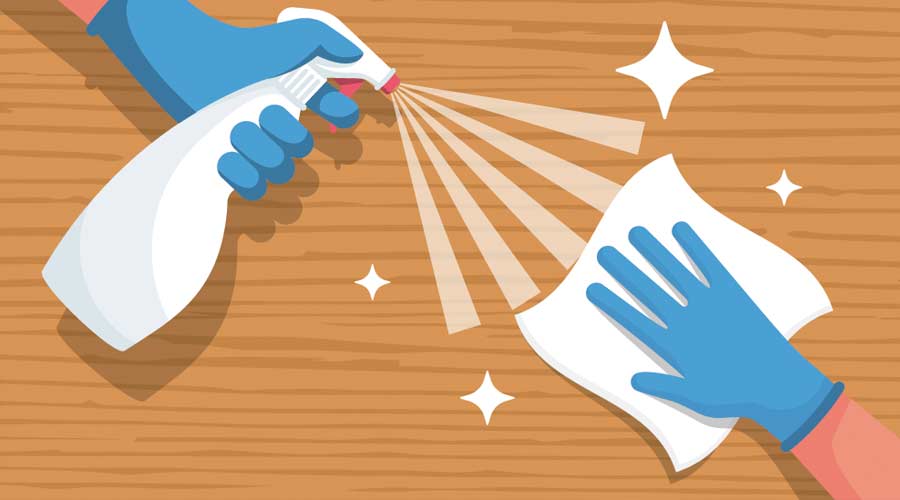
While the paranoia surrounding COVID-19 is far from its 2020 peak in many aspects, it’s still a common practice for many facilities to both implement and advertise high levels of disinfectant usage for occupants in a way to dispel concerns. While admirable in theory, green cleaning industry expert Stephen Ashkin of The Ashkin Group points out that when used irresponsibly or incorrectly, disinfectant usage can actually have an adverse affect on occupant health — even if used on key touchpoints.
In a recent article, Ashkin points out some key concerns surrounding disinfectant processes, as well as whether green cleaning is getting proper attention in facilities.
• Clean-Then-Disinfect process. Frontline cleaning staffs must pay attention to the capabilities of the disinfectant being used. If a product is both a cleaner-and-disinfectant, then in theory the process can be single step. If a product is simply a disinfectant, however, then surfaces must first be addressed with a neutral cleaner to properly complete the ‘clean-then disinfect process’. Ashkin also notes that if just disinfectant is applied to a surface first, then the entire process must be repeated if it dries.
• Deciphering disinfectants fromsSanitizers. A disinfectant is designed to kill pathogens or bacteria linked to causing diseases as indicated by the label, while sanitizers typically destroy all bacteria or pathogens entirely. Depending to the facility type in question, such as foodservice or healthcare, facilities should realize whether or not a disinfectant or sanitizer is necessary for proper infection control.
• Pay attention to dwell times. Whether or not a disinfectant is correct for a particular surface can be irrelevant if it’s not given the appropriate time on the surface before being wiped off. Make sure frontline cleaning staffs are aware of how long surfaces need to be wet for disinfectants to work, as indicated on the label. Dwell times often range between 5-10 minutes to fully kill organisms.
Green Cleaning Considerations
While Ashkin notes that the Environmental Protection Agency (EPA) doesn’t allow for disinfectants or sanitizers to have official ‘green’ claims, there are still some best practices to adopt.
• Consider pH in selection. When feasible, frontline staffs should aim for sanitizers and disinfectants that are as close to neutral (pH 7) as possible. More extreme products, which are determined by the further away they are from 7, increase the chance for skin irritation, burning and eye injuries if employees are unintentionally exposed to them.
• VOCs can pose similar threats. When considering selection of sanitizers and disinfectants, also study the label for the amount of volatile organic compounds (VOCs). Choosing options with fewer VOCs can reduce the chance of respiratory problems for both frontline staff and occupants alike. Even when used outdoors, they can be evaporated and be harmful to people and the environment.
For the complete article with insights from Ashkin, click here.