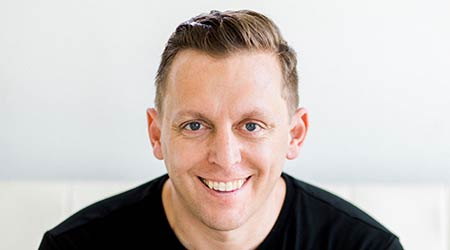
Last month, I had the privilege of participating in a panel discussion on CleanLink.com with a diverse group of professionals. The subject was a frequent topic in the profession: implementing innovations in your cleaning program. After the session, a participant asked what each panelist thought were the most promising innovations in the cleaning industry. My response was not as cut and dry as some might expect.
Almost universally, cleaning operations struggle to find adequate space to manage their program. Even more challenging is the struggle of keeping existing space that they do maintain.
I’ve gone through a lot of closets in my career. Very often, I find a single common thread: custodial closets function as storage for chemicals, equipment, paper and soap. They are also a break room, locker room, and sometimes serve as a manager’s office.
Most operations do have adequate space, but over the years, each closet becomes its own kingdom for the person who uses it. More often than not, that poor soul is buried alive — metaphorically speaking — in a humble 20-square-foot space.
Finding solutions for leaner cleaning operations isn’t a new concept. The problem is that it hasn’t necessarily been well-defined, is too general or is written by people who don’t run cleaning programs. One of the simplest and easiest ways to remedy this is to repurpose existing space and make it a functional component of your operation. Addressing the following concepts will help you get started.
Bulk Storage: Where bulk materials — chemicals, wear items (such as vacuum filters) and replacement tools — are stored for the entire operation. This can be a single, ample storage space, or an area or zone for sizable multi-facility operations. The bulk storage is primarily accessible by managerial staff — kept under lock and key, so things don’t sprout legs and walk away.
Check-in Area: Each team needs an area where workers clock in, grab their tools and go. In zones with multiple facilities, this may be in a single building that serves as a home base.
Pantry: One of my favorite innovations in newer buildings are pantries between each set of restrooms. These areas are best suited for storing restroom consumables. The spaces reduce the need for crowding carts with heavy paper rolls, but it also prevents spills when said carts are overloaded and go over thresholds.
Equipment Storage: This is usually a closet or space where large pieces of equipment live. Go through that stock and determine what’s needed and what is surplus. For example, if your building has no carpet, you probably don’t need five carpet extractors.
SDS: Can your supervisors and leads tell you where the safety data sheets (SDSs) are located? If not, then you need to address this immediately. The best rule of thumb is to keep them within 10 minutes of travel time (walking, running, driving, or a combination of the three) and in centrally located areas where they’re easily identifiable.
Most discussions on innovation revolve around new tools and products, and rightfully so. The drive to create faster, better and more is how new technology is born. That said, one of the fundamental elements that often takes a back seat is whether a cleaning operation supports a daily cleaning process. Considering these six components can help.
Ben Walker is COO at ManageMen, Inc., a leading cleaning industry consultancy specializing in training, transitions, auditing and educational materials. He can be reached at ben@managemen.com.