Through the first quarter of the year, the U.S. tissue market yielded rather mixed signals. While some tissue producers reported higher volumes, slightly improved product pricing, or brighter prospects in the year ahead, most manufacturers blamed persistently competitive markets for the quarter’s somewhat disappointing profits. Likewise, first-quarter demand was a bit of a mixed bag. Year-over-year U.S. tissue demand was looking strong in January and February, but the latter month had an extra day this year. And because March demand was slightly negative, 1Q04 tissue consumption turned out to be comparable to 1Q03.
The story changes somewhat if we separate the away-from-home (AfH) market from retail tissue. While retail tissue seems to have been relatively weak thus far this year, AfH demand during the first quarter was exceptionally strong (4.4 percent over year-ago). All things being equal, the extra orders for AfH tissue helped secure the spring price hike, now being implemented by the mills. What is not yet known, however, is the extent to which the building of buyer inventory impacted the first-quarter demand jump. AfH customers may have shrewdly padded their stocks of paper in advance of rising prices.
Whatever the case, the increase in AfH prices is slowly gaining acceptance. By June, average pricing will have climbed nearly 3 percent over February, and prices should continue to climb as contract prices are renewed at the higher levels. On the other hand, tissue manufacturers could face stiff resistance to further implementation of the general price increase if buyers are able to cut orders and instead rely on the substantial amount of (tissue) paper purchased for inventory during the first quarter.
One should also note that although international trade in tissue plays but a small role in the market, U.S. tissue imports have been running high while exports generally have been flat. U.S. imports of parent rolls and converted toilet tissue from Canada hit all-time highs in March — buoyed principally by the expansion of Kruger, Irving, and Cascades that was aided by the depreciation of the Canadian dollar since January. The threat of competitively priced imports could prevent the spring price increase from being fully successful.
Nevertheless, these challenges to rising tissue prices are relatively minor when viewed in light of our forecast of rising operating rates and production costs. Although U.S. apparent consumption of tissue in 1Q04 fell a shade below year-ago, on a quarterly basis, total demand in 1Q04 showed significant improvement over the second half of last year. These quarter-to-quarter gains in demand will continue through 2005, but at a diminishing rate due to the decelerating economy. Still, we can expect to see rather strong year-over-year demand numbers through the balance of 2004, owing to softer comparisons to the weak demand during the last half of 2003.
Showing Some Restraint
The solid improvement in U.S. tissue consumption over the next couple of years will likely be on par with the long-term average annual growth rate (2.1 percent) and push demand over 7.5 million (short) tons next year. But as the economy cools down toward the trough of the business cycle, demand growth will likely slow down to slightly below trend.
The saving grace for tissue mills will be if they exhibit supply restraint as we expect they will for at least the next two years. Three new machines started up during the first few months of 2004: Potlatch at Las Vegas (30,000 tpy), G-P at Wauna, Ore. (80,000 tpy), and SCA at Barton, Ala. (110,000 tpy). However, moves to idle or permanently shut down several machines over the last few quarters helped to accommodate the new tonnage. Additional capacity gains diminish in the near-term outlook. Aside from the inauguration of a third Metso PM (80,000 tpy) at P&G’s Cape Girardeau, Mo., mill late this year, and the launch of a 70,000-tpy machine at First Quality’s facility at Lock Haven, Pa., we expect to see only one or two other, smaller expansions by the end of 2005. (These may include Augusta Tissue and Evergreen.)
With capacity gains limited to just over 1 percent per year in the near term, the trend-level growth in demand will spur tissue industry operating rates upward. The long-term average operating rate for U.S. tissue is 93 percent. But during 2001-2003, aggressive capacity expansion met with relatively weak demand growth to drag the utilization rate below that level. In the past few quarters, it reached a nadir of 88 percent — the lowest level in a generation. Now that demand appears to be growing faster than supply, tissue operating rates will likely climb steadily toward 91 percent by the end of next year.
