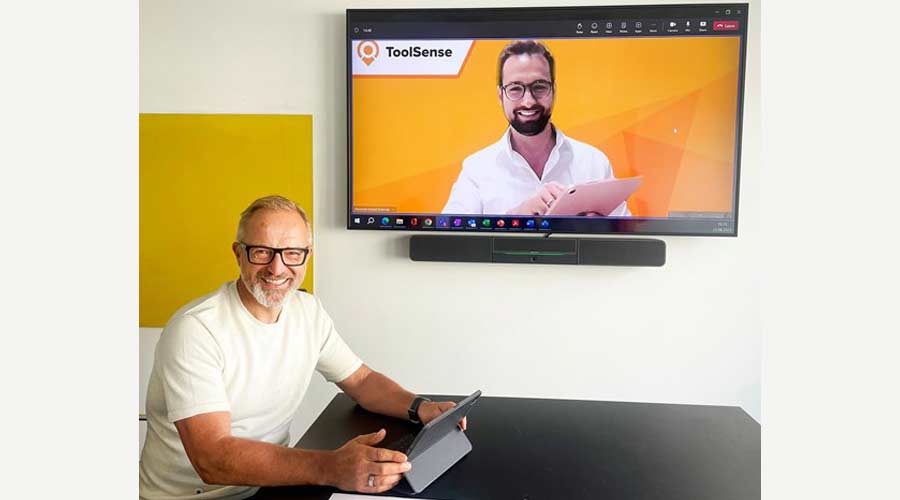
SS A/S, a global workplace experience and facility management company, is enhancing its leading technology position in the industry through a new global strategic partnership with tech startup company ToolSense. By leveraging state-of-the-art Internet of Things (IoT) solutions that can be integrated into ISS's management of the company's global assets of movable machines, ISS aims to boost its operational efficiency.
Every day, more than 300,000 ISS on-site employees are taking care of over 500,000 movable machines, such as vacuum cleaners, kitchenware and healthcare equipment, in more than 30 countries worldwide. The tracking, maintenance and utilization of these assets will now be optimised by the use of ToolSense's innovative Asset Operations platform, Internet of Things (IoT) solutions, and QR codes.
Boosting efficiency and consistent workflows
“As a cornerstone of our ambition to become the technology leader in our industry, we are firmly dedicated to building an ‘ecosystem’ of strategic partnerships and collaborations with innovative startups and suppliers who are pioneers in their respective fields. By digitizing ISS’s global asset management through ToolSense’s solutions, we will enhance the entire ‘life cycle’ management of our movable assets and boost our operational efficiency. For instance, we will gain a comprehensive overview of all our on-site tools and machines, including their utilization, maintenance needs, and potential upgrades. These data-driven insights will ensure that we always have the right equipment on hand at our customers’ sites, enabling a consistent workflow”, says Markus Sontheimer, CIDO of ISS A/S.
Digital solutions reducing workload and CO2 emissions
A crucial aspect of integrating ToolSense’s solutions is to digitise work processes that would typically be manually carried out by ISS’s on-site employees. Alexander Manafi, CEO of ToolSense, explains:
“Rather than maintaining an overview of local machines through laborious processes involving pen and paper or Excel sheets, employees will now have access to all relevant information and will manage assets through one single digital platform. This platform provides a machine-to-service connection for real-time communication, access to machine locations, and automatic run-time documentation. Furthermore, machine failures and upcoming maintenance are instantly recorded and tracked. On-site, employees can conveniently report issues by using QR-codes. This optimized life cycle management of ISS’s tools, including a better utilization of existing resources, will also positively impact CO2 emission reductions. We are very much looking forward to embarking on this journey with ISS.”
ISS and ToolSense initiated their local collaboration in Austria two years ago, successfully piloting the integration of ToolSense’s solutions into ISS Austria’s asset management processes. This collaborative effort has now culminated in the global strategic partnership, enabling the scaling of these solutions and approaches to a global level.