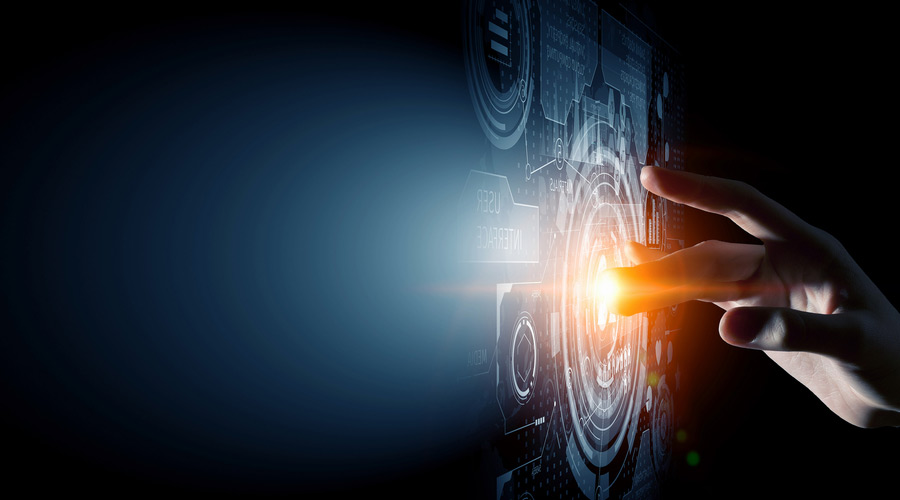
This is the second of a six-part series by Mike Sawchuk on the five key pillars that will drive significant, long-term improvement and enable cleaning operations to meet higher client expectations while providing the highest levels of clean, safe, healthy at the lowest overall cost.
A couple of weeks ago, we discussed Why, When & How Cleaning Operations Should Consider Implementing New Technologies. This week, let's look at 11 technologies that cleaning operations — whether in-house or a building service contractor (BSC) — should consider implementing. Many of these are relatively inexpensive and easy to implement. Some may already be in place. However, the tips below are worth reviewing to ensure proper use.
1. Microfiber cloths and mops. While familiar to leading operations, the quality of microfiber matters. Many factors impact how microfiber picks up and holds soils, bacteria, and microbes, including the overall quality, how the fibers are split, the size of the fibers, and how they are stitched. How microfiber is used is also essential. It should be color-coded by task and area, and wiping should be in one direction (not in circles or back and forth) to prevent cross-contamination. Cloths should be presoaked versus spraying and wiping and folded in quadrants to ensure a clean quadrant for each wipe. Proper laundering is essential, which includes never using bleach and fabric softener or washing microfiber with cotton cloths or mops.
2. Electrostatic sprayers. Not all electrostatic sprayers are engineered the same or work the same. Always use a disinfectant with the viscosity of water and the safest formula possible for humans, the environment, and the assets being disinfected (always avoid spraying quats!). Also, users must be trained properly, including how far away they need to be when spraying, how fast to move the wand, how much solution to apply, and how to purge the lines before and after use. Disinfectants are registered with the U.S. environmental protection agency (EPA) as pesticides for a reason, so it is vital to avoid misuse and overuse. It should be emphasized to users always to follow the manufacturer's instructions, especially if a clear water rinse is required.
3. Floor care. Dual buckets with separate clean and waste solution compartments are far preferable to single buckets for mopping. However, using auto scrubbers and mini or micro auto scrubbers is always preferable over mopping. Where resources allow, alternatives, such as steam cleaners; or spray, scrub, vac, and dry no-touch equipment, should be considered.
4. Disinfectants. Essential aspects of disinfection are:
- A. To not rely on the continuous use of any one active ingredient because bacteria and other pathogens can get used to them, leading to "superbugs." Meanwhile, not all disinfectants are effective against all pathogens, especially spores, certain viruses, and fungi.
- B. The safest disinfectant possible that is effective against what is being targeted should be chosen. These newer, safer disinfectants include hydrogen peroxide, NaDCC, and hypochlorous acid. Certain steam vapor cleaning devices using no chemicals, just tap water, are also EPA-approved to disinfect effectively. However, there are many false and misleading claims being made by some steam vapor manufacturers, so buyer beware. For proven disinfection claims, ensure the product has an EPA Establishment Number as well as third-party, scientific, peer-reviewed studies that list the specific device and technology and all kill claims.
5. Sustainability. The COVID-19 pandemic put environmental considerations temporarily on hold, but it’s back with a vengeance with people wanting products that are proven safer for humans, animals, and the environment, such as bio-enzymatic products and bleach/disinfectant alternatives such as those mentioned above. Independent third-party, multi-criteria green certifications such as Green Seal and EcoLogo will likely grow in importance. Recycling, upcycling, and proven landfill diversion claims will continue to gain momentum. So, too, will products made from sustainable sources, such as bamboo and other plant-based materials, and products that use fewer resources, such as coreless toilet paper and reduced packaging. BSCs and in-house departments would be wise to research technologies that speak to the concerns of their customers.
