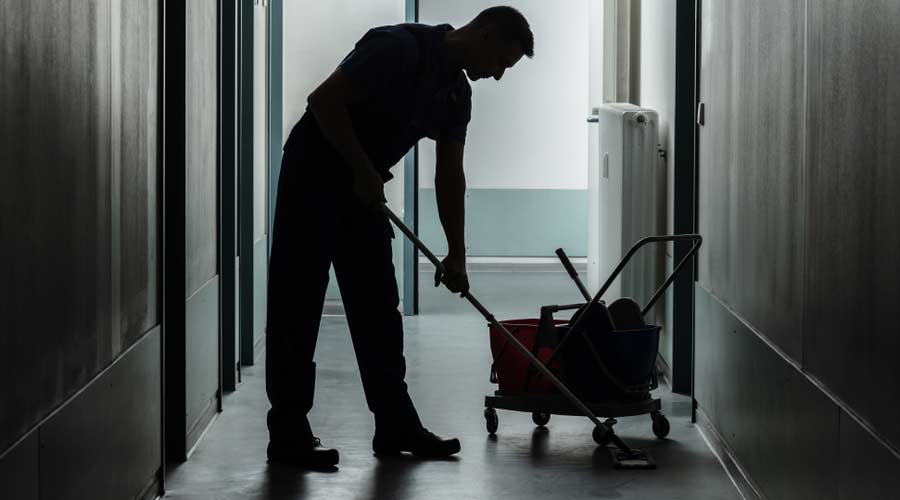
Nobody ever said that the cleaning and maintenance line of work is easy; workers often spend entire shifts on their feet, lugging equipment from room to room and floor to floor, plugging and unplugging wires, replenishing chemicals, measuring out proper dilutions, cleaning up spills, pushing vacuums and swinging mops, among many other things. Employers are constantly looking for ways to make the job easier on their employees and more appealing to new hires. Enter the magic word: ergonomics. The term itself has been bandied about for years – but what does it really mean? There’s a general assumption that when a tool is “ergonomically correct”, it’s better for the worker. But how? How can being mindful of this concept eventually pay dividends in the workplace? Here are some key things to know when it comes to ergonomics.
• Cleaning and maintenance workers deal with a lot of workplace hazards; from electrical shocks to chemical mishaps, cleaning can be a risky business. The American Journal of Industrial Medicine conducted a study recently revealing that incidents of workplace injuries or illness are on the rise compared to previous studies, with a nonfatal injury or illness rate of 107.5 per 10,000 – which is significantly higher than the 89.5 per 10,000 of “private industry” as a whole.
• “Ergonomics” itself is a fairly recent term. It’s known as “the study of human abilities and characteristics which affect the design of equipment, systems, and jobs.” It gained in popularity in the United States in 1957, when the Human Factors Society was formed, and the US Military placed particular emphasis on “human factors engineering”, a unique perspective on engineering and development that considered the human as having a “role” within a defined system.
• Generally, ergonomics centers around making the products and equipment comfortable for the worker, and not forcing the worker to accommodate the equipment. This includes buying vacuums with quality grips, adjustable handles to accommodate different worker heights, considering the weight of the equipment that will be used in repetitive motions, monitoring the noise output, reducing the amount of heavy buckets and mops that need to be carried, and more.
• Sound also falls under the category of “ergonomics” as it relates to worker comfort. When a machine puts out considerable noise for an extended period of time, and the worker doesn’t have proper ear protection, the constant noise can cause a form of fatigue, wearing the worker down faster. This can result in long-term damage, but also cause real-time challenges. If workers need to shout to be heard, it can increase stress levels and wear the employee out faster. Ergonomics can affect mental fatigue as well as physical strain.
• Training can help with better ergonomics. Monitor the types of movement workers are making during their routines, and adjust cleaning processes or look for equipment solutions as necessary. Pay particular attention to the main types of movement that cause problems: workers hunched over equipment that’s too tall or too short (they should be able to stand upright and look ahead, not stare down at the spot they’re cleaning). Make sure they can operate their tools with a relaxed grip – too tight of a grip causes stress and puts pressure on joints and ligaments. Provide carts for the transportation of heavy trash bags or tools that need to be moved from one place to another. Teach workers to move side-to-side with their feet when mopping and sweeping instead of swinging the upper body. Little things make a big difference.
Jackson Silvanik is the Managing Editor for Contracting Profits, and lives and works in Lexington, Kentucky. He joined Trade Press Media in 2021 and also edits and writes for Facility Cleaning Decisions, Sanitary Maintenance and CleanLink.com.