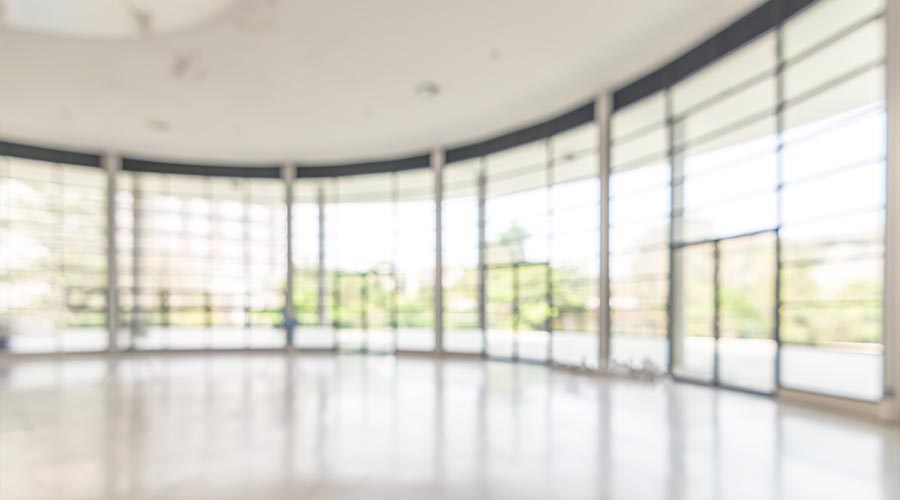
Throughout the COVID-19 lockdown period of the pandemic, Chicago Public Schools (CPS), like many other districts, investigated and tested different solutions to help ensure building occupants felt comfortable enough that buildings were safe for occupancy. Initially, teams worked quickly to implement short-term strategies to address various concerns. That included partnering with third-party technical auditors to inspect ventilation equipment in all spaces, conducting air quality sampling within all schools, and establishing a greater emphasis on air quality control with facility field teams. Subsequently, CPS created standardized processes that are used today to proactively manage indoor air quality (IAQ) issues and keep CPS teams focused on figuring out the best solutions to continue operating effectively moving forward.
The first IAQ strategy implemented was creating an annual air quality sampling program to help the CPS environmental team identify potential IAQ issues. To do this, CPS partnered with three managing environmental contractors (MECs), each assigned to a region within the district. Annually, each MEC takes a sample of the air during occupancy in 25 percent of our rooms, does a 100-percent visual inspection of all rooms, and posts the results on the CPS website (www.cps.edu/AIRQuality).
If any sample readings are identified as above what would be acceptable, the MEC partners develop a scope of work for the CPS facilities teams to use to address the issues causing IAQ problems. The MEC partners then work with our facilities teams and any contractors we bring on board to rectify the problems, ensure that the repairs are handled properly, and not lead to any other environmental concerns within the building.
CPS's second strategy was to develop a quarterly preventative maintenance IAQ sampling check. This is where building engineers collect air quality data using handheld IAQ measuring devices. This portable air quality monitoring device measures PM2.5 and PM10 (both are types of particulate matter), CO2 concentrate, temperature, and humidity. Any readings that our onsite engineers capture as above acceptable levels are reported to the CPS environmental team, who then deploy the MEC to conduct site visits. They will investigate the situation further and develop a recommended scope of work to mitigate any issues found.
This strategy has proven to be a cost-effective way to capture air quality data more frequently. It is now a standard part of our preventative maintenance program.
The third strategy is currently in the pilot phase and is focused on using onsite IAQ sensor technology to collect real-time air quality data within our facilities. During the research phase, we reviewed possible device solutions for this pilot. Our teams looked at several different permanently mounted solutions that would meet multiple needs. We also sought help from IPVM, experts in physical security technology, which had a comparison study on the effectiveness of IAQ monitoring solutions.
We settled on a device based on the effectiveness of the sensors that we tested. These were compared against the IAQ testing tools our environmental contract partners use, as well as the technical requirements that we needed from an IT infrastructure perspective. Those requirements included:
-
Google single sign-on requirement
-
Validation by our information security team that the devices had no or low possibility of a threat
-
Could support simple network management protocol updates so our network monitoring tools could monitor and manage them
-
Must integrate into our network monitoring tool
-
The solution had REST API support (representational state transfer application programming interface — allowing two computer systems to securely exchange information over the internet)
-
The solutions provider had an uptime (the amount of time the server is available) of 99.99 percent
-
Centralized maintenance tools (also known as computerized maintenance management systems, or CMMS)
-
BACnet (Building Automation and Control Networks) compatibility native with the devices
-
Local vendors that could receive/warehouse/configure/deploy the devices
It was understood from the beginning that CPS wanted a holistic technology solution that met CPS's technical requirements and provided the flexibility to integrate with multiple other technology devices that CPS was already managing. Most vendors selling the devices provided a SaaS (Software as a Service) dashboard. However, this was limited to hosting their own devices, restricting us from expanding this program to integrate our current suite of technology solutions.
Based on our research and our need for flexibility, we ended up partnering with two vendors. One provided a product for combining BAS (Building Automation System) data and IAQ data dashboards. The second offered a platform for centralized aggregation of the IAQ views.
Today, the CPS IAQ remote monitoring pilot sensor solution is installed in 12 buildings, with 12 to 15 more slated for this capital year, depending on funding support from the budgeting team. This initiative represents a significant step forward in our commitment to ensuring the health and comfort of our building occupants. As the program has been rolling out the initial pilot sensors in these 12 buildings, facilities were chosen to represent a variety of design styles from our portfolio, including two administration facilities.
The technology and strategic set have provided our teams with the tools necessary to monitor and manage issues before complaints are provided proactively. Occupants in a few of the buildings have complained about the air quality over the years, and it was challenging to convince them that there were no risks or concerns — even with air sampling results from environmental consultants. Now that there is continuous data that can be shared with building occupants and leadership, it has proven to be a great tool to help create staff confidence in the current state of IAQ in these buildings.
As progress continues in this pilot program, there are considerations to add a few additional device manufacturers into the mix. When added to the BAS specifications, it will replace the traditional temperature/humidity/CO2 stats and allow for enhanced operating sequences. All-in-all, we are close to having a solid foundational systematic technology solution in place that will allow CPS to scale through the district as resources become available.
About the Authors/Program Owners
Rob Chistlieb — CPS Executive Director of Facilities
Robert is the Executive Director of Facility Operations for Chicago Public Schools. As Executive Director, Rob oversees the district's facilities maintenance and environmental health and safety programs. Rob has been instrumental in creating the vision and leading his teams to develop and enhance IAQ and ecological programs. Under Rob’s leadership, Chicago Public Schools joined the Healthy Green Schools & Colleges program.
Richard Schleyer — CPS Director
Richard is the Director of Environmental Health and Safety at Chicago Public Schools and oversees and manages all district environmental program standards and efforts. He and his team manage an extensive environmental health and safety program and have played a vital role in developing and managing the current IAQ programs.
Paul Valente — CPS Automation Architect
Paul, the Automation Architect for Chicago Public Schools, oversees the district's management, upgrading, repair, and installation of all Building Automation Systems (BAS) and IoT systems. He plays a key role in coordinating specifications and consolidation efforts, focusing on integrating advanced technology to modernize the district’s controls and management systems.
Brian Martin — Deputy Program Director CPS PMO
As Deputy Director of the Chicago Public Schools Project Management Office, Brian is vital in working with CPS teams to develop and manage the program governance and standards for Chicago Public Schools' facilities maintenance and capital renovation programs.