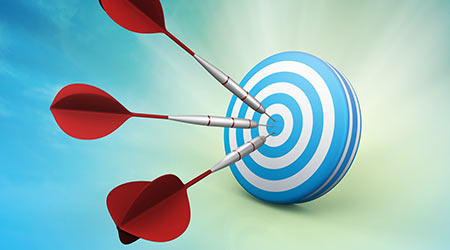
Contributed by Alan France, CS-P, CSR-P, Vice President, Quality and Sustainability, ABM
Even with advances in technology and equipment, cleaning services still rely heavily on man power. Because labor accounts for 55-65% of janitorial costs, creating efficiencies is key to lowering costs.
Learn three ways to improve janitorial productivity and reduce costs while maintaining a clean and healthy facility.
1. Use a “one-pass” cleaning process.
Train your service professional to use a one-pass cleaning approach. This involves simple, logical cleaning processes that leverage proven time-saving techniques, including wiping furniture from the top down and starting to clean a facility at the furthest point from the exit and working your way out.
A one-pass approach, leveraging proven practices and the right equipment, will:
- Improve the positioning of cleaning materials and supplies to reduce frequent returns to the cleaning cart.
- Prevent backtracking when cleaning an area. Trashing, dusting, and vacuuming can occur almost simultaneously.
- Increase the speed at which a cleaning professional can move through an area.
- Improve cleaning motions to increase efficiency while reducing the risk of potential injury (to the cleaning professional).
A one-pass cleaning approach can improve productivity by 5.5 percent. Below are specialized tools to improve the processes associated with common janitorial certain tasks:
· Emptying trash. Cleaning professionals are often required to empty waste baskets and recycling bins into separate trash receptacles. This often involves the janitor making two or more separate rounds through an area. By providing a trainable dolly system, (Rubbermaid is one of many brands that make them), janitors can link trash receptacles together, like train cars, and pull them with one handle, collecting both recyclables and other trash in one cycle, as they go.
· Surface cleaning and dusting with microfiber. Microfiber has had a significant impact on the cleaning industry. The material, which can absorb up to seven times its weight in water, has an almost magnetic attraction to dirt and dust. Microscopic “hooks” in the fabric act as claws that scrape up and hold particles. Microfiber mops, cloths, and telescoping dusting wands quickly capture and lock in dirt rather than just moving it around. By using microfiber materials in your cleaning program you can save time and money. As an additional benefit, extension wands with microfiber head covers provide janitors more extension and eliminate the need to reach and stoop when cleaning high and low areas.
Microfiber is a lint free, durable and soft material, so it does not scratch surfaces. Test results show its use can reduce bacteria levels by more than 96 percent. It is an environmentally-friendly material because it minimizes the use of chemicals and paper towels. In addition, microfiber cloths and mops can be color coded for different areas of a facility to control cross contamination—the spreading of bacteria among people, surfaces, and/or equipment.
· Floor cleaning. Using lightweight, powerful hip and backpack vacuum cleaners improves a cleaning professional’s mobility. Designed for comfort, maneuverability, and ease of use, these vacuums have an airtight canister that reduces the amount of dust in the air and a multi-level filtration system that maximizes their capacity to pick up dust and dirt.
Hard floor cleaning with microfiber flat mops eliminates the use of buckets. In addition, leveraging refillable cleaning solution bottles, secured in a plastic caddy, minimizes trips to the janitorial closet. Microfiber mops have a drag that is 1/10 of traditional wet mops, which reduces worker fatigue, while scrubbing strips take care of scuffmarks.
For small messes that don’t warrant taking the time to set up a vacuum or mop, a mechanical roller sweeper or toy broom with a standing dustpan can be used. These tools work well on hard surfaces and low pile carpet.
2. Consider a 3/2 cleaning approach.
For additional cost savings, implement a 3/2 reduced specification approach. In a 3/2 cleaning approach, full facility cleaning would occur three days per week, typically Monday, Wednesday, and Friday. On these three days, all existing tasks and frequencies continue to be completed in all areas. But, on the two other days—typically Tuesday and Thursday—only “critical” building areas receive their regular service at the same frequency. These critical areas often include lobbies, breakrooms, cafeterias, and restrooms. Non-critical building areas are not cleaned, vacuumed, or trashed these two days.
As a 3/2 plan is implemented, your service provider should work closely with you to identify any problems and make necessary adjustments—ongoing operational evaluation is critical to a successful 3/2 program. For example, some sites might require additional trashing in designated areas. Certain building areas, such as executive offices and suites, may need to have additional tasks added back on the reduced days. For high-end offices or retail facilities, any customer-focused areas might also require special attention. One thing to consider with this approach is that, depending on traffic, it may increase the wear and tear on carpet, which would warrant replacement sooner than anticipated. This is not a reason to discard a 3/2 plan, but it is something to keep in mind as you weigh your options.
If properly implemented, you could expect to see cost savings between 15 and 25 percent almost immediately, depending on your building type, occupancy, staffing plan, etc.
3. Trust the experts.
People often view janitorial services as a commodity, but there is an art and science to cleaning. Your service provider should perform a careful analysis of the facility’s needs and generate a customized cleaning plan. The provider can then equip each cleaning professional with the appropriate combination of tools and equipment, as well as a task schedule optimized for their specific work areas.
By partnering with a trusted services provider, you will benefit from their years of experience and proven best practices, including improved efficiencies; a cleaning team that is happier and more focused; increased cost savings; and overall, better quality cleaning, recycling, and maintenance programs.
Alan France is in his nineteenth year at ABM Industries. Prior to this year, Alan served as the Director of Sustainability, Environmental Services. In this role Alan was responsible for the oversight and the operational deployment of ABM GreenCare® and worked closely with new and existing customers to implement and maintain our sustainable service programs. Alan worked with ABM's suppliers to ensure their newest products and innovations are introduced to the ABM GreenCare program.