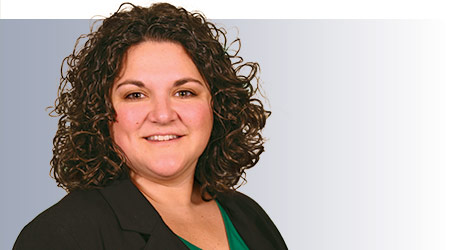
I’m one of those people who likes to be organized. I like knowing what I have and where I have it so I can easily and quickly access it — or restock it — in a time of need. That’s why I got excited last weekend when I secured three new shelving units and got to spend the afternoon in the basement reorganizing.
It may not sound like a fun way to spend the weekend, but, for me, it’s a way to give order to the chaos. Now, surplus cleaning supplies are in one area, bulk foods occupy their own full unit and kitchen appliances are strategically placed for easy access.
When was the last time you did a similar exercise by walking through your warehouse? It might look organized, but there might also be some chaos that needs attention. For example, many distributors store all their chemicals in one area, paper in another and equipment accessories somewhere else. When it comes to order fulfillment, categorizing products this way can be a time suck as staff has to walk past seldom-purchased items to get to more popular products.
It might be time you consider shelving strategies that make more sense and contribute to worker productivity. Start by dividing inventory into three categories: A, B, and C. Products in group A are top sellers. These should be stocked together, most accessible and closest to the loading docks. Category B inventory tends to be less profitable, but still moves through the warehouse at a steady pace. Workers should have relatively easy access for picking.
Finally, products in category C sell less frequently than the others and tend to cost distributors the most because of low product turnover. These should be placed out of the way in the warehouse, or possibly on higher shelves. Once products become excess inventory or dead stock, it’s recommended to remove them entirely, freeing up the warehouse space for more profitable products.
These are simple ways to organize warehouses so teams can be more efficient at filling orders. Distributors who want to take it one step further should consider what technology can offer. Our cover story outlines how adding technology to the warehouse can help respond to staffing shortages, manage inventory or even publicize delivery times to customers. Meanwhile, I need to add napkins to my shopping list.
Corinne Zudonyi is the Editor-in-Chief of Sanitary Maintenance and has been in the cleaning industry for 17 years. She also oversees CleanLink.com, Facility Cleaning Decisions magazine and Contracting Profits magazine.