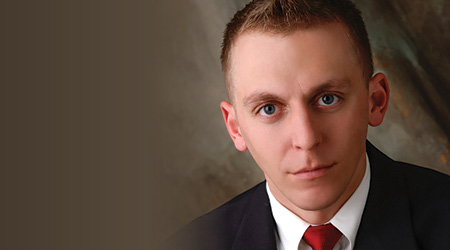
One of the biggest challenges in managing custodial operations is fighting fires, versus preventing them. It is not uncommon for most custodial managers to be thrown off course by the daily demands of keeping a facility clean. In fact, I have found that not managing the four concepts below are usually the root cause.
Streamline daily chemical inventory.
Most custodial operations are addicted to purchasing chemicals. In my experience, the general daily cleaning of a facility only requires the use of a germicidal detergent (for restrooms and restroom floors), an all-purpose cleaner (for above the floor surfaces and glass) and a neutral mopping solution (for floors outside of the restrooms). Instead, it is not uncommon for custodial closets to be chemical dumps.
Solve this by whittling the daily use chemicals down to one type of each of the aforementioned chemicals, and inventory them for daily use. Project chemicals for hard water, carpet and hard floors are different, periodic and should be tightly controlled and dictated by schedule.
Track complaints, comments and daily issues.
Most cleaning operations deal with serial complainers. They are usually the folks who throw a paper clip or a corn chip under a desk and start the stopwatch on how long it sits there.
You can get ahead of this behavior by starting a formal complaint program and having the person issuing the complaint sign each individual one. It seems simple, but if you have 25 complaints in one month issued by the same person, you have data that will help modify that behavior. There are a few really good apps available for this, but if you don’t want go that route, a simple log book will do.
Additionally, consider a simple form for cleaning workers to document issues that arise during their individual shifts. Most cleaning operations have fairly robust software for issuing work orders and such, but access is usually limited to supervisors. Having the ability to quickly document maintenance issues, broken equipment, complaints, security issues, or even compliments is empowering for cleaning workers and gives supervisors useful real-time data.
Perform meaningful, quality checks and inspections.
While appearance inspections may be useful for discovering immediate issues, they only capture a small snapshot of what’s really going on within your cleaning operation.
A more effective method is to use a checklist of your daily cleaning assignments to determine if the work is being performed properly. This is one of the best ways to find out if the cleaning crew has been equipped with the right tools for the job; trained properly; understand daily assignments; know how to dilute and use chemicals properly; understand daily equipment storage and maintenance; and whether they understand safety protocols. This is not only an inspection of your crew, but it’s also a subtle way to evaluate the management team.
Track daily equipment use by operator.
Equipment — vacuums in particular — take a daily beating. They also end up being the sole focus of turf wars between individual crews or custodians. The newer, better functioning equipment tends to become “theirs” rather than that of the operation. While a sense of personal ownership can be a good thing, many times it leads to equipment being hidden or broken, and can be a principal tactic in inter-shift warfare.
Eliminate this by having a central equipment storage area where check-in/out is required. Furthermore, have managers sign-off on the equipment as it is checked back in daily. Doing so creates accountability, encourages proper daily maintenance and reinforces training.
Considering these four solutions in your daily management arsenal will put you on the road to recovery from fire fighting. They give you tangible management assets and put you back in charge of your cleaning department.
Ben Walker is the Director of Business Development for ManageMen, Inc., a leading cleaning industry consultancy specializing in training, transitions, auditing and educational materials. In addition to his consulting work, Walker is the author of ISSA’s best selling book: 612 Cleaning Times and Tasks.