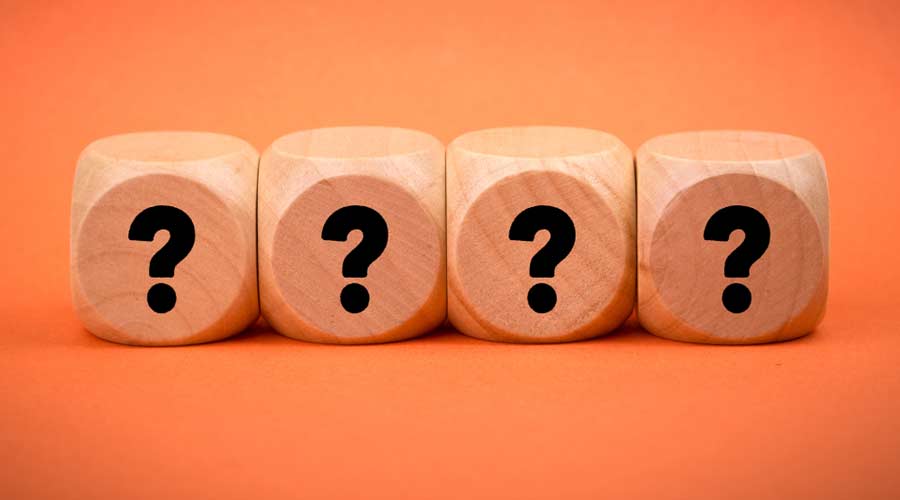
Prior to the pandemic, cleaning standards for buildings were mostly set through visual inspection. If a floor or surface appeared to have no visible dirt or soil, it often checked the box. The elevated scrutiny on cleaning and general hygiene from the pandemic, however, has shifted expectations to a higher standard. This silver lining of the past two years can lead to fewer instances of illness among occupants, but cleaning departments themselves have to commit to a higher standard of general effort and touchpoint disinfection.
To help in-house cleaning departments and building service contractors (BSCs) better evaluate themselves, Stephen Ashkin, CEO and president of the Ashkin Group, crafted four questions every department should ask regarding the gauge of their cleaning services and whether improvements are needed.
1. Are we cleaning the right spaces in the facility?
When it comes to the likeliness of spreading pathogens, some parts of a facility pose a far greater risk. By identifying different parts of the facility and assigning a degree of importance to cleaning and disinfecting, you can create benchmarks and performance data that ensure areas with high amounts of foot traffic or touch points are accounted for. Key examples of high-risk include restrooms, lobbies and break rooms.
2. Are we cleaning the right surfaces in those spaces?
Once areas of a facility are highlighted as higher risk for transmitting pathogens, departments should then specifically outline the greatest spots of concern. For example, cleaning frequencies for walls or ceilings are far less of a priority than door handles, dispensers, and stall locks in a restroom. With only so many hours in a day, making those particular spots a priority can be pivotal in keeping facilities safe.
3. Is the current frequency of cleaning sufficient or excessive?
Just because a contract indicates that a space needs to be cleaned once daily doesn’t mean that’s actually the optimal frequency. A break room, which Ashkin uses as an example, will likely need multiple frequencies compared to a personal workspace. To get a better idea of what spaces need varying frequencies, BSCs or in-house cleaning departments can use data for guidance.
4. Are we cleaning effectively?
An example of the aforementioned technology includes adenosine triphosphate (ATP) meters, which measure residue levels on surfaces. These meters can not only test the quality of work being done, but be used in a larger-scale data collection to determine which tasks are most important to ensuring occupant health.
For more from the Ashkin Group, check out this recent article on the bottom line benefits of sustainability programs.