The advertising slogan “You’ve come a long way, baby!” could very well be applied to today’s extractors, sweepers and vacuums — the products that fall into the carpet-care equipment category. Equipment has, indeed, come a long way over the years, according to distributors across the country.
In his 10 years in the jan/san industry, Kevin Beam, vice president of sales for Treat’s Solutions in Ada, Okla., has seen vast improvements in floor machines over the ones he originally sold.
“Ten years ago, equipment was inadequate compared to today,” he says. “Machines were more labor intensive, had less capacity and no batteries. Now we’ve got battery-powered machines, we’ve got walk-behinds and ride-ons. We’ve got machines that can now clean 38,000 square feet of carpets per hour. But today’s operators must know how to properly do the job.”
Beam says the No. 1 piece of carpet-care equipment his company sells today is the battery-operated ride-on extractor.
“It’s the most phenomenal machine I’ve ever seen,” he says. “It does a faster, more efficient job, with less labor.”
Portable equipment, too, has more features than ever before, says Steve Hanson, a 20-year industry veteran and owner of Brainerd Lakes Cleaning and Supply in Brainerd, Minn.
“In the past few years, you have been able to purchase a unit that has 500 to 1,200 psi, a two- or three-stage vacuum motor, an 800-watt heater, and an automatic pump-out system — that’s equipment with the power of a truckmount and the convenience of a portable,” he says.
Today’s [portable extractors] are mobile and generally self-contained with a fresh water recovery tank and a vacuum motor, Hanson explains.
“They have vacuum motors now that enable you to get good recovery. You’re able to put up to 100 feet of hose on them so you can cover a lot of space, especially if you were to set up your automatic pump-out system. Just let it sit in one location and you can virtually do thousands of square feet without dumping or filling. That’s a fairly recent innovation.”
The industry has seen marked improvements in portable equipment over the past 23 years, says Hanson, including “much better components and better capabilities concerning heat and recovery.” There’s also much less downtime due to repairs, he adds.
“In the 1980s, you typically had equipment with 100 to 200 psi, which was great for its purpose, but was time consuming,” he says. “You couldn’t do as good a job as you can today. There were no heaters on these units, either.”
Keep It Dry
The most important innovation over the past 20 years, according to Hanson, is the backpack vacuum cleaner.
“About 80 percent of carpet soil is dry, so it can be easily removed,” he says. Better filtration systems contribute to much better indoor air quality, he adds.
Backpack technology also works well with the low-moisture cleaning systems that are being used more and more often.
Hanson says low-moisture encapsulation systems are a significant part of the cleaning industry today.
“[These] account for cleaning rates of 2,000 to 3,000 square feet per hour with no rinsing needed.” Once the carpet dries, the “encapsulated” dirt can be vacuumed away. “The labor savings is great,” he adds.
Hanson says the development of the low-moisture walk-behind unit is another important addition to daily maintenance programs. “Their recovery systems recycle cleaning solutions,” he notes.
Ray Herzog, a 20-year veteran of the industry, agrees that low-moisture cleaning systems are important innovations.
“Custodial staffs today are more involved with low-moisture and cylindrical-type cleaning,” he says. Herzog, equipment specialist for Burke Supply Co., Brooklyn, N.Y., says cylindrical cleaners are relatively new in their use of low moisture. He says that in the past, pile lifters had been used on carpets as a dry carpet-cleaning process.
“People are now cleaning in a similar fashion, but with low moisture,” he explains. “That’s been the most important innovation that I’ve seen. By using low moisture, the cleaning process is enhanced. Low moisture doesn’t allow dirt to go deeper into the carpet and the matting, so you basically are cleaning the surface fibers.”
Modern-Day Conveniences
When Mike Tighe started his carpet-cleaning industry career some 18 years ago, two cleaning methods were used. The first method involved rotary machines with box extractors. Tighe, vice president of Industrial Cleaning Products and Supply in West Boylston, Mass., says the rotary would be used first, then the carpet would be vacuumed with the box extractor.
“Later, the industry went more with the box extractor alone, using a wand with 50 or 100 psi to clean and vacuum the carpet,” he says.
“Both methods were extremely labor intensive,” he says. “But in the past 10 years or so, there’s been a shift toward the self-contained extractor that has a brush and vacuum shoe all in one machine. This gives a tremendous increase in productivity.”
