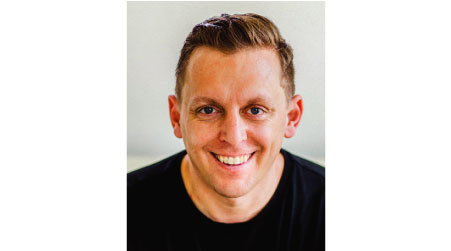
John P. Walker, former president of ManageMen, founder of Janitor University, trainer and industry innovator, used to say, “It’s simple to make things complicated. It is complicated to make things simple.”
With progress comes periodic failure — and, in my opinion, we don’t talk enough about that concept. We certainly don’t talk about it enough in a professional setting, and it has been my experience that we really tend to bury it quickly in the cleaning profession.
Understanding the reasons for why we fail can be a humbling exercise, but sometimes, the reasons aren’t as important as lessons contained within. These lessons can serve as a point for personal reflection, which can be challenging and emotional to accept, but often require courage before moving forward. It not only takes a strong leader to admit and accept failure, but a strong culture of leadership to address it properly.
I’ve spent many hours picking my favorite leadership psychologists’ brain on understanding failure, and how to make lemonade out of tough situations whenever they arise. What I’m frequently reminded of, sometimes to her chagrin, is that there is a spectrum of failure. It boils down to three essential types: complexity-related failure, predictable failure, and intelligent failure.
In my consulting work over the years, it has been my experience that most cleaning operations struggle with complexity-related issues. One system for one building, a different system for another; different tools, no processes, few procedures, differing management philosophies, non-specific training, inter-shift conflicts, and the daunting task of trying to get things done with consistency creates a complicated formula for every leader to manage — let alone execute with consistency. Much of it stems from what the leaders had to put together on their own through a process of trial and error, and with varying degrees of success. This creates fertile ground for regular systematic failures. In these complex operations, failures become unavoidable.
W. Edwards Deming once famously stated, “If you can’t describe what you’re doing as a process, you don’t know what you’re doing.” I like to think of cleaning operations as similar to the model airplane kits that I used to build with my father when I was in grade school. In each box, you’d receive plastic parts, a list of step-by-step instructions, and a list of tools needed to build the plane. Sometimes my excitement would get the better of me, and I’d skip ahead. When this happened, we’d lose parts and have pieces that no longer went together because I had glued pieces together before it was time to do so. This is a perfect example of predictable failure.
The purpose of having a system that creates predictable outcomes isn’t a call to become homeostatic — quite the opposite. With the presence of a process that generates predictable outcomes, the path is paved for pioneering ideas. As long as you stay true to following the original process, the stage has been set for performing micro-experiments to test.
In a cleaning operation, this might look like testing a new tool to see if it fits in your process. Does it really improve the steps, or does it omit them to the detriment of the outcome? Did it create more work, or less? Does it require creating a new set of steps? Does it complicate your operation, or does it simplify things? These are all questions that can be answered when intelligent failures happen.
Failure, while uncomfortable, doesn’t always need to be a negative experience. As a leader, it challenges you to look for the opportunity for learning and improvement. It creates an environment of adaptation to create better future outcomes. Ultimately, it can be an important tool for improving effectiveness, and foster a culture of learning.
Ben Walker is COO at ManageMen, Inc., a leading cleaning industry consultancy specializing in training, transitions, auditing and educational materials. He can be reached at ben@managemen.com.