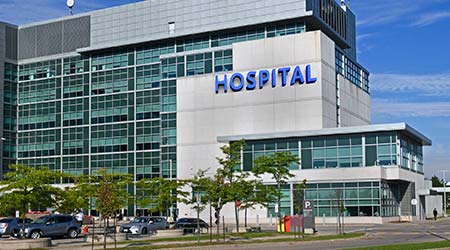
Contributed by AFFLINK.
Adventist Health System is listed as one of the five largest non-profit hospital systems in the United States. The organization has 46 hospital campuses, in 10 different states, and more than 78,000 employees. Further, Adventist is considered a full-service hospital chain. Along with traditional hospital services, the organization also provides urgent care centres, home and hospice services, and skilled nursing facilities.
Over the years, one of the ways the hospital has grown is by purchasing and taking over other hospitals. For instance, just last year the chain acquired a major hospital in Florida, making it the sixth hospital operated by the chain in the southeastern area of the country. While each branch must adhere to the same high medical standards of the Adventist Health System, it appears the organization has typically allowed the individual operations to retain considerable independence, with each hospital purchasing a range of supplies with little oversight.
“They lacked standardization, purchase reporting at each location, and it was not easy to determine how much each hospital was spending on supplies and other products,” says Marie Carr, AFFLINK’s director of healthcare. “This even included very basic things like trash liners used in the hospital.”
While trash liners are not normally a “big spend” item in a facility, if replaced each day or multiple times during the day in a large location like a hospital, they can become very costly very quickly. Further, the latest version of LEED — V4 — does not require the use of recycled or recyclable liners. This means hundreds of trash liners disposed of every week will typically end up in landfills, where they can take years, if not decades, to decompose.
Recognizing an opportunity for improvement, the hospital system set up a pilot program with Carr to help reduce these costs and by doing do, promote sustainability, in six of the chain’s 46 hospitals. To do this, Carr introduced administrators at Adventist to the ELEVATE process, a free online service developed by AFFLINK, which essentially allows managers to “take the roof” off their facilities and see what products and services are actually being used in each specific area of the facility.
Using the process, Carr and the administrators were able to determine exactly which liner sizes were needed for trashcans throughout the locations. Having too small or too large a trash liner is wasteful and usually costly. The pilot program went so well that Adventist worked with Carr to standardize the purchasing of liners in all 46 locations.
“Managing a complex supply chain across multiple facilities like this isn’t easy,” says Carr. “But working together and with the use of the ELEVATE process, Adventist Health System was able to standardize procurement procedures across all 46 facilities, resulting in cost savings just on liners of over $200,000 in just one year.”