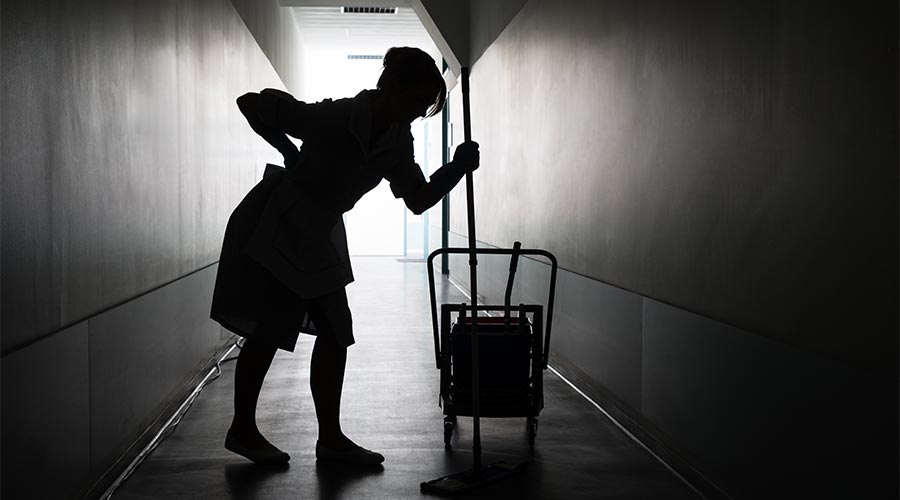
Like many constantly evolving and seemingly omnipresent industries, the realm of professional cleaning tools and equipment banks a whole lot on tradition. It makes sense that professional cleaning is a science based on years of experimentation, evaluation and refinement. Done correctly, workers can shave minutes off a cleaning program here, while saving a few ounces of product over there. It’s a constant push-and-pull of resources and investment against time and quality.
In recent years, green cleaning and sustainability efforts have become popular enough that sheer dollars-and-cents aren’t the only factors under consideration for facility managers looking to make less of an impact on the environment. Facility executives have shown an inclination to appreciate said efforts and are, at times, willing to invest slightly more budget dollars to improve results because it feels like a responsible thing to do.
Such investments are also a result of a recent trend in making job roles more appealing — largely to assist with turnover and retention rates. Executives have shown a tendency to invest in equipment, tools and products that, either via construction materials or design, make tasks a little easier for frontline workers.
In terms of real-world impact, this most often takes the form of tools that mean less wear-and-tear on the worker. Backs, shoulders, legs, and feet are often some of the first areas of complaint for workers in the cleaning field. Subsequently, manufacturers have now spent years looking at how to make their tools stand out from the crowd when it comes to offering products that workers feel comfortable using for hours and days on end.
At first glance, though, one wonders how much room for ergonomic improvement there can even be when it comes to familiar tools like brooms, buckets, and mops. These industry standards have been around from the very start and were mainly functional in their invention and mass production. They were made to complete a job and hold up physically for some time. Concepts like worker comfort and user friendliness would become more critical over time.
Now, facility cleaning managers are not just factoring in ergonomic features when practical; they are more invested than ever when it comes to protecting their workers’ bodies and boosting efficiency. At the core of the equation is the toll of work on a human body, and thus, such problems can require a scientific approach. After years of backaches, new tool designs are starting to give way to ergonomic breakthroughs that will have a resounding impact on the future of work — things such as longer, adjustable handles, lighter plastics for easier push-pull, materials that clean better with less volume and mass (think mop heads), and more.
Evolving Ergonomics
Early in their inception, one-size-fits-all tools ruled the day. The idea that cleaning equipment could be multi-purpose was an appealing concept, especially in terms of the actual quantity of tools that one would need to properly outfit a janitor’s cleaning arsenal.
Eventually, however, the push for worker comfort would turn from convenience to design principles that focused on reducing fatigue and painful, repetitive motions that have negative long-term implications on the health and safety of the employee. Three areas stand out when it comes to simple design components that make a huge difference for the worker:
• Bristle Material and Type: Bristle density plays a crucial role. For example, a mop with a lower bristle density is ideal for smooth floors, reducing drag and the push-and-pull force required. Conversely, denser bristles on a broom trap dirt more effectively on rough surfaces.
• Grip and Length Science: Handle design is a symphony of science and user comfort. Handle length is determined by the task. Mop handles for floor cleaning are longer to maintain a comfortable posture, while broom handles might be shorter for better control. Grip options, including textured surfaces, improve control, and minimize hand fatigue.
• Customization: One size truly doesn't fit all. Adjustable handles on hand tools allow workers of different heights to maintain proper posture, reducing stress on the back and shoulders.
Josh Kerst, CPE, CIE, vice president of Humantech Inc., an ergonomics consulting firm based in Ann Arbor, Michigan, says of design innovations that “Often, we’ve seen first attempts to adjust ergonomics miss the mark because they weren’t thought all the way through.”
For example, a no-lift mop bucket that drains right into a floor drain of a janitor’s closet sounds like a great idea, until it was realized that workers were dragging the bucket farther in search of a closet that suited their needs. Solutions should make life easier overall, not create additional issues.
Cohesive and Convenient
Ergonomic tools are designed not just for individual tasks, but to integrate seamlessly into a cleaning crew's workflow. Features like lightweight construction and stackable mop heads make equipment easier to transport and store. Hooks and clips on handles allow for convenient hanging in closets, keeping cleaning areas organized and safe.
One of the reasons that carts came to feature 360-degree swiveling casters, for instance, is to help workers not just move their supplies from place to place, but to allow access from multiple angles and maneuver into tighter and more awkward spaces, improving their access. For example, fixed wheels require wider turns, but swivel casters make for easier maneuverability and quick parking.
Sometimes, the environment forces innovation, say experts. Healthcare facilities pushed the need for quiet wheels to help patients rest, and they've since become a standard feature. Wheel-locking mechanisms are also being put on carts so that if they must be parked on an incline or a decline, they will not slide or drift away.
Efficiency and Effectiveness
The production process of tools plays a vital role in the final user experience. It can also translate to better cleaning efficiencies due to several factors:
• Material Selection: Choosing the right materials for handles (such as lightweight yet durable aluminum) and mop heads (microfiber for superior cleaning power, for example) directly affects worker comfort and efficiency.
• Rigorous Testing: Manufacturers often conduct field tests with actual janitorial crews, receiving valuable feedback on design, weight, and functionality. This ensures the tools truly address the challenges faced by cleaning professionals.
A tool that is truly meeting the definition of ergonomics should also positively impact morale and health. Success can be measured in several ways:
• Reduced Worker Injuries: Ergonomic tools demonstrably decrease the risk of muscle strain and long-term physical challenges, which is a major concern in the cleaning industry.
• Improved Cleaning Performance: By minimizing fatigue and discomfort, ergonomic tools allow workers to clean more effectively and efficiently.
• Increased Worker Satisfaction: Comfortable and well-designed tools contribute to a happier, more productive workforce.
By embracing ergonomics, facility cleaning managers are investing not just in tools, but in the health and well-being of their most valuable asset: the cleaning crew itself. This shift not only protects workers, but also improves cleaning performance and efficiency, creating a win-win situation for everyone involved.
Workers deal with tools and push carts for hours on end — the better a product is, the happier everyone involved will be. Frontline teams are less fatigued and frustrated, cleaning gets done more efficiently, everyone wins.
Technology Spearheads Industry Innovation