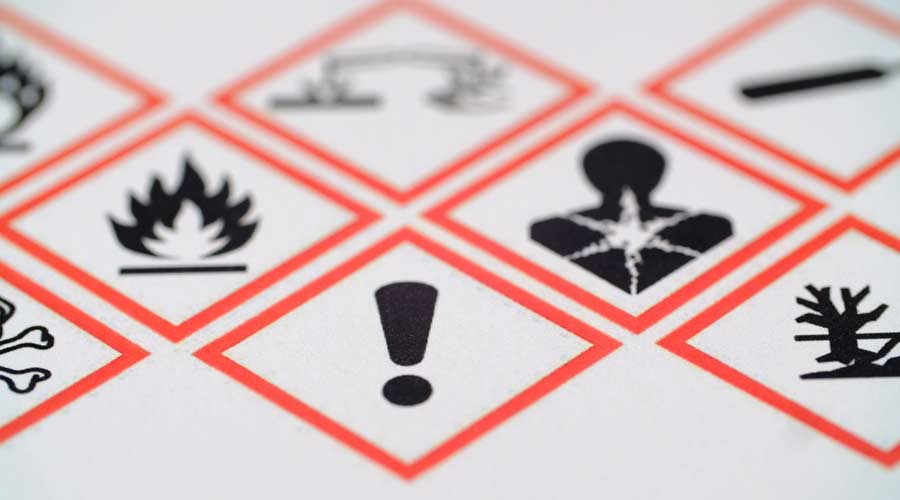
Drilling down to the details of what should and should not be included on a cleaning cart, and their positioning, will also improve efficiency, ease of use and safety for BSCs. For example, Thompson says that since many frontline cleaning crews are now using microfiber, including a laundry bag holder for wipers/pads would be a good idea. And rather than an open tray, there should be bottle holders, which would keep these chemicals from moving about. As for what not to include, he nixes gallon containers of any kind, as well as chemical measuring systems.
“Additionally, open water containers should never be in the front and loose to move around on the tray,” Thompson notes. “Water spills are very common and produce slip-and-fall hazards for the technician. Water should be over the transport wheels, not the swivel wheels. This would make the cart easier to steer and result in less sloshing of the water. Heavy items should be located over the fixed axle, not in front of the back wheels.”
Schneringer cautions against placing incompatible chemicals, such as bleach and ammonia, in proximity to each other. He also advises placing dry items above wet items rather than below, which could lead to them getting accidentally wet in the event of a spill or accident. A similar approach is recommended for dirty items, keeping them away from clean so that these are not inadvertently contaminated.
One strategy to separating soiled from clean items is using a dedicated hamper or bin with a lid that can be sealed. This will contain wet mops, dirty brooms or soiled linens.
“Used wipes and empty bottles can be placed in a separate trash bin lined with a plastic bag and disposed of regularly,” Segura adds.
There are recommendations to stocking carts, but in the end, carts are a personal tool and what is and isn’t included may cause tension between management and the frontline worker. Although some BSCs might allow their workers to slightly personalize carts, there should be baseline standard operating procedures when stocking these mobile units. Requirements such as proper weight distribution can mean huge safety gains.
Not only is weight distribution important when it comes to productivity, but it is essential to avoid injury from incidents such as tipped carts. Accidents like this can be prevented with the right cart and the right organization of items on the cart, making sure it’s not so heavy and unstable that it becomes a hazard.
Carts that are unsturdy is only one problem stemming from improper weight distribution. Personal physical issues resulting from improper weight distribution include pain and discomfort in the back, neck, shoulders and knees. Difficulty breathing and fatigue are other symptoms. Ergonomic experts recommend periodic staff training sessions on proper lifting techniques, which can help avoid injuries related to this issue.
In response, there is a growing preference in the industry toward more compact and lightweight cart designs that are easier to maneuver and tuck away.
“These carts may incorporate features such as adjustable shelves, ergonomic handles and locking mechanisms for added security,” Segura explains. “As for underutilized configurations, there may be potential for cleaning carts that incorporate smart technology, such as sensors that detect when supplies are running low and automatically reorder them, or GPS tracking to monitor the location of carts to ensure they are being used efficiently.”
Other potential innovations include carts that can be customized based on the specific facility/environment or tasks, such as hospitals, care facilities, restaurants or schools.
Cart features, design and stocking options can vary, but experts agree that most cleaning teams see the value of a well-organized cart
“When people understand the benefits of an organized cleaning cart, they become more motivated to take steps to improve the situation,” says Segura. “It’s essential to raise awareness and encourage individuals to prioritize this aspect of cleaning to ensure a more efficient and effective cleaning process.”
Pamela Mills-Senn is a freelance writer from Long Beach, California. She is a frequent contributor to Contracting Profits.
Cleaning Cart Improvement Tips for BSCs