In the past three years, however, Tighe has seen a shift back to using the old box extractor.
“But today’s machines have a much higher psi — 300 — and a heating element that heats the water to 212 degrees,” Tighe notes. “A lot of people are using that with the wand. By making the psi so much higher, manufacturers have created a labor-savings method. And the heat factor gives you a deep cleaning.”
Another innovation he cites is the dual vacuum motors on newer units, which allow users to pull more of the cleaning solution out of the carpet, leading to quicker dry times.
“That’s crucial because we’re seeing a demand for less and less downtime in the industry, especially in the hospitality trade or healthcare institutions,” says Tighe. “The quicker the dry time, the better. The dual vac motors provide much more water lift than in the old days. Instead of 10 to 24 hours of drying time, carpets cleaned with this unit can dry in about one hour.”
More and Better Options
Herzog believes that low-moisture systems lead to savings in labor and productivity costs. In the past, people performed a two-step cleaning process using rotary machines and extraction equipment.
“Using low-moisture equipment basically gives you a one-step process,” he says.
“Two rotating brushes, spinning in opposite directions, kick moisture and dirt into a hopper, basically eliminating a step in the two-step cleaning cycle, and therefore make for more productivity and labor savings as well.”
In Bay City, Mich., Michael Arnold, president of Arnold Sales Complete Janitor Supplies Inc., says there are two big changes he’s seen in carpet-cleaning equipment in the past 29 years. “There’s now a wider variety of carpet-cleaning equipment choices available to us, and greatly improved technology.
“The biggest innovations I’ve seen include riders that have come along recently,” Arnold adds. “They’re great for productivity and ease of use in their proper applications. I’ve also seen equipment get larger, giving you a longer time between stopping and refilling. Also, dual-mode extractors that enable you to do light cleaning or heavier cleaning with the same machine — they just require a change of brushes.”
Besides the technology that has helped to improve today’s carpet-care equipment, productivity has improved markedly. According to Beam, an emphasis on training and education “has put us on the road to that improvement in productivity.”
In spite of that, he says, inadequate training is still a big problem in the carpet-care industry.
“In general, end users haven’t been as well informed by sales reps as they should be,” Beam says. “When reps sell the machines, they don’t train the customer well enough. With proper training on the improved equipment, productivity improves. And reps must properly assess their customers’ needs and recommend the appropriate equipment.”
Arnold remembers the first walk-behind carpet extractors back in the early 1980s. “They haven’t changed a whole lot since then, except for this important fact: They have become more efficient, productive and reliable.”
Back and Forth
Tighe says one of the machines his company sells is a two-way, self-contained unit that operates in both forward and reverse modes. There are only a few of these models on the market today, he says.
“Most self-contained units are pulled toward the operator, thereby causing a lot of strain and fatigue,” Tighe notes. “But the two-way machine allows for increased productivity because it’s almost self-propelled in a forward or reverse direction and lets you walk at a normal pace to clean a carpet.”
When Beam joined the industry in 1996, carpet machines weren’t ergonomic, he says. “Pulling a piece of equipment toward you with 50 to 200 pounds of water and components, or holding a wand and a jet and a hose, spraying water and bending from the knees down is hard on the body,” he says. “Compare that to sitting on a rider and doing just as much if not more work.”
Ergonomic characteristics of a product should be considered for the mind as well as the body, Beam contends. “You get a healthier mindset when you can clean four classrooms in a school in 20 minutes vs. cleaning them over eight hours.”
“Cylindrical-type cleaning machines are an ergonomic plus,” says Herzog. “Two counter-rotating brushes oppose each other and just ‘float’ on the carpet. So there’s no pressure needed from the operator, who doesn’t have to use his or her back or shoulders as much.”
Equipment improvements are a constant in the jan/san industry, and distributors will continue to ask, “What will they think of next?”
Jordan Fox is a Milwaukee-based freelance writer.
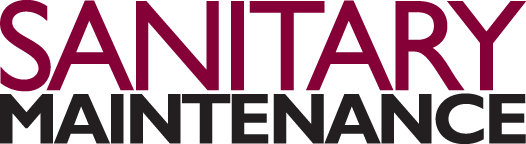
Carpet-Cleaning Equipment’s Quiet Evolution
BY Jordan Fox
POSTED ON: 11/1/2005