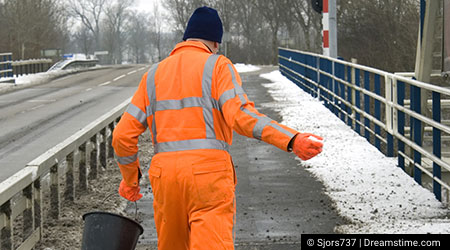
Before any salt is ever applied, it’s important for facility cleaning managers to establish a policy for clearing new snow accumulations — anything 1 inch or greater — prior to any de-icing application. This is important because clearing new snow accumulation first will prevent the overuse of ice melt products that typically occurs when staff attempts to ‘burn off’ the snow with salt.
Clearing snow includes plowing, blowing, shoveling and sweeping. Staff should be trained to relocate snow piles to areas that minimize the flow of water that may refreeze — warranting future de-icing applications of the refreeze. Managers should provide workers with documentation (i.e. Site Engineering Plan) of drainage and slope issues so they can properly place snow piles. Finally, make sure staff does not relocate or dump snow into bodies of water, such as lakes, ponds, rivers, streams, ocean, wetlands, storm water management ponds, etc.
Once snow is properly removed, staff can apply ice melt products.
Just as important as it is to have a policy for removing snow, facility cleaning managers should have a policy for ice melt. First, make sure to train staff on where to apply salt products. They must avoid salt-sensitive areas or zones that are protected by local, state/provincial or federal regulations.
The policy should also include the proactive prevention of snow and ice bonding on driving and walking surfaces as a standard practice. This is known as anti-icing. When implementing anti-icing techniques, it’s important to know the specific weather scenarios that exist where and when anti-icing may be ineffective (i.e. heavy rain, specific temperature conditions, etc.).
Also ineffective is a program that doesn’t include spot-treatment of problem areas. Facility cleaning managers should train staff to be aware of north-facing areas or areas where water and ice are known to build up. Spot-treating these areas should be standard practice rather than ‘blanket treating’ the entire exterior space every time, which can be costly for departments.
Finally, an ice melt policy should include an ice monitoring process, which would insure proactive and effective spot treatment, sometimes referred to as an ‘ice watch.’ This means ongoing monitoring and documentation of any refreeze-related risks caused by damaged or faulty infrastructure (i.e. broken downspout, clogged drain, etc.), with a focus on reducing the need for additional de-icing applications.
Using Salt Brine/Liquids
The use of salt brine (sodium chloride, magnesium chloride, calcium chloride, etc.) or other liquid de-icers (e.g. calcium magnesium acetate) — as a strategy for direct liquid anti-icing of paved surfaces and for pre-wetting solid salts for optimal efficiency of the material — are known best practices for facility cleaning managers to consider. Furthermore, solid salt optimization techniques include blended, pre-treated or pre-wetted rock salt with the goal of optimizing effectiveness to accelerate de-icing and/or lower the effective temperature of the salt.
Salt brine may also be utilized for pre-application of dry or solid salt supply, such as spraying piles, prior to applying solid salt proactively as an anti-icing application.
Keep in mind, the application of solid salt for anti-icing applications will experience some waste due to bounce and scatter while applying. Often there will also be further displacement by vehicle traffic.
Purchasing, Storing Salt In Preparation For Winter
Documenting Ice Melt Applications