How does any industry achieve credibility — with its members, its customers, the media and compared to other industries? When Sanitary Maintenance posed that question to several cleaning industry experts, one issue kept resurfacing in their answers: standardized certification. An industry that has agreed-upon standards takes the guesswork and subjectivity out of evaluating cleaning procedures and product performance. In the sanitary supply industry, many are calling for a universally accepted system of certification.
“Our industry actually does very little in the way of third-party certification,” says David Frank, president of KnowledgeWorx, Highlands Ranch, Colo. Frank recently founded his own third-party organization, the American Institute of Cleaning Sciences (AICS), modeled after a 30-year-old organization in Great Britain, the British Institute of Cleaning Sciences (BICS). Frank created AICS to certify cleaning processes for end users, as well as to establish best practices for manufacturers and distributors.
“Our cleaning industry can learn a lot from what’s going on in Europe,” he adds. “In Germany, you have to have three years of training before you can be a ‘master cleaner.’ In the United States, almost anyone can do it. If people don’t need credentials, then the ethics and professionalism of the industry go down.”
Not that certification has been completely ignored by the sanitary supply industry. There are plenty of organizations — new and old — that offer certification programs. The Institute of Inspection Cleaning and Restoration Certification (IICRC) has been in the business of certification for more than 30 years, while The National Floor Safety Institute (NFSI) was established in 1997. There are a number of certifying organizations in the jan/san industry — from the Green Seal certification program, which certifies that cleaning products are environmentally friendly, to the professional certification system for the Association of Higher Education Facilities (APPA), which endorses cleaning processes for buildings.
Frank, and others, still see a need for universal industry certification criteria in the United States.
“There should definitely be an organization that monitors what goes on in the industry,” says Mark Newhouse, president of Laymen Global, a distributor in Rahway, N.J. “We don’t want everyone claiming, ‘Our product does this,’ or, ‘This is the best method,’ without any credibility behind it. Our company recently lost an account because our competitor was making claims about his product that no one could refute, even though our product was every bit as effective.”
“Certification doesn’t just elevate standards; it creates standards,” says Russ Kendzior, president and founder of NFSI, Southlake, Texas. “The industry has really let anyone make any claim, so the end user has no way to compare.”
Valid standards can’t be established if products and procedures aren’t sanctioned in some way. In order to sanction either a product or a process, there has to be a set of performance criteria. The trickle-down effect of creating standards makes for more demanding job-skill requirements. Consequently, a more skilled work force often enjoys increased credibility and even better pay.
Science vs. Marketing
Many industry experts insist that in order for any set of standards to be credible with the industry at large, they must emanate from an independent, neutral third party that has no direct ties to manufacturers or distributors. At the recent International Sanitary Supply Association (ISSA) trade show in Chicago, a number of certifying organizations came forth with strong ties to the manufacturers they evaluate. Many attendees were skeptical about the degree of objectivity one can attach to this type of approach to certification.
“Unfortunately, I think [most certification] is often a lot of marketing hype,” says Carol Dell’Aquila, president of Maintex Inc., City of Industry, Calif. “Many of the organizations get paid by the manufacturers they evaluate, so it’s no surprise when those manufacturers get certified.”
Although many manufacturers in the jan/san industry have established demanding manufacturing and performance criteria for their products, most industries rely heavily on an unbiased, third-party organization, says Frank. “Some of the alpha-level manufacturers have done their homework and have some pretty good programs, so I’m not making a sweeping indictment against them,” he says. “But you can’t have the fox in the henhouse. You can’t have a quality insurance program that is being measured by the manufacturers. At the end of the day, the manufacturers have to be loyal to their invoice, so the evaluator has to be a neutral third party.”
The problem isn’t necessarily that manufacturers aren’t discerning evaluators. However, they often don’t share the criteria used to measure their products. This problem is more visible with products that are labeled “green” or “environmentally friendly,” but the claims don’t go much further than the label. “I give that kind of certification absolutely no credence,” says Scot Case, director of procurement strategies for The Center for a New American Dream, Washington, a third-party organization that evaluates the safety of cleaning products. “It must be open and transparent criteria, or the claims really don’t mean anything,” he says.
As one of the industry’s most influential organizations, ISSA has been petitioned by some cleaning professionals to institute credible guidelines for the industry. “I believe that eventually ISSA will set up certification in the area of cleaning methods,” says Frank. “In the long run, I think it’s their responsibility to provide educational modules that will help the industry create centralized standards.”
ISSA says it has considered establishing itself as a comprehensive cleaning certification entity, but has yet to set a course for the kind of curriculum that would be appropriate. “From a broad perspective, it would be interesting to have a uniform standard for the industry,” says Anthony Trombetta, ISSA’s director of education. “Everyone could participate in and abide by those standards. We have looked at it, and we are continuing to look at it, but there are several inherent problems in trying to organize certification for a diverse industry,” he says. “It would definitely be an upgrade in professionalism.”
ISSA is in the final stages of endorsing NFSI’s standards for floor safety certification as its own standard, says Kendzior. “The ISSA had heard that we were making a CD-ROM of our training program, which will certify [cleaning professionals] in the area of slip-and-fall accidents,” he says. “We’re putting together the program, and it will be administered by ISSA and State Farm Insurance. Once they’re certified, participants will have finished a course that will help them reduce slip-and-fall accidents by 80 percent.”
