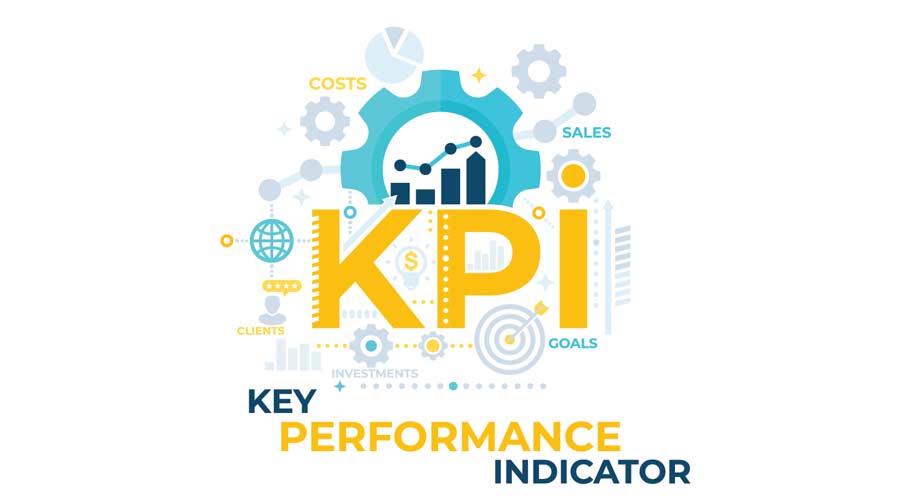
This is the third of a six-part series by Mike Sawchuk on the five key pillars that will drive significant, long-term improvement and enable cleaning operations to meet higher client expectations while providing the highest levels of clean, safe, healthy at the lowest overall cost.
In our last article, we discussed the need to be open to adopting new technologies. This was the first of the five pillars to drive significant, long-term improvement. These pillars can enable cleaning operations to meet higher client expectations while providing the highest levels of clean, safe, healthy at the lowest overall cost. This week, we will cover Pillar 2, the importance of high-quality data. This includes the collection, tracking, reporting, monitoring, and acting upon data to constantly drive improvements in results and operations.
There are many resources facility managers and building service contractors (BSCs) can use to ensure they have accurate and valuable data. First, however, let’s look at some areas where this data can improve decision-making and overall cleaning operations.
Employees. Data can be used to help make informed personnel decisions. It can be used to track employee-turnover rates. High employee turnover and a low net employee promotor score can signal a serious culture problem, where employees are eager to leave, only staying until they find something better. Or, it can signal poor recruiting and hiring.
Similarly, many companies have employee referral programs, which pay employees for encouraging others to work for the company. But how many companies track these programs to see if the money spent is worth it? Do the new hires become top-quality employees and stay, or do they leave quickly, leaving the operation with the expenses of rehiring and training?
Cleaning quality. Data can be used to ensure cleaning teams meet their clients’ expectations by monitoring everything from cleaning results and scheduling to supply refill processes and the number of customer complaints.
Cleaning frequency. If restroom cleaning is scheduled five times daily, but data shows there is no traffic after the third cleaning, the last two are a waste of time, labor, and product, costs that add up considerably over a year or even a month.
Products and equipment. Along with unnecessary cleaning frequencies, data can expose other waste, such as inaccurate dilution rates and over product saturation. Tracking product inventory can also help eliminate the purchase of products that are no longer used and help avoid the expense of disposing of outdated products. Meanwhile, monitoring usage and maintenance schedules can help keep equipment in good, operational condition and help prevent expensive repairs and even lawsuits from injuries caused by poorly maintained equipment.
Labor savings. Automated tracking, measuring, and reporting information through software eliminates hours of manual input.
One, Two, Three, Go!
While agreeing that data is king, many cleaning operations struggle with where to begin. The three steps below can ensure they have the data necessary for better decision-making and overall improved cleaning results.
1. Assess. As mentioned in my previous article, the key place to start is with an integrated and comprehensive assessment of your current cleaning operation and how they compare to best-in-class. A thorough assessment identifies current standings and where, what, how, and why improvements should be made. In addition, assessments help build consistency in providing the highest levels of clean, healthy, and safe at the lowest overall cost. The assessment is the foundation for obtaining the quality and quantity of data that leads to better decision-making. Thanks to technology, facility managers and BSCs can learn to conduct their own in-depth assessments online, starting with a brief survey.
2. Digitize — then digitalize. Once the assessment is complete, the second step for those who have not done so is to digitize all paper documents — then digitalize those processes that can benefit from doing so. Both of these should be used when incorporating data for better decision-making.
Digitization is the process of transforming information from a physical format (paper) to a digital version. All critical processes and communications can be tracked, measured, monitored, and reported far more easily by today’s software than manually on paper (not to mention the kudos earned for being more environmentally responsible). Here it is crucial for BSCs and facility managers to research any software being considered to ensure it meets the specific needs and goals of the organization.
Digitalization is the practice of using technology to enhance corporate processes. Today technology to digitalize processes is available for every aspect of cleaning operations. Examples include:
· Work loading software to adjust variables as required
· Internet of Things (IoT) and artificial intelligence (AI) to make data-driven decisions regarding cleaning schedules and frequencies by area
· Smart dispensers to track soap, towel, and other consumable usage (which can help reduce the overall cost of these consumables by 20 percent to 30 percent).
· Software programs to tell cleaning crews when a meeting space has been used and needs cleaning
· Traffic monitors to track the number, time, and flow of people in the facilities
· Many, many, more.
These and similar technologies also help better direct labor to improve overall efficiencies and productivity to produce a higher level of clean.
While digitizing, then digitalizing, can improve the effectiveness, efficiency, consistency, and productivity of cleaning processes, neither should be done without examining the processes themselves. Do the processes move the cleaning operation toward excellence or hinder its progress? Now is the time to review the processes being used and, if necessary, replace them. There is no need to transfer flawed processes from paper to software and even less need to add digital functions.
3. Track KPIs. The third step to using data to improve decision-making and cleaning operation outcomes is to develop a dashboard of the critical key performance indicators (KPIs). Like an airline on autopilot, a best-in-class cleaning operation should be able to operate on quality cruise control. A KPI dashboard ensures the operation doesn’t stray off course. The dashboard must measure, record, track, report AND be regularly monitored. This data will paint a picture of the current situation and trends over time, such as whether the quality is improving or getting worse and at what rate. The information can then be used to make decisions and measure the impact of those decisions on effectiveness, efficiency, productivity, and consistency.
The KPIs developed should depend on the operation’s business objectives and pain points, from staffing and scheduling to quality assurance and safety. A KPI dashboard can verify what is working and where improvement is needed, as well as provide the data necessary for a cleaning operation to verify results and validate its effectiveness for all stakeholders.
These basic steps will ensure the correct data is collected to enhance decision-making and ensure an overall best-in-class cleaning operation, one that is constantly improving its operation and results.
This is part three of a six-part series. Click here to read part one and here to read part two.
Mike Sawchuk of Sawchuk Consulting is a leading education and BSC cleaning operations consultant and coach. He assists BSCs and facility management leaders, helping them improve their outcomes with insightful, pragmatic solutions and comprehensive, integrated assessments for cleaning operations. He can be reached at 905-932-6501 or via LinkedIn at www.linkedin.com/in/mikesawchuk. Or to learn more about his and his company’s expertise, visit www.sawchukconsulting.com.