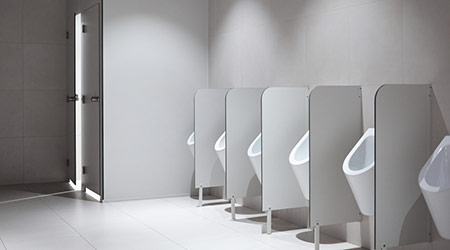
I can remember the day vividly. It was a spring morning in 2006. I was in San Diego to get started on a consulting project with a new client. At the time, they were preparing to open up a brand new, state-of-the-art building and wanted me to be there on day one to make sure that their new $100 million building would be cleaned using the best methodologies possible.
The facility — a stunning achievement of architecture — featured the latest and greatest in sustainable materials, and was designed to have the lowest possible environmental impact on the community in which it had been built. Everyone was proud of the accomplishment, and they should have been. It was a testament to a successful corporation that wanted to give back to the city it called home.
As I walked through on the first day of performing my usual first-day-on-the-job tasks, I encountered something that I’d only read about in magazines and heard of in presentations: waterless urinals.
“Marvelous!” I thought to myself. “They’ll reduce water usage by (whatever number the case studies said that I’d read at the time).”
I went about my business: counting fixtures, measuring spaces, counting stairwells and stairs. I went to the top floor and walked down sequentially to determine ideal routes. I entered my numbers into my spreadsheet and left town knowing that I’d done an amazing job for my clients.
Little did I know that there was a brutal storm ahead.
You see, I was still quite young (not yet 30) and just getting my feet wet as a consultant. I hadn’t yet learned to ask — as I was about to — the holy grail of all questions that needed to be asked when addressing new facility-related wizardry: “Great, but how do you clean it?”
What I was about to learn was a formative professional experience.
About three months into the new project, I started dealing with something I hadn’t yet had to face in my young career: complaints. Not the usual kind either. These were new and of the “restrooms are disgusting” variety.
What had happened, I found, is not only were the custodial crew members struggling to keep the new waterless urinals clean, but a very pungent odor was beginning to overtake the facility. It was faintly reminiscent of a goat farm crossed with an ammonia spill.
What happened here was a similar phenomenon to what has happened in many custodial departments. While waterless urinals offer huge benefits to an individual organization’s sustainability goals, they also require different cleaning procedures than traditional fixtures and can be a frequent source of headaches for the staff in charge of cleaning them. While the cleaning procedure for waterless urinals isn’t difficult, it’s an additional process that managers need to be aware of.
Most manufacturers of waterless urinals will include cleaning/maintenance procedures in their instruction manuals, so make sure to have those handy (I find that many custodial managers don’t). Most of these procedures are also available online, along with some additional tips for janitorial crews to guarantee the waterless urinals get properly cleaned every day.
First — and this is a very important first — make sure that the staff is using the proper chemical recommended by the waterless urinal manufacturer. Some recommend specific brands. However, in lieu of adding yet another chemical to the cleaning inventory, most recommendations are usually for either germicidal cleaners or all-purpose cleaners. Make sure the staff is using the proper dilution and that they’re applying the chemical using a sprayer.
Second, train staff to spray the interior surface with chemical, taking great care to avoid chemical run-down into the cartridge (chemicals other than urine and water will ruin them). To simplify this step, some prefer to remove the cartridge altogether when cleaning. However, if the fixture has recently been used, the cartridge may still contain residual fluids, which the staff won’t want to spill all over themselves, the cart or the surrounding floor area. Teach staff to use caution when tackling this step.
Third, using a cotton cloth or microfiber towel, have staff wipe down the interior of the urinal top-to-bottom. It’s important to remember here to not use paper products to wipe. While paper towels are terrific for absorbing moisture from hands, they’re ineffective as cleaning tools. They also absorb very little moisture before becoming saturated.
Finally, take note of the type of cartridge used and when it was installed. Different manufacturers have different recommendations for replacement — usually within the window of 3 to 6 months. If cleaning teams start receiving complaints about odor, chances are it’s time to change. Keep enough inventory on hand to facilitate changes and make sure that crew members responsible for restroom cleaning understand what to do when maintenance is necessary.
There might be specific steps, for example, to removing cartridges and additional steps to installing. Some fixtures also come with a unique key to provide access to cartridges. If left to their own devices, untrained workers could damage the units.
As sustainability has become the status-quo for the design of modern facilities, so has the need to understand how to properly maintain these elements. Making sure the cleaning team is aware, included and prepared to address sustainability initiatives is paramount to the development of these newer technologies.
Ben Walker is the COO for ManageMen, Inc., a leading cleaning industry consultancy specializing in training, transitions, auditing and educational materials. In addition to his consulting work, Walker is the author of ISSA’s best-selling book: 612 Cleaning Times and Tasks.