Kendzior says certification must be rooted in science. “Our claim to fame at the NFSI is creating the first practical, real-world test method for measuring the safety of floor materials,” he says. “It’s a scientific testing instrument that’s been accepted by ASTM’s (American Society for Testing and Materials) federal standards committee.”
The Importance of Profits
While some of the standard-setting organizations swear by their non-profit status, others claim that there’s nothing about being for-profit that puts credibility in question. The IICRC has been on both sides of the profit fence throughout its 30-year history.
“The IICRC as we know it today is totally different than when it started,” says Jeff Bishop, a consultant with the IICRC. “It started out as a for-profit organization, and it was really just a marketing scheme. People would pay about $30 per year, and we’d tell them that they could put our seal of approval in their advertisements in the Yellow Pages.”
In the early 1980s, IICRC was bought out by several associations. Today, the IICRC is a federally approved, non-profit organization owned by 16 trade associations. “I feel that it’s very important for the organization to be a non-profit entity if it’s going to be certifying companies without any bias,” says Bishop. “Otherwise, there will always be the possibility of a built-in prejudice.”
Not all certification organizations agree with Bishop’s take on how to eliminate potential bias. According to Frank, the issue is not whether the organization receives payment, but from whom the payment comes. “I don’t think it really matters whether the organization is non-profit or for-profit,” says Frank. “The question is who is paying for the services? I’m not doing it for free, and I don’t have to. People are willing to have a third-party organization come in and assess the cleaning programs. They know it’s a valuable resource.”
Even if an association or institute happens to be recognized as a non-profit organization, users usually still pay for the services that are provided. Some analysts have criticized the NFSI for charging manufacturers $2,800 in fees to certify a manufacturer’s floor machine. What those critics don’t understand, says Kendzior, is that most floor machines fail the first phase of inspection, which costs only $300. In addition, NFSI’s certification lasts for the life of the floor machine, unlike many organizations that require companies to renew their certification annually.
“Underwriters Laboratories is a very respected certification program, and they charge thousands of dollars per product per year in order to be certified,” says Kendzior. “We have a similar style of testing that is quite difficult to pass. It’s not like they send us $2,800 and we just send them a logo. It’s a 30-day test, and only one out of three applicants earn their certification.”
ISSA, as a non-profit organization, is said by some to be the highest-ranking candidate to be an umbrella group to handle industry certification.
Products vs. Process
Only a few certifying organizations, such as Green Seal and NFSI, specialize in evaluating products. Most organizations in existence today evaluate cleaning processes, including AICS, IICRC, and APPA. Important to any discussion about jan/san certification is the question: should the two spheres of cleaning industry accreditation be independent or are they viscerally intertwined?
Those organizations that focus on the product side of cleaning say that the “what” of cleaning should take priority over the “how” of cleaning. “It’s my experience that those groups that emphasize process do so because they don’t have quality products that meet the right criteria,” says Case. “By focusing on the process, it helps [manufacturers] hide their faulty products. Start with products, then work on fixing the process.”
On the other hand, say process-certification advocates, a quality product doesn’t do any good if it’s not being used correctly. “It doesn’t matter to me that a product is certified by Green Seal because that doesn’t mean that the process is being carried out correctly. Just because a product doesn’t have any carcinogens, doesn’t mean it’s OK to use all over a building,” says Frank. “Now, if Green Seal certifies action points, and they’re checking the measurements and they know how the HVAC and air-exchange rates are being affected, then they can tell you if it’s safe.”
For the time being, product and process certifications are likely to operate independently of one another. However, multiple certification groups appear to be better for the industry than no certification at all — as long as each group is fairly and accurately evaluating product or process.
“There are different levels of certification,” says Frank. “I can certify a test, a product or a process. There are moving parts, and you have to try to look at the big picture in order to see that each part has its own importance.”
Whether or not an organization is certifying products or processes, all good certification programs demand at least one thing: time. Most often, the pretenders can be separated from the contenders by looking at the amount of time spent on each certification standard, says Bishop. “Here at the IICRC, our organization came off looking like latecomers on the mold-remediation issue. We had meetings with insurance companies, our cleaning technicians and four of our lawyers for 18 months, so that we could really make sure we did it the right way. We didn’t want to just throw something out there, and see if it would stick. In the meantime, several groups have come out with standards that are popular, but they’re really inadequate.”
All Or Nothing?
“I really believe that there needs to be a universal certification standard,” says Shelley Riha, regional president of AmSan, a large jan/san distributor. “Without those standards, the industry becomes overly fragmented and confusing — and it’s already that way to some extent. The quicker we can arrive at one standard bearer, the quicker we’ll be able to level the playing field for all parts of the supply chain.”
Other industries were slow to agree on certification standards, but when they did, it created a common language that elevated the practices of those industries, says Riha, who has a background in the electronics industry. “If you look at UPC barcoding, there were so many standards in the beginning and it created a tremendous amount of confusion,” she says. “Finally, one standard was agreed on, and the confusion ended. If you don’t have an organization that’s controlling that, then you’ll just have all sorts of claims.”
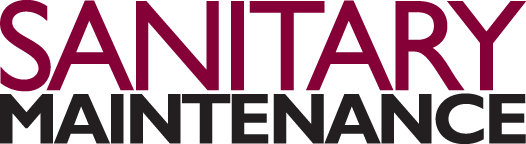
Certified Confusion
BY Alex Runner
POSTED ON: 1/1/2004