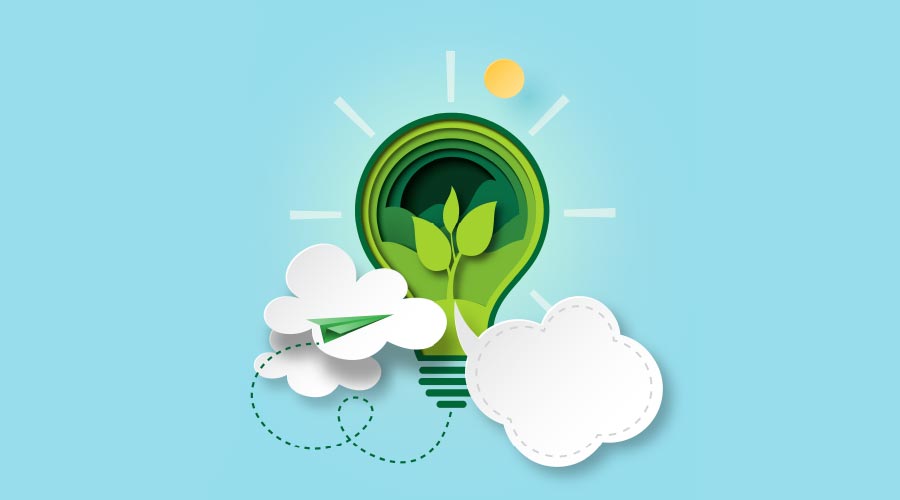
Going green is nothing new. Since the first Earth Day celebration in 1970 birthed the creation of the Environmental Protection Agency, awareness about human impacts on the planet has grown. In fact, many improvements have been made in these last 54 years. For example, we no longer have lead in our gasoline and Ohio’s Cuyahoga River has not spontaneously caught fire since 1969.
When it comes to the commercial cleaning industry, despite great strides toward sustainability, some facility managers seem stuck in the stone age. It’s understandable. The early days of green cleaning were, well, bad — products were expensive and less effective than their traditional counterparts. A lot has changed since then.
“Twenty years ago, we would be having a different discussion,” says Steve Ashkin, president, The Ashkin Group, LLC, Oxnard, California, when asked about the barriers to successful green cleaning programs.
Today there are benchmarking tools, certifications, and consultants to help guide a facility’s green cleaning journey. There are also third-party organizations that authenticate product claims, so facility cleaning managers can be confident in their choices. It’s a major step forward.
“Compared to 20 years ago, we now have the benefit of eco labels that will help facility managers weed through cleaning products,” explains Sara Porter, vice president of external affairs, Healthy Green Schools & Colleges. “The marketplace has so many options for certified products that work well and are as affordable as standard products. There’s no reason not to choose these options.”
For schools in some states, going green is not a choice but a mandate. The Environmental Law Institute lists 10 states and the District of Columbia as places that have some kind of green cleaning mandate in place. Policies around meeting these decrees vary greatly from jurisdiction to jurisdiction.
But having rules on the books doesn’t guarantee facility managers will execute the best program.
“Event when there’s a regulatory mandate, some will do the absolute minimum required to meet that mandate,” says Dean Stanberry, SFP, CFM, chair-Global Board of Directors, International Facilities Management Association (IFMA), Houston. “I used to think that mandates would drive change. Now I believe it is a combination of mandates along with demands from investors and consumers/facility occupants that will be the ultimate drivers.”
Identifying Hurdles
Even though the “green” and sustainable products on the market today are comparable in price and effectiveness to traditional alternatives, facility cleaning managers might still find implementing them is an uphill battle. Launching a successful, enduring green cleaning program requires a lot of buy in, especially from leadership.
“If an organization doesn’t prioritize sustainability from the top in its vision and mission, it would be really hard for an individual department to launch an independent initiative on its own,” says Stanberry.
In the fortunate case that leadership is on board, managers will then be challenged with crafting a mission and outlining an operational plan. That would include identifying proper equipment, products, and procedures to execute the plan.
“Facility managers should ask themselves if the organization has the processes and people to launch and operate a successful program. If not, this is a good place to start,” adds Stanberry.
Fortunately, there is help available for those cleaning managers who are ready to craft that mission. The EPA offers some advice, as does the State of New York, but Ashkin recommends starting with a thorough inventory of what’s already in the custodial closet. Developing this baseline includes assessing the products — cleaning chemicals, paper products, plastic liners, and equipment — already in play. The exercise may be quite illuminating.
“I’ve found facilities stocked with old samples left by sales reps,” Ashkin reports. “Over the years, you end up with 50 half-used bottles waiting to leak or be misused.”
Taking inventory should identify some immediate easy fixes. This low hanging fruit may include moving from all virgin paper products to paper with recycled content. Switching from C-fold towels to large paper rolls is another easy, “green” swap — one that will decrease use from occupants, according to Ashkin. He also suggests investigating concentrates versus ready-to-use chemicals, and plastic liners thick enough to do the job, so janitors don’t have to double up.
Conducting an inventory lets facility managers know what they have and gives them an opportunity to identify what they need. Investigating what to buy next can feel a bit daunting, but outside help is available. One — albeit expensive — solution would be to hire a consultant, but it isn’t the only option.
“You don’t have to pay for a green consultant,” insists Ashkin, who is in fact a green consultant. “Twenty years ago, transitioning to ‘greener’ programs was hard work. Today it’s easy. There are hundreds of manufacturers making thousands of products that meet standards.”
Porter agrees, adding that consultants can work well, but budgeting for them could stretch some organizations too thin. She points to a wealth of other free resources available, including her organization’s self-assessment tool.
“It’s a nice benchmarking tool,” she adds. “You answer a series of questions and get a score. After you implement your policy, you can retake it and see how the score changes.”
There are also the U.S. Green Building Council’s LEED O+M: Existing Buildings green cleaning policy documents. And experts agree not to ignore the benefits of networking with other professionals/organizations that have taken steps to “green” their cleaning.
“There is quite a brain trust out there,” adds Porter.
Meanwhile, science-backed, third-party certifications take the guesswork out of buying “green” products and equipment. Labels like Green Seal, EPA’s Safer Choice, and UL Ecologo have “done the homework for you,” says Porter. “You don’t have to worry about greenwashing.”
If this all still seems like a lot, facility cleaning managers need to look no further than their local jan/san distributor. These professionals offer a lot more than just product sales.
“Ask your distributor to do a green spend report,” says Ashkin. “They want to keep your business and will be happy to work with you to figure out how to best change product mixes.”
The Cost of Going Green