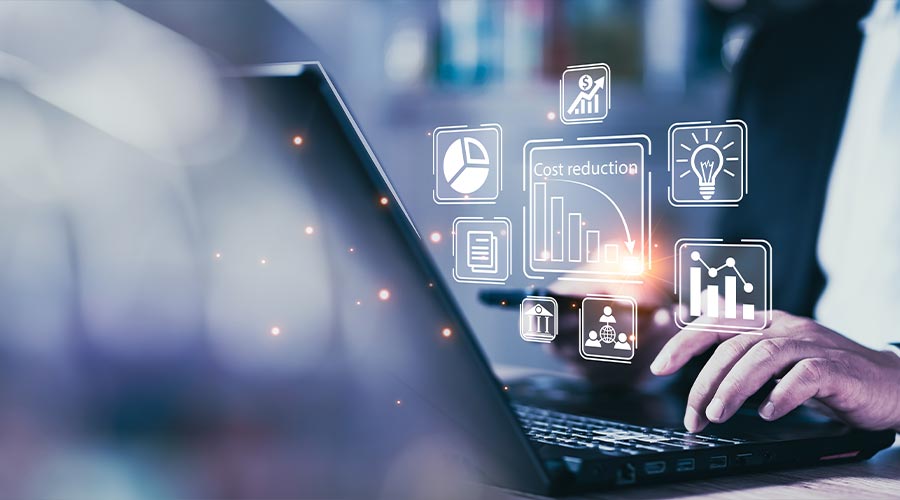
Contributed by Phil Carrizales, I.C.E-T, A.C.T, ACME Paper & Supply Co.
Embracing standardized processes in businesses large and small is no longer just a matter of efficiency, it’s a matter of sustainability and fiscal responsibility. Optimizing business operations is a driver of success in modern facilities management practices and the better owners and managers get at the standardization game, the better the long-term outcomes will be.
The Challenges of Multiple Chemical Products
The building and facility management industry is faced with an overwhelming number of choices when it comes to cleaning products. From floor cleaners to disinfectants, the wide variety can increase the likelihood of inefficiencies in product usage and storage. For this reason, implementing standardization in product selection and procurement and training specific staff on ordering efficiencies is imperative.
Take one very large building services contractor (BSC) our team recently met with in the Maryland and Washington, DC region. Touring the company’s sizable warehouse space, we were struck by the multiple and redundant cleaning products taking up space on the shelves. The facility manager didn’t know what many of these cleaning products did, why they were ordered, when they were ordered, or by whom. This was a perfect example of why standardization and efficiency processes were necessary in the stocking of cleaning solutions. Consolidating supplies not only frees up storage space but purchasing one or two cleaning products that tackle multiple jobs can lead to tremendous cost savings.
Streamlining for Cost Savings
It’s no secret that standardizing chemical products can save businesses money. From bulk purchasing to negotiating more favorable pricing from suppliers, facility managers can reduce the risk of over-ordering and overstocking supplies. Streamlining the usage of specific products also minimizes staff training requirements which saves time and money on education and onboarding processes. Stocking fewer cleaning products means companies can focus more on training staff on the appropriate usage of one or two products instead of many.
Take Advantage of Dilution Control
Thanks to improvements in chemical formulations, one cleaning product can perform multiple jobs well. Whether it’s a multipurpose cleaner, a disinfectant, floor or window cleaner, many chemical solutions, including many green cleaning products, come in concentrated formulas that are easily diluted. This means less packaging taking up less room on storage shelves and one product that can last longer, resulting in cost-efficiency.
The Soft Cost of Doing Business
These days, warehouse and storage space is at a premium, both in space and dollars. There is a cost for every purchase order for every product with multiple deliveries that must be met and cataloged by warehouse staff.
Product standardization can help businesses large and small with:
- Cost efficiency: standardization eliminates redundant products and reduces the risk of waste due to expiration. Procurement practices will also be improved, and price negotiation can reduce expenses.
- Operations: standardization of products and cleaning protocols streamlines staff training and utilization. We’ve seen many facilities enact “floaters” or personnel focused on the assessment of products and processes to ensure operational efficiency.
Where to Begin with Standardization
For many facilities, beginning with a comprehensive survey of every site allows companies like ACME to look at the big picture. We’ve seen facilities with 10 different locations do things 10 different ways with 10 different products. In the case of the large building service contractor, the ACME team looked closely at every site and assessed the type of cleaning they were doing to devise a short list of quality cleaning products that could be run through dilution control and serve each location effectively. Our team created laminated instruction sheets and flip cards so staff knew exactly how and where to use each chemical.
The result? The company used one type of floor cleaner, window cleaner, and the like at each location instead of multiple chemicals. Every product went through dilution control and we standardized all of the cleaning processes and procedures. The cost savings and the efficiency gains were huge, with savings at a minimum of $100,000 a year. This allowed the company to reinvest those savings into new technologies and their people.
The development of standardized processes is effective for every type and size of facility, whether it's healthcare, education, or Class A office buildings. By streamlining products and procedures, businesses large and small can realize substantial cost savings and efficiency gains.
Phil Carrizales is the Director of the Hygiene and Facilities Solutions Division at Acme Paper and Supply Company, one of the nation's largest suppliers of sanitation solutions, disposable food service packaging, restaurant equipment and supply, retail and industrial packaging, and custom-designed packaging. Phil has over 20 years of experience in account management for major cleaning suppliers and is ISSA certified. Phil can be reached directly at pcarrizales@acmepaper.com. For more information visit https://www.acmepaper.com/index.html.