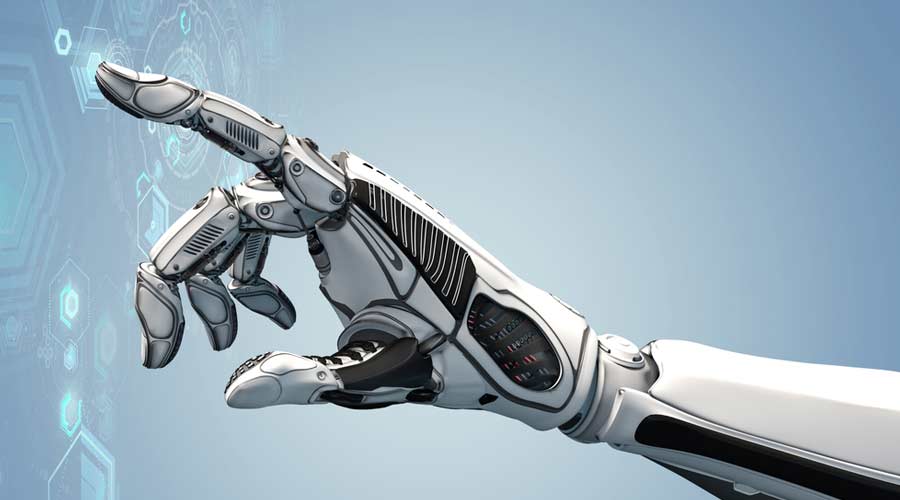
Contributed by Mike Sawchuk
This is the sixth and final article in the series discussing the five key pillars that drive significant, long-term improvement and enable cleaning operations to meet higher client expectations while providing the highest levels of clean, safe, healthy at the lowest overall cost.
Since COVID-19, cleaning operations — whether in-house or contracted — have been under intense scrutiny to ensure they are providing clean, safe, healthy environments. “If it looks clean and smells ok, it must be clean” — once the measure of cleanliness — has been set aside. Today, most building occupants and visitors are more likely thinking, “What dangerous pathogens may be lurking that we can’t see?”
So, how can cleaning operations ensure they are providing the highest levels of clean, safe, healthy at the lowest overall cost, especially amidst high employee turnover and reshuffling rates and the difficulty in finding the best people as we discussed in the previous article of this series? Robotics can help.
Robotic Benefits
When selected and used correctly—and with the first four pillars in place—robotics can help in a variety of ways, including allowing cleaning operations to:
· Clean more consistently with increased effectiveness, efficiency, and productivity
· Better cope with labor shortages
· Attract workers interested in using new technologies
· Allow current labor to do other less mundane and repetitive tasks and redirect them to higher value-adding tasks
· Increase worker satisfaction
· Enhance worker ergonomics
· Enjoy a relatively high return on investment (ROI) in a relatively short time, typically six to nine months
· Collect objective performance data to monitor areas such as productivity and quality assurance.
Not Your Parents’ Robotics
Robotic cleaners have changed a lot in the past few years. They are not the same as they were just five years ago. They are:
· Smarter
· More effective and efficient
· Quieter
· More ergonomic
· Available for a wider variety of tasks
· Simpler and easier to use.
The options have also multiplied exponentially. Today’s robotic cleaners come in every size, shape, and form and can clean virtually every surface. Floorcare robotics, such as programmable auto scrubbers, sweepers, vacuums, and combo units that can even sense spills to spot clean carpets are just the beginning. There are robotic UVC disinfecting devices, window-cleaning and roof-inspecting drones, self-dumping waste hoppers, even walking robots that do everything from cleaning to picking warehouse orders. The list of future robotics is as endless as the imagination and will continue to expand as technologies advance.
Five Robotic Considerations
While exciting, the number of options can be overwhelming when it comes to choosing the best robotics for their cleaning operation. With this in mind, the five considerations below can help facility managers and BSCs choose and adopt robotics appropriate for their cleaning operations.