6. Residual antimicrobial surface protection. This technology falls into different categories: The adhesive type is like a sticker that adheres to frequently touched surfaces such as doorplates, elevator buttons, and airport check-in machines. The second are antimicrobial formulas that are applied to surfaces, activated by sunlight or a chemical reaction to extend effectiveness. Surfaces made of metals such as copper or silver have intrinsic antibacterial properties. It is important to note that these products typically only address bacteria but are ineffective against viruses or fungi. These products have their place in cleaning with their 24-hour to 90-day residual antimicrobial claims.
7. Robotics. It seems these days, people have different ideas of robotics. On the one hand, you have programmable auto scrubbers, sweepers, and vacuums in various shapes and sizes. Many of these have laser mapping capabilities that guide them around furniture, tell them when they are moving from hard flooring to carpet, and even detect spills. The newest emerging robotics includes everything from UV-C devices and drones for cleaning windows and some large spaces to self-dumping hoppers and walking robots programmed to clean restrooms or pick warehouse orders. A few notes of importance: Today's robotics are far advanced compared to what they were even five years ago, so don't discount them based on past performance. Equally important before purchasing robotic equipment is to pinpoint the business objectives the equipment will fill.
8. Touchless. Since COVID-19, conventional wisdom says the less touching of surfaces, the better. This area has advanced dramatically in recent years to include everything from hand soap, sanitizer, and towel dispensers and automatic flushing toilets to doors, lighting, and elevator buttons. This trend will continue to advance, providing healthier environments for cleaning personnel and building occupants.
9. Internet of Things (IoT). The world is increasingly connected through smart technologies, including the cleaning industry. IoT can produce greater efficiencies in nearly all areas of a cleaning operation—from digitized paperwork and janitorial software to better manage the refilling of consumable products, such as hand soap, sanitizer, and toilet tissue to cleaning frequencies and labor management. Like robotics, the key here is to have a clear picture of what and how IoT will achieve specific business goals.
10. Cleaning operation assessments. Compares a cleaning operation to best-in-class. Regardless of the current pain point(s)—an inability to find enough qualified people, high employee turnover or customer churn, need to improve cleaning results — assessments will help. A good assessment will identify where, what, how, and why improvements should be made to help reduce or even eliminate pain points. In addition, assessments help build consistency in providing the highest levels of clean, healthy, and safe at the lowest overall cost. These assessments once required hiring a consultant to conduct in-person evaluations and weeks of onsite training. Thanks to technology, facility managers and BSCs can learn to conduct in-depth online assessments, starting with a brief survey.
11. Indoor air quality (IAQ). The COVID-19 pandemic brought many emerging technologies promising to improve IAQ into focus, such as UV-C, various types of bipolar ionization, and selective ionizations. There are also new, energy-saving advancements in facility units. However, these technologies can be costly, and some can't be installed in older HVAC systems. With this in mind, there are less expensive ways to significantly improve IAQ using a multi-layered approach, starting with having the facility's HVAC and air ducts inspected annually and cleaned regularly. Additional measures include upgrading the effectiveness of the HVAC filters by increasing their MERV rating or using a different, more effective filter membrane and changing them regularly. Another critical component is using sensors to monitor IAQ key performance indicators, including temperature, humidity, particulate matter, CO2, total VOCs, and possibly ions. The sensors' findings can pinpoint areas where and when adjustments should be made, which can include simple actions, such as opening windows, incorporating fans, or adjusting humidifiers/dehumidifiers.
Once thought to lag behind other industries when it comes to adopting new technologies, the cleaning industry is making up for lost time. Those that do not keep up risk being left behind. Keeping up with the latest innovations can save time, and labor, reduce employee fatigue and turnover, improve cleaning outcomes, and even cut costs. Most importantly, they can contribute to improving the employee and customer experience. Smart BSCs and facility managers will keep abreast of these new developments and eagerly adopt those that will bring these positive results.
This is part two of a six-part series. Click here to read part one.
Mike Sawchuk of Sawchuk Consulting is a leading education and BSC cleaning operations consultant and coach. He assists BSCs and facility management leaders, helping them improve their outcomes with insightful, pragmatic solutions and comprehensive, integrated assessments for cleaning operations. He can be reached at 905-932-6501 or via LinkedIn at www.linkedin.com/in/mikesawchuk. Or to learn more about his and his company's expertise, visit www.sawchukconsulting.com. Contact him to find out more about conducting a cleaning operations assessment.