify safety concerns that might arise. In some cases, lockable spaces/compartments on carts might be necessary.
“Arrangements should be made to keep things safe and secure if there is a concern that unauthorized people may gain access, steal or be exposed to materials on the cart that could be hazardous,” Schneringer explains.
How Fine-tuning Cart Organization Pays Dividends