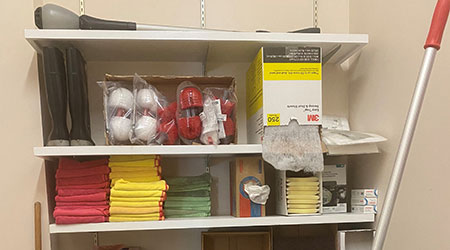
For many, a new year is an opportunity for a fresh start. That could mean a new diet, resurrecting a favorite hobby or the chance to get rid of old habits and start anew. I decided to take a closer look at our cleaning processes and how our custodial closet usage and integration with inventory management technology has improved cleaning operations efficiency at the Athens-based University of Georgia Facilities Management Division (UGA FMD).
While relaxing over the holiday break, I realized that 2020 marks the arrival of a new opportunity to improve our facility management organization and enhance the customer service initiatives that we provide to our campus community. The standardization of equipment and materials in our closets, along with regular staff training, serves to improve worker safety, ease of locating supplies and materials and reduces clutter, all the while demonstrating the professionalism of our cleaning team.
A Look At Layout
Our UGA FMD Services Department staff have voiced strong support for custodial closet inventory and standardization because they know that with it, the equipment and supplies they need are always available and all necessary personal protective equipment has been inspected and is in stock. They know this because they are all involved in the stocking process, in one way or another. Comprised of dedicated cleaning training staff and equipment specialists, the Services Department Training Specialist team ensures all new staff complete the Building Service Worker Academy program. Meanwhile, all existing staff complete an annual green cleaning procedures refresher. The courses include reviewing pictures of the approved closet layout, custodial cart set-up, required equipment and cleaning supplies, closet shelf inventory standards and closet cleaning equipment staging layout.
Our custodial staff supervisors submit their custodial supply and material orders via an electronic inventory management system managed by our FMD Warehouse Unit. Additionally, the training specialists work with campus custodial supervisors to ensure inspection forms are completed and submitted monthly to maintain green cleaning certification compliance. Taking product and equipment inventory is made simpler when the space is designed properly. At UGA, the FMD Services Department engaged the Engineering Department and Office of University Architects to create facility design standards for new custodial and equipment storage areas. These new design standards ensure permanent and convenient access to water and electricity, while providing adequate square footage for cleaning operations.
Standardization guidelines require all custodial closets to include chemical dispensary units for on-site generation of cleaning products (lock-n-dial or gun dispensers) to eliminate ready-to-use chemical bottles and clutter. The guidelines also restrict the number of extra products stored in the closets, which is monitored and managed via a building chemical use report. This report enables the facility supervisor, department leaders, and warehouse staff to track chemical inventory and usage trends at each building.
When inventory is needed, electronic order requests are generated by the facility supervisor based on inventory data, and items are chosen from a pre-approved commodity list. Warehouse staff then deliver the orders to each building every week, as vendors do not deliver to individual buildings. For emergency material or supply needs, supervisors either complete an electronic emergency order request or they coordinate with department leadership to identify and use another building’s available stock.
This streamlined process greatly reduces the mindset leading to ‘hoarding syndrome’ of commonly used items. Meanwhile, facility cleaning projects involving deep cleaning of VCT tile, large area or classroom carpet cleaning, or stair tread cleaning would be considered ‘heavy cleaning projects.’ These projects are planned in advance, allowing time for any needed commodity items to be electronically ordered based on a quarterly work plan.
Any restorative, non-green certified cleaning supplies require prior approval by FMD Services Department leadership before they can be ordered. These products are not regularly stored on campus and are not readily available to staff as a “stock” item for electronic ordering.
Regular Inspections Ensure Adequate Supplies, Safe Equipment