“Achieving Effective Inventory Management, 5th ed.” is written by Jon Schreibfeder, president of Effective Inventory Management. The book is designed to help distributors meet or exceed customers’ expectations of product availability and to minimize total inventory investment. The following is excerpted from chapter two, Get Your (Ware) House in Order.
Bar codes can be utilized to help ensure that products are put away in the right bin location and orders are filled properly. One-dimensional bar codes are used to identify individual products or bin locations.
You might think that it would be impossible to put a bar code label on every piece of every item you stock. You don’t have to. Many companies have utilized the power of bar codes by placing product bar code labels on bin locations instead of individual pieces of a product.
There are two types of bar code readers: data collection devices and “RF” (or radio frequency) units. Data collection devices store information about the specific products and quantities of those products scanned over a specific period of time. This information is then downloaded in a batch into the computer system. Data-collection devices are most appropriate for receiving and the physical counting of inventory.
“RF” bar code units maintain constant contact with the computer system. As soon as a product is scanned or a quantity is inputted, the information is transmitted to the computer system and appropriate inventory-related records are updated. “RF” bar code units are appropriate for nearly any warehouse operation. Here are some common applications found in most warehouse management systems (WMS):
• Receiving: The receiving person scans a “two-dimensional” bar code on the label of an incoming package.
A two-dimensional bar code contains all of the information in a document (in this case a packing list). Most systems give the receiver the option to automatically receive the shipment or check the shipment for accuracy.
If the shipment is automatically received, on-hand quantities of each item listed on the packing list are increased by the quantity received and the material is “placed” in a holding bin for stock receipts; perhaps a holding bin for material that will be sent to a specific zone in the warehouse. The receiver is notified of any discrepancies between the material listed on the packing list and the actual purchase order. In other words, any difference between what you ordered and what you received.
If the shipment is checked for accuracy, (whether using one or two-dimensional bar codes) the receiver will scan the one dimensional bar code on each piece, box or package in the shipment. The system will keep a running total of what is scanned and compare it to both what is listed on the packing list and what was ordered. The receiver will be notified of any discrepancies.
• Put Away: When a warehouse person puts away a received product in a fixed or random storage bin, he scans the receiving copy of the purchase order or the individual item and the bin location. The system verifies that he’s putting the product in the right location and immediately increases the on-hand quantity of the item in that bin location, and at the same times decreases the quantity of that product in the holding bin used in the receiving process.
• Order Fulfillment: When filling an order, the picker can scan the bar code label on the bin and the system will verify that she is pulling the right item from the right location. The picker can enter the quantity picked or scan each piece. RF units immediately deduct the picked quantity from the bin’s on-hand balance. At the same time the quantity of the item in an order accumulation bin assigned to the picker will be increased. The quantity will remain in this bin until the order is packed and shipped.
Note that bar code technology eliminates hard-to-account-for “floating” material in a warehouse. Floating material occurs in facilities that only use paper-based documents. There is always a time lapse between the movement of material and when transactions recording that movement are entered into the computer system. With RF bar coding it is easy to pinpoint where any quantity of any item is located at any time.
• Physical Counting: The counter scans the bar code label on the bin and enters the quantity of the product he counts. If there is a discrepancy between what is counted and the quantity in the computer system the bar code reader may prompt the counter to recount the product.
To order a copy of “Achieving Effective Inventory Management,” visit www.naw.org.
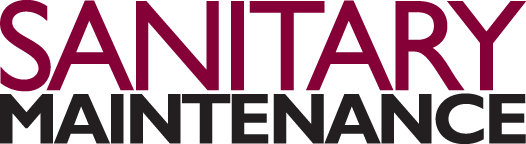
Bar Coding Systems Improve Warehouse Accuracy and Productivity
BY Jon Schreibfeder
POSTED ON: 9/17/2012