Need. The first step before purchasing any robotics is to carefully analyze the need and compare robotics and manufacturers that could fill this need. This requires observing where results could be improved and, better yet, analyzing data. For example, using an ATP meter or fluorescent gel or imaging—or a combination of these technologies—might show that restroom sinks are not consistently and thoroughly cleaned. A robotic auto scrubber or vac could be the answer, and the workers who used to perform the service could be re-allocated to better cleaning the restroom. Or, similarly, it could be that a “smart” auto scrubber could improve cleaning quality while lowering overall costs over time. No robotic should be purchased just because they are “cool.” If a robot doesn’t improve the current operation by solving a specific objective, the money is best left unspent, especially since most are anything but cheap.
Improved Overall Effectiveness and Efficiency. Consider: Cleaning 53,820 square feet (5,000 square meters) daily generally would take 300 hours of manual labor monthly using traditional cleaning tools. It only takes some robotic scrubbers about 130 hours monthly to do the same work — a 230 percent efficiency improvement. The hours a cleaning technician spends on this task can be redirected to accomplish less routine, more labor-intensive, value-adding tasks or to add previously unprovided services.
Sustainability. Most facilities want to reduce their carbon footprint as protecting the environment becomes increasingly important to commercial entities and building occupants. Commercial cleaning robotic equipment uses less water and chemical than traditional cleaning methods. At the same time, today’s models are designed to be energy efficient, making robots attractive to customers and other stakeholders.
Safety. As most facility managers and commercial cleaning operations understand, cleaning can be more dangerous than people suspect. Today, robots are taking over many of the more hazardous duties. They are being used to protect workers from accidents and injuries caused by everything from falling off ladders and scaffolding to inspecting rooftops and cleaning confined spaces. This benefit is significant for operations looking to improve or maintain a good safety record.
Leadership. This may seem a distant consideration when it comes to robotics. However, some workers and unions fear that robotics will “steal” their jobs and are reluctant to welcome its use. In these cases, it could be a leadership problem that should be identified and fixed before adopting robotics. Leaders create enthusiasm for innovation. They allay fear by communicating accurate, timely information such as why a robotic is being considered, how it will benefit the workers, including how it will make their jobs easier and safer and reduce the more mundane, routine tasks, etc. Leaders encourage staff input, including onsite testing of potential equipment to help ensure buy-in. True leaders are also equipped to make tough decisions about employees who may be unable or unwilling to transition despite thorough training and coaching. Before adopting robotics is when to make sure those leaders are in place to ensure the transition goes smoothly. The chances of successfully integrating robotic innovations are slim without the right leaders. (See Pillar 4 to compare the qualities of managers and leaders).
Take It for a Test Drive
Once a need has been identified and the benefits of employing robots established based on the considerations above, it is vital to realize that not all equipment is created equal, especially in robotics. Facility managers and BSCs need to do their research, including having various prospective manufacturers and units demonstrated at their sites to test units out on their floor types and conditions, soil types and load, occupant constraints, and other real-life conditions. Models should also be tested by their own workers to collect their input and buy-in. In addition, there should be key business objectives, including key performance indicators (KPIs), to compare current operations to the same KPIs after each robot is tested.
Commercial cleaning robots — from multi-functioning robots in all sizes to improved artificial intelligence (AI))—are revolutionizing how we clean and maintain our businesses and public facilities. They are efficient, effective, and offer a safer, more sustainable, and cost-effective alternative to manual cleaning. While implementing these machines can be complex, the benefits far outweigh the challenges.
Want to learn how your cleaning operation compares to others, then use the information and insights to improve? Visit www.sawchukconsulting.com/the-short-quiz.
This is part five of a six-part series. Click here to read part 1, part 2, part 3, part 4, and part 5.
Mike Sawchuk of Sawchuk Consulting is a leading education and BSC cleaning operations consultant and coach. He assists BSCs and facility management leaders, helping them improve their outcomes with insightful, pragmatic solutions and comprehensive, integrated assessments for cleaning operations. He can be reached at 905-932-6501 or via LinkedIn at www.linkedin.com/in/mikesawchuk. Or to learn more about his and his company's expertise, visit www.sawchukconsulting.com.