Not so long ago, people would have laughed at what are now commonplace items in office settings everywhere — ergonomically designed supplies. They would have viewed ergonomic chairs as contorted, alien-like, with their arms sprawled every which way. Back rests, wrist rests, foot rests and adjustable keyboard trays probably would have been seen as a bunch of useless clutter.
That line of thinking has undoubtedly changed. Sparked by a rash of ergonomic-related complaints, injuries and lawsuits, combined with employers’ increasing awareness of their employees’ comfort, safety and well-being, ergonomically designed supplies have popped up everywhere and are readily and gratefully used by the masses — in the office, that is.
So why haven’t ergonomic tools and supplies become mainstream — or at the very least, trickled down — into the cleaning industry? Their purpose is quite the same as it is in other industries — helping people do their jobs more easily, more efficiently, and with as little effort as possible. We’d all win if this was the norm, right?
“These things are new and you kind of have to work at it until it becomes easy,” says Karen Adams, president of the Mop Bucket in Kansas City, Mo. Adams says the few people who have chosen mops with ergonomic handles haven’t really liked them, but she attributes that more to a tendency to stick with the tried-and-true than actual lackluster performance of the mop handles. End users and purchasing agents seem to have an aversion to the “funny” looking, twisted handles, and more so to the term “ergonomic.”
For a long time, “ergonomics” has been considered a taboo word for many distributors who often associate it with the Clinton administration’s much-opposed ergonomics standard. However, the standard was a rule that would have forced business to comply; the true definition of ergonomics is simply giving a worker the right tools and supplies to allow them to do the most efficient, best job in the easiest manner possible. The study of ergonomics is really based on accident and injury prevention which allows employers to maintain the happiness and well-being of employees.
“Ergonomics is basically the attempt to fit tools to workers and the way they work rather than fit the workers to the tools,” says John Walker, president of ManageMen in Salt Lake City and a leading consultant to the cleaning industry. There are a lot of tools out there that aren’t very user-friendly, he contends. Walker and his company have been pushing for awareness of ergonomics for the past three or four years, and he says he’s seen companies experience success when they have taken the initiative in making their employees’ jobs easier.
For one of Walker’s clients, an airplane building firm, he fitted them with ergonomic vacuums and tools including lighter flat mops for restrooms, and they were supplied with lighter cases of chemicals and cleaners.
“Two of them wanted to continue with the program because they said it was the first time they didn’t go home in pain every night,” Walker says. It’s very sad that workers do jobs that cause them actual physical pain, he adds.
“Our belief is that work doesn’t need to be a pain,” says Josh Kerst, a certified ergonomist and the vice president of Humantech, an Ann Arbor, Mich.-based ergonomic solution consulting firm. He says the act of cleaning presents a whole set of ergonomic risk factors, including awkward postures and positions that are sustained for great lengths of time. Rinsing out mops, carrying mop buckets, washing and wiping down floors and walls with mops, lifting and emptying the bucket — all this causes strain on the back and neck, the wrists and shoulders. Anything that can be done to ease the duration, pressure and extent of these positions will allow cleaners to be more comfortable and therefore, happier in their job.
The best way to carry a bucket is don’t, Kerst muses, though he says finding a way to do a job that is kindest to the body is probably a more realistic solution. Kerst’s company has helped develop a few products with ergonomics in mind, including a machine that makes floor cleaning easier by requiring little force and little pressure.
“You’d be surprised by how many people still clean floors on their hands and knees,” he adds.
Where Trends Begin
It’s fairly well-known that many U.S. cleaning trends have their roots in European mainstream. European culture simply places more emphasis on the act of cleaning, so Kerst says he won’t be surprised when ergonomic products start popping up more and more in manufacturers’ product lines. It’s already happening in Europe, but because customers aren’t demanding the products yet here, they’re not getting a lot of press. Still, consultants and experts are excited about some of the new products that are hitting the market.
For instance, Unger Enterprises Inc., Bridgeport, Conn., recently developed a new line of products that includes an ergonomic, micro-fiber mop, micro-fiber cloths, ergonomic dust pans, squeegees, brushes and more. The line’s official launch is scheduled for ISSA 2001, but the products are already being test-marketed on the East Coast, with positive results.
Unger’s vice president of global marketing, Bruno Niklaus, says these tools are designed to make cleaning a cinch for those using them.
“It’s easier, which also means they’ll get less tired and actually get better results,” he says.
