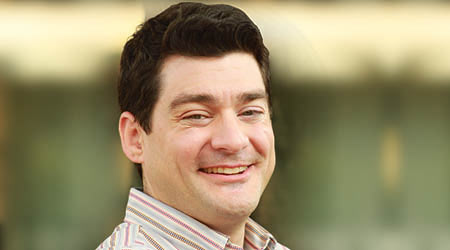
The third side of the cleaning triangle, after staff and chemicals, is cleaning equipment. Since tools and equipment are purchased less frequently than consumables, and represent significant embodied resources, it’s important to keep them in tip-top shape so they last and continue to work properly. Here are a few things to consider before purchasing.
Find hand tools that your staff will actually use, ideally with staff input, before you make major purchases. Consider attributes such as tool weight, ergonomics, length/reach, ability to adjust for the height of staff, warranty and availability of user-serviceable replacement parts.
Even once you’ve decided on a particular type of equipment, you can still try out several models to get staff input. Obtaining new equipment that will be used is more preferable than having staff revert to using old equipment and cleaning the old way. Sometimes the staff input can provide very basic, but critical feedback, like whether cord length will be sufficient for all areas cleaned, or if there may be areas/doorways where the proposed new equipment won’t fit.
When investing in quality equipment, make sure the tools are designed for professional use. I’m sure I’m not the only one that’s seen residential vacuum cleaners from a big box retailer being used in commercial facilities. Intended for vacuuming in a residential setting once or twice a week, it’s not surprising that these machines don’t hold up to the heavy daily usage by cleaning professionals.
On their way to wearing out, vacuums may churn through belts, end up with constantly clogged filters and beater bars, and have cords that detach or fray with heavy use — all things that, at a minimum, mean the vacuum is not cleaning properly and, at worst, may present a safety hazard. It may also be difficult to make warranty claims for actual defects if using residential machines in a commercial setting.
Once the right equipment is purchased, follow the manufacturer’s guidelines for regularly servicing and replacing items such as belts, fluids and batteries. All too often, we only pay attention to maintenance when there’s a problem with a piece of equipment. Preventive maintenance is usually much more cost-effective than dealing with down equipment that has a major, likely preventable, dysfunction.
Keep track of and follow the recommended schedules for changing fluids, cleaning battery terminals and filters, and replacing bags and belts. And while you may have a MacGyver on staff that’s a whiz with duct tape and baling wire, take the time to replace worn or frayed cords and missing screws and bolts.
Finally, when it comes to cleaning tools and equipment, size does matter. When my 38-inch lawn mower gave up the ghost, I purchased a 46-inch replacement. The extra 8 inches of cutting width on each pass means it now takes me about 30 minutes less time to mow the lawn.
It’s not hard to put a price on my valuable weekend time, and the same is true for your staff time. An extra few inches of mop, squeegee or autoscrubber width can add up to measurable time savings, as long as the equipment fits where you need it and your staff can properly handle the size.
MARK PETRUZZI is Senior Vice President of Outreach and Strategic Relations with Green Seal. He’s in his third decade of striving for more sustainable purchasing and operations by using his engineering powers for good.