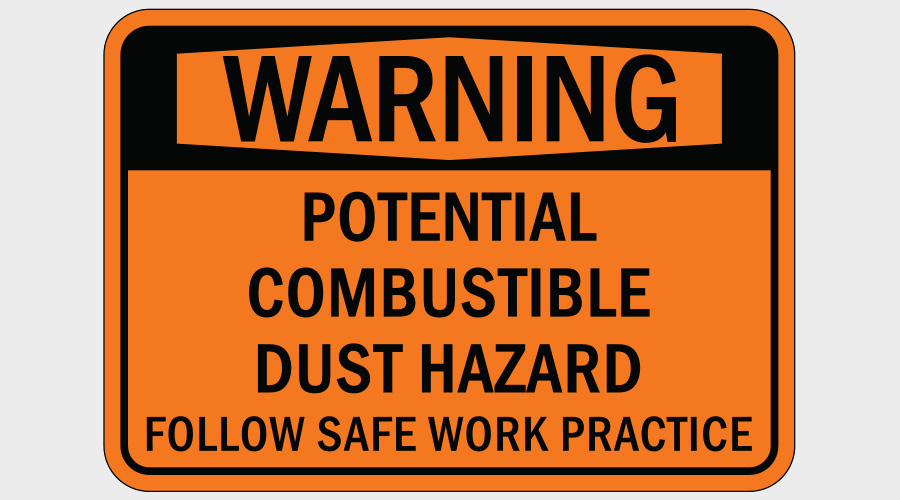
The National Fire Protection Agency (NFPA) has introduced a new standard, NFPA 660 Standard for Combustible Dusts and Particulate Solids, that consolidates several prior standards into one comprehensive, consistent document which applies to a variety of industries. This is intended to simplify compliance, reduce confusion and create a more streamlined approach to managing combustible dust hazards.
The NFPA 660 introduces a risk-based, performance-oriented approach, allowing tailored safety measures based on specific risks. The standard refines Dust Hazard Analysis (DHA) requirements within a unified framework, enhancing clarity and removing redundancies. Additionally, it includes industry-specific chapters to address unique risks.
“Making sure that our customers are purchasing the right equipment to safely address their environment and application has always been a top priority for us,” said Eric Potorski, Industrial Vacuum Specialist at Goodway Technologies. “Our robust and detailed consultation helps gather the necessary information to understand the material they are collecting, the environment and the disposal process. This thorough analysis is an effective, safe, and necessary standard to be compliant with your DHA.”
Goodway Technologies is providing next steps to help businesses comply with NFPA 660:
- Review the Standard: Familiarize yourself with NFPA 660 and understand how it applies to your facility.
- Conduct a Dust Hazard Analysis (DHA): If you haven’t already, perform a DHA to identify and mitigate potential hazards.
- Update Safety Procedures: Adjust your safety protocols and training programs to align with the new standard.
- Invest in Proper Equipment: Ensure you have the right dust collection, ventilation, and housekeeping systems in place.
- Work with Experts: Consulting with combustible dust safety professionals can help streamline compliance and enhance workplace safety.
“This unified standard helps facilities proactively identify a more consistent approach to hazard management,” said Potorski. “Our team can provide consultation to help incorporate routine maintenance and find the right solutions for the right applications.”
To help reduce potential hazards associated with combustible dust explosions, facilities can also implement the following best practices.
1. Ensure access to all hidden areas of the facility. Evaluate dust buildup on every horizontal surface, including ductwork, beam and joist surfaces, and areas above suspended ceilings.
2. Frequently inspect for dust. OSHA inspectors look for accumulations of 1/32 of an inch, which is about the thickness of a standard paper clip. Immediate cleaning is necessary when a layer of that amount covers a surface area equal to 5 percent of the floor area.
3. Implement regular cleaning intervals. Develop a plan for timely cleaning, ensuring that work cycle dust is removed concurrently with operations and not allowed to accumulate. Be cautious of dust dispersion during housekeeping.
4. Relocate dust collectors outside. Dust collectors with a volume greater than 8 cubic feet should be situated on the exterior of buildings to limit risks.
5. Ensure electrical wiring and equipment are approved for dust hazard conditions. OSHA recommends using proper electrical equipment in hazardous locations to eliminate a common ignition source.
6. Use certified industrial vacuums for picking up explosive material. In hazardous dust environments, "explosion-proof vacuums" approved for Class II conditions should be used to prevent sparks.
7. Control ignition sources. Post "No Smoking" signs, control static electricity through bonding and grounding equipment, and provide necessary personal protective equipment to prevent ignition from static electricity.
8. Perform regular preventative maintenance on equipment. Faulty equipment is a common cause of ignition.
9. Train employees to recognize and prevent hazards. Proactively train new employees before they start work and periodically refresh their knowledge. Employees should understand safe work practices, as well as plant programs for dust control and ignition source control. Encourage employees to report unsafe practices and foster a company culture of safety. If fine dust, powders, or other flammable materials are used in the facility, consider implementing these tips to enhance preparedness.
While this information can serve as a reference, it is important for plant and facility managers to discuss best practices with their safety officer or maintenance personnel before selecting equipment or implementing safety and preventative maintenance measures.