“It’s time for a new system to clean restrooms faster, and in a more ergonomic and better way,” he adds.
Other companies have also come out with some products that are designed to reduce the stress and strain on cleaners, and most do the job. The adoption rate, however, is slower than manufacturers would like. Most of the distributors SM spoke with said their customers had really shown no interest in ergonomic cleaning tools, and they hadn’t sold many, if any.
It’s important to note, though, that an ergonomic tool does not have to be labeled as such to produce the results that define it. As long as it is allowing someone to do their job more easily, it can be classifed as ergonomic.
On the Horizon
Adams is quite optimistic about the products and what the companies are putting on the market now. The floor machines that now come with curved, triangular handles are a favorite — they allow users to change their grip on the bar to a number of positions. Adams also raves about micro-fiber cloths, which she calls “the most wonderful thing since sliced bread.”
Other developments Kerst has seen are the secondary handles that were first added on rakes and now are seen on mops and other handled equipment. It allows users to grip them more easily and comfortably, without putting the wrists in an uncomfortable position.
Flat mops made of micro-fiber are popular in Europe and Canada right now and are lightening the loads of cleaning workers, says Walker, who claims mopping is the most energy-intensive and fatiguing job in cleaning a restroom. Walker also recommends using a proper janitor cart and not loading it down too much, though he says having storage near the restroom is probably the most effective way to combat problems with overloaded and potentially dangerous carts.
Kerst suggests cleaners work to find ways to combine jobs, tasks and motions to avoid unnecessary fatigue.
“Make sure whatever action you’re doing adds value,” he adds.
Other products include taller, thinner mop buckets that Adams says are easier to move and dump, but she says, people are still creatures of habit and it’s going to take some time for these products to really catch on.
“The more discussion, the more people will have a tendency to want to learn about ergonomics for their own good,” she says. But the purchasing managers and decision makers are the ones who hold the purse strings and the decision to move to ergonomic equipment falls on their shoulders.
Helping Hand
In order to be most helpful to customers, distributors need to understand janitorial work to really appreciate the value ergonomic thinking brings, says Walker.
“It’s hard work and I think of lot of them don’t understand that. The cleaners come in and work hard. They’re lifting, pushing and carrying things. Trash bags are heavy and lifting is hard work. The machines are heavy. [Distributors] need to understand that it’s hard work and try to provide customers with tools that make the work easier.”
“What distributors should be looking for are suppliers that have an open mind and are looking for unconventional solutions to conventional problems,” says Lowell Spence, president of Interlochen Consultants Ltd., Grawn, Mich., and a certified safety professional. Then, he says, distributors should be helping their customers find equipment that can be used efficiently and effectively.
“They really need to get feedback from the users to find out how well it works,” he recommends.
Detective Work
Distributors can do many things to bring themselves up to par regarding their customers’ needs and provide them with the advice, education and products that will help them do their jobs in the safest, easiest way. As the industry slowly realizes the value of its employees, it will become easier to anticipate their needs and work to incorporate their advice.
Walker says the cleaning industry is one of the last to realize the value of its employees, but now that the industry is coming around, you’re sure to see employers doing more things to make their jobs easier and less strenuous.
“A lot of industries realized a long time ago they didn’t want to wear out their employees,” Walker says. “Once there’s a dollar cost attributed to an employee, the employee is considered worthy and they start treating them differently.”
That value is also compounded with a lesser turnover rate — employees are happier and more content in their job and duties, and they stay longer.
“It’s all about efficiency and feeling good about what you’re doing,” Adams says. “When you have the right equipment you feel better about your job.”
Despite the enthusiasm consultants show for these products, it’s all in vain if end users aren’t receptive to them. It becomes a matter of educating end users, showing them the value of these products and helping them understand the value they can gain by using them. How long will it take for end users to warm up to ergonomic cleaning tools and equipment? Hard to say, but this could be an area where distributors could ease the strain of customers who can’t decide which mop, bucket or cloth will serve them best.
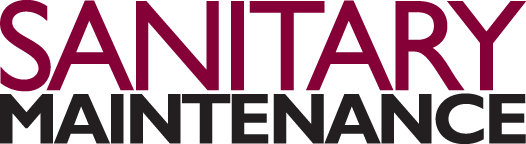
‘Ergonomics’ is Not a Dirty Word
BY Seiche Sanders
POSTED ON: 9/1/2001