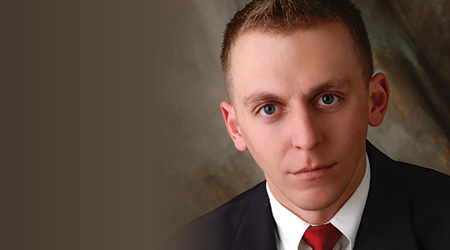
Over the past three years, I’ve had the privilege of getting involved in the standards community. I was part of a team of volunteers who took Simon Institute, a small non-profit formed by professional cleaning operations, through the process of becoming an accredited standards developer by the American National Standards Institute (ANSI).
This was a very thorough process, and one that was quite tedious at times — for a good reason. There are just over 200 accredited standards developers in the United States, which speaks not only to ANSI’s high standards, but also to the fact that there is a strong process for developing standards in the United States.
The purpose of this column isn’t geared toward explaining the accreditation process, or the rigorous process involved in getting draft standards through the system. Rather, it is to highlight the importance of why standards matter and how they affect our industry.
The cleaning industry ranks high on the list of workplaces reporting injuries. Workers are exposed to risks and hazards everyday, including slips and falls, repetitive motion injuries and chemical hazards. And these hazards stretch beyond cleaning workers to building occupants and facility patrons.
There has been a lot of awareness brought to some of these issues, particularly slips and falls, by the diligent efforts of standards developers such as the National Floor Safety Institute. But we’re just beginning to scratch the surface of developing good working standards for the cleaning industry that can prevent mistakes and protect people from harm.
Here is one example of a time when a standard could have helped:
Three years ago, in my hometown of Salt Lake City, a husband and wife went out for lunch. As they gathered their food and prepared to sit down, the wife stopped off at the drink station to get a glass of sweet tea. What happened next was horrific. Security footage showed her taking a sip of the tea, then almost instantly grabbing her throat. Through a labeling miscue, a worker misunderstanding, and a perfect storm of mishaps, the tea had been accidentally sweetened with a lye-based product for cleaning deep fryers, instead of sugar. The wife spent weeks in the hospital recovering, lost most of her voice, and the franchisee is currently in a lawsuit with the manufacturer and distributors of the chemical.
Whether or not the suit is just isn’t the point. Issues like this happen too frequently with cleaning products and workers who come into contact with them. How often do you read about a facility evacuation because two different types of chemicals were improperly mixed? Do a simple Google search and you will see that it happens fairly regularly.
As an industry, we have a large responsibility to develop and embrace standards that take our cleaning workers out of harm’s way, protect the occupants of our facilities, and provide enough due diligence for manufacturers and distributors to ensure that risky mishaps like this don’t happen. It’s on all of us.
The Simon Institute has initiated the process to develop a standard for the safe handling of cleaning chemicals for custodians. Once finished, there will be an industry-driven, voluntary standard that is aimed at mitigating this costly problem. The idea is to build a training program that educates and verifies the training of cleaning staff on the understanding of the chemistry they come in contact with on a daily basis.
Standards aren’t just a list of rules to make us feel good about what we do. They are an important driver of safety, risk reduction and progressive decision-making. They protect our departments, our budgets and liability. I’m excited to see what the future holds.
BEN WALKER is the Director of Business Development for ManageMen, Inc., a leading cleaning industry consultancy specializing in training, transitions, auditing and educational materials. In addition to his consulting work, Walker is the author of ISSA’s best selling book: 612 Cleaning Times and Tasks.