While marginally tighter markets could help producers secure a price increase this year, the real boost will come from intense fiber cost inflation. Recovered fiber, or deinked pulp, accounts for 43 percent of the furnish at tissue mills across the United States. Thus, the volatile price of recovered paper has a tremendous impact on industry profits. Average prices for a key grade of recovered paper used in tissue manufacture, SOP37, increased nearly 7 percent in 2003 and finished the year at $95/ton. Prices surged in early 2004 and by February hit $115/ton. A lull in the market this spring prevented runaway inflation, but as global paper and board production ramps up during the next few quarters, we could see SOP37 climb to $190/ton in early 2005.
Rising pulp costs similarly put the squeeze on nonintegrated mills that use virgin market pulp in the furnish. NBHK delivered to the United States cruised from $455/tonne in January 2003 to $505/tonne in January 2004. In June, the price of NBHK is expected to reach $580/tonne and could continue to climb until next spring, approaching $700/tonne. Inflation in softwood pulp has been (and will be) even more dramatic. We foresee NBSK climbing from $480/tonne in January 2003 to $780/tonne by April 2005.
Increase Reasoning
Due to mounting pressure caused by fiber and energy costs, we estimate that U.S. tissue mill production costs will build on a 9 percent jump in 2003 and inflate by another 8 percent in 2004. This cost pressure has already catalyzed all of the major U.S. tissue manufacturers to announce price increases, and it will force them to push hard for full acceptance.
SCA North America was quick to announce a general increase effective March 11 of up to 9 percent for into-stock items for its away-from-home products. Georgia-Pacific, Cascades, and BayWest chimed in with similar plans, albeit slightly less aggressive. In the retail (consumer) tissue markets, Procter & Gamble (P&G) announced plans to increase its prices on facial and bath tissue products by 5 to 6 percent, but will wait until the summer to do so. Kimberly-Clark soon followed with a similar proposal to lift tissue pricing in July by an average of 5 to 6 percent. And Georgia-Pacific plans to do the same, although its target range of increase is 6 to 9 percent.
The recent (or perhaps ongoing) industry shift in favor of discounts and promotions decreases the likelihood that tissue producers will be able to shift the full burden of the anticipated cost inflation to its customers even if a second round of price increases is proposed. Although they face shareholder pressure on a quarterly basis, the major manufacturers remain keen to protect market share. We believe, however, that the announced price hikes will yield a net pricing gain of around 3 percent in 2004. Furthermore, given the mid-year start to most of the increases this year, average pricing in 2005 could jump another 3.5 percent despite minimal cost inflation.
Nevertheless, because price gains lag rising costs, producer profits will be squeezed in 2004. Consequently, delivering shareholder value will continue to be a challenge for tissue manufacturers for the next several quarters. And even as fiber costs cycle downward over the next couple of years — thereby boosting tissuemakers’ profitability — the decelerating economy will rein in demand growth and re-ignite competition for space on the grocery shelf. The U.S. tissue industry will probably remain highly competitive for quite some time to come.
U.S. Tissue Market Supply and Demand (000 Short Tons)
2000 2001 2002 2003 2004 2005 Demand
%CH6,954
-0.77,084
1.97,220
1.97,233
0.27,378
2.07,541
2.2 Imports 355 416 516 541 538 516 Exports 313 357 401 402 401 412 Production
%CH 6,911
1.07,024
1.67,106
1.27,094
-0.27,241
2.17,436
2.7 Capacity
%CH 7,448
4.67,736
3.97,785
0.68,015
3.08,113
1.28,210
1.2 Capacity
Utilization 0.928 0.908 0.913 0.885 0.906 0.893 Demand = Production + Imports - Exports
Andrew Battista is Senior Economist at RISI/Paperloop out of Charlottesville, Va., where he edits the monthly publication, The Tissue Monitor. Contact him for additional analysis (historical & forecast) at 434-978-2927.
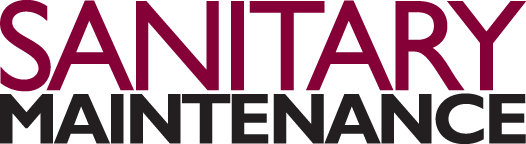
Get Ready For Paper Price Hikes
BY Andrew Battista
POSTED ON: 7/1/2004