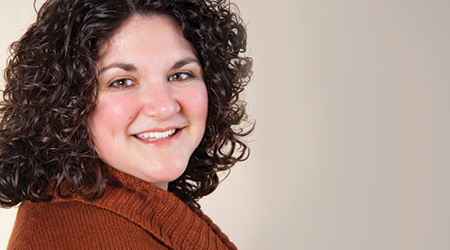
Over the last six months, whether I'm speaking with in-house facility cleaning executives, building service contractors or jan/san distributors, they all lament about the same struggle: staffing. As cleaning demands increase, professionals in the jan/san market are struggling to keep up. There just aren't enough applicants coming in and retention efforts continue to falter. One cleaning manager I spoke to said his department was functioning (barely) with 40 percent fewer frontline workers at any given time.
Since I entered this industry 17 years ago, the mantra of "doing more with less" always hovered in the background, but it is more prominent now than ever before. Departments need help and technology might be the answer.
In May, I was invited to Interclean Amsterdam, the largest global cleaning event offered to our industry. I was proud and very honored to represent the U.S. market on this global platform, but the opportunity also provided a chance to see how other countries were tackling cleaning challenges.
As I perused the extensive show floor, it was hard to miss the technology on display. I saw presentations on dispensing equipment that simplified dosing. There were restroom dispensers and apps that tracked usage and stock levels. There was training software and tools used to measure the organic material on surfaces. But the most prevalent technology was robotic (autonomous) machines. One company (of many) had 12 different machines on display and there was an entire Robot Arena set up to offer ongoing demos of equipment from all manufacturers throughout the show hours.
Unlike in Europe, autonomous machines aren't prominently used in the United States, at least not yet. They often come with a hefty price tag and some people fear the training challenges associated with the machines. Often, though, I hear complaints that robotic equipment takes jobs from human candidates, which is exactly why more managers are now exploring them as an option.
The reality is departments can't afford not to consider adding technology into their existing programs. Robots, for example, have advanced platforms that simplify training; their improved sensors detect the most camouflaged obstacle; they are smaller in size to reach into tighter areas; they offer add-on options such as inventory tracking; and there are now some machines that are smart enough to identify spills or map an area completely on their own.
Staffing is an issue across the globe, and it doesn't sound like it's getting better anytime soon. If managers can implement technology that will streamline processes, improve productivity and minimize laborious tasks, they might win at doing more with less.