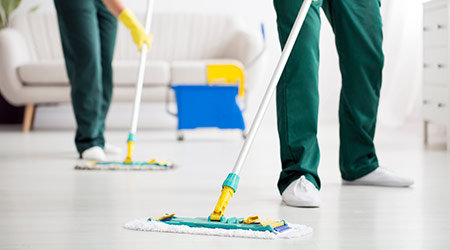
Bringing microfiber mopping to a facility can have measurable benefits, not only for the building itself, but also for the employees that handle the daily floor maintenance. Unfortunately, implementing new products and/or processes is sometimes easier said than done. Managers must take appropriate steps to streamline the implementation.
Setting clear goals helps in navigating the various topics that will come up during the testing of these new products. I had two goals in mind when bringing microfiber into daily use at Cosumnes River Community College, Sacramento, California: to save the amount of water used daily by the custodial staff and to improve employee ergonomics.
On average, one custodian will go through 9 gallons of water each day. A crew of 20 custodians would use 900 gallons of water each week just mopping restrooms and common areas. With a microfiber mopping system (non-charge bucket), a custodian will use 3 gallons each day, which brings the weekly total down to 300 gallons. In California, a savings of 600 gallons of water per week is huge. Our water savings goal had been achieved.
The second goal of employee ergonomics was just as important. The stress that is placed on the body of someone in the cleaning industry will have a lasting effect years after retiring. Whatever can be done to reduce the stresses from repetitive motion should be implemented.
Assisting Staff
When switching over to microfiber, it's important to be clear with staff that the change is happening. Clear communication and involving them in the process will help gain their support.
It's often easy for staff to focus on why a new system won't work and why it shouldn't be implemented. As an extension of this, it's important to remove the old mopping system when testing new options. Don't leave old tools in a cubby, closet or warehouse — take them away. If old mops are kept around, management will need to be very vigilant in making sure they aren't being used.
The next step in implementing microfiber mopping systems is selling the change in a way that will promote staff buy-in, which is already established by environmental and employee health improvements.
Staff must also be prepared for, and trained on, a difference in mop upkeep. Old wet mops can be sprayed off at the end of the shift and used the next day, and the old looped mop can be used for up to three months, maybe even longer. However, microfiber mops need to be regularly laundered.
Microfiber holds dirt very well, but if a microfiber mop is not cleaned properly, staff will notice that it isn't working as well as it should. Once issues occur with the mop's performance, staff must think twice about when the microfiber heads were cleaned last.
The best way to develop a system for determining when a mop was last cleaned is through an examination that takes place during a trial phase. Get a clear count of heads that will be used per custodian, each shift. Multiply that number by two and that is the number of heads that should be ordered per custodian. Half are used on the first day, then sent for laundering. On day two, while half are being cleaned, the second half are being used for cleaning tasks. This process will keep the heads clean and ready for use.
Additional color heads for other surfaces can enhance the cleaning of desktops, whiteboards or other flat surfaces. These heads need to be different colors so that mop heads used in restrooms are not the same as those used on lunch tables, for example. Proper training for each surface should be given verbally and written during the training on microfiber mopping systems.
Microfiber Promotes Efficiency, Ergonomics