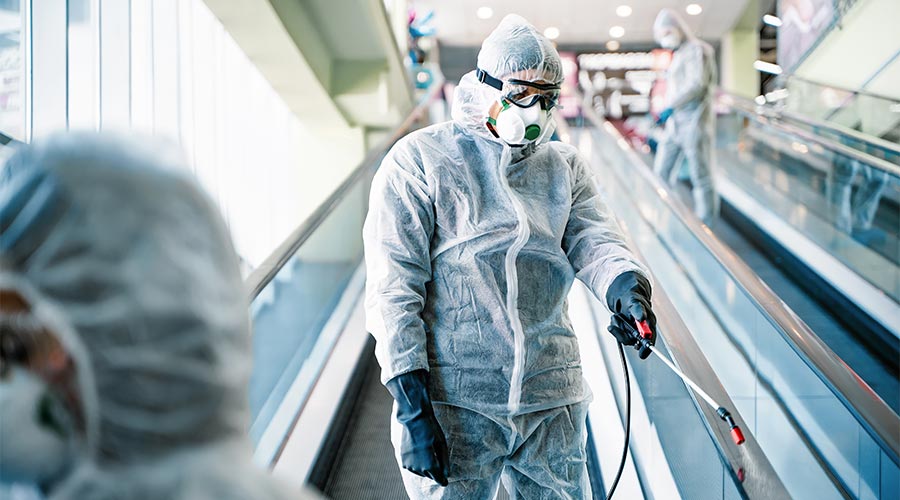
"The label is the law," Solomon stresses, emphasizing the importance of adhering to disinfectant instructions. Choosing the right product is important, but using it correctly matters, too.
The EPA requires chemical companies to submit their labels for review. All labels contain usage instructions for the product.
“A chemical must be applied in adherence with this label,” she says.
Beyond the label, Hicks notes both the EPA, and the Centers for Disease Control and Prevention (CDC), recommend cleaning a surface first and then disinfecting it.
“You can remove 98 percent of the soil from a surface by cleaning it,” he says. “Removing 98 percent of the soil from a surface will also remove harmful bacteria.”
Some disinfectants claim to clean and disinfect in one step. However, Hicks maintains those products have only been tested in the presence of 5 percent invisible soil. He stresses using those disinfectants with higher soil concentrations is considered off-label use.
“If cleaning is done well, it should be followed with a disinfectant from List Q for new and emerging viruses,” he says. Hicks recommends applying this disinfectant with an electrostatic sprayer for even coverage on pre-cleaned surfaces. Spray bottles, he says, atomize chemicals that employees breathe in as they work.
“In contrast, electrostatic sprayers work by positive-negative attraction,” he says. “Most surfaces are negative, so the sprayer puts a positive charge on droplets coming out of the electrostatic spray nozzle. These charged droplets look for that negative surface that they can attach to.”
However, Solomon warns to use electrostatic sprayers with caution as many chemical labels do not mention their use.
“During COVID-19, a lot of BSCs were applying chemicals with electrostatic sprayers that could never legally be applied that way,” she says. “The application method is whatever is specified on the label.”
Labels inform how products can be applied and what surfaces they may be applied to. It’s important not to overlook that information.
Hicks explains that during the pandemic, people turned to hardware store pump sprayers for do-it-yourself (DIY) disinfection. Unfortunately, he says this method often applied harsh chemicals to surfaces that could not handle them.
“The demand for nightly disinfection meant that materials not designed for such frequent exposure — like certain finishes and fabrics — were damaged, raising concerns about the long-term effects of excessive cleaning,” he says.
Hicks recommends a targeted approach to maintain hygiene in shared spaces. Identify high-touch surfaces, like microwave handles, elevator buttons and refrigerator doors, for targeted disinfection. Then focus cleaning efforts on those hotspots to prevent the growth and transfer of infections, as well as the potential of cross-contamination.
“By prioritizing the removal of soil and grime, we can eliminate the food sources that allow bacteria and viruses to thrive, reminding us that good hygiene often begins with simple, thoughtful cleaning routines,” he says.
High-touch surfaces should be cleaned at least daily, and more often with heavy use, using the least corrosive disinfectant possible.
“Read the label,” says Hicks. “If the label says do not spray on stainless steel, then spraying it on stainless-steel elevator button panels would be a no-no. Make sure workers are trained to use a disinfectant that is compatible with the surfaces they are cleaning and disinfecting.”
Personal protective equipment (PPE) also should be considered well in advance of an outbreak, according to Solomon.
“Cleaning technicians need to wear PPE that’s appropriate for the type of transmission, whether it's droplet, airborne or contact,” she says. “It also needs to be appropriate for the chemicals they are using.”
Mindful Monitoring
Validating cleanliness after cleaning is vital, experts agree. The goal should be to validate that the area is clean, but it is not intended to be punitive, says Solomon.
Using an ATP meter or a fluorescent gel light can validate cleanliness quickly. For example, the ATP test generates a number that shows how many pathogens are on the surface. A high ATP reading, expressed in Relative Light Units (RLU), means the surface is not clean and indicates more cleaning is necessary to prevent the growth of microbes. Experts agree that clean surfaces generally have an RLU of 30 or 40, while dirty surfaces may have RLUs as high as 600.
Validation is unnecessary everywhere, every day. In fact, auditing two rooms a day in a 100-bed facility or two classrooms in a 100-classroom school is likely sufficient.
Solomon recommends a follow-up meeting between a manager and a cleaning technician after validation.
“I like visual validation tools, like fluorescents, because they are excellent teaching tools. You can bring a technician back to an area and they can visually see what they missed,” she says. “Validation is an opportunity to re-educate and retrain. I would document those training opportunities, so that if you see a pattern emerge, you can address it differently.”
Insero agrees, “It is important that we effectively communicate KPIs with the cleaning team, acknowledge their success and develop an action plan for any areas that need improvement. Regular audits, clean KPIs, immediate feedback and ongoing training ensures compliance with cleaning, disinfection and infection prevention protocols.”
Hicks suggests supervisors observing employees is as effective as other validation methods.
“Watch and ask, ‘Are they sticking with their training? Are they using products the right way? Are they making sure not to cross contaminate anything?’” he asks. “Put eyeballs on how products are being used and whether processes are being followed.”
The Next Step
BSCs can build trust with clients long before an outbreak occurs. Here are a few recommendations from experts:
-
Talk it Out: Effective communication about cleaning efforts, backed by data and transparency, builds trust among building occupants and helps to maintain a safe environment.
-
Leverage Technology: Consider apps or digital platforms that allow occupants to report cleanliness concerns in real time, enhancing responsiveness and accountability.
-
Visual Indicators: Use signage to show that areas have been cleaned and disinfected. Placing visible cleaning schedules in public areas can enhance transparency.
-
Conduct Surveys: Periodically survey building occupants and cleaning staff to gather feedback and identify areas for improvement in cleaning practices and communication.
-
Create a Clean Culture: Promote health and hygiene practices like handwashing and sanitizing among staff and occupants, creating a collaborative effort to maintain a clean environment.
BSCs can establish and strengthen trust with clients long before a health crisis arises. Prioritizing effective communication and transparency about cleaning efforts reassures occupants and fosters a collaborative, safe atmosphere.
By being proactive, BSCs protect health and enhance well-being, leading to a cleaner and safer future for all.
Ronnie Wendt is a freelance writer and owner of In Good Company Communications in Waukesha, Wisconsin.
How Cleaning Teams Prepare for the Next Infectious Outbreak