Every distributor should get as excited about floor care as Fred Elliott does. Elliott, president and owner of Gamet Supply in Seattle, loves seeing his customers use the right kind of cleaning tool for a particular job. And, of course, he likes selling those tools as well.
For Elliott, a broom is never just a broom. Instead, each one represents a possible solution to cleaning a facility. He sees himself as a problem-solver.
Some brooms are for heavy-duty sweeping and others are for dusting. Some are good on tile, while others are best on wood surfaces. Angled brooms are great for staircases, and double-side brooms provide more versatility.
Sure, there are no complicated switches and settings like an expensive rider scrubber or a chemical proportioning system. But that doesnt mean that distributors should turn up their nose at a product that performs such a valuable function, simple or not.
One of the areas where distributors can provide the most value is teaching customers how to properly maintain their brushes, brooms and mops, according to Gerry Hearnley, owner of The Brush Man Inc., Mahomet, Ill.
I had a customer who was a factory owner in Chicago, and he was giving all his workers pieces of junk for sweeping, he says. I tried to sell him some quality, solid-wood brooms with brass handles, but he wanted whatever was cheapest.
The factory owner told Hearnley that his workers didnt take care of equipment, no matter the quality of the product. But I had him try my brooms for a week and the workers were cleaning like professionals. They were even locking their brooms in their lockers so no one could take them.
Quality brooms and mops can last up to 10 times longer than cheaper models, adds Hearnley, which will save end users a lot of money. If distributors want to be successful, then they have to be able to serve their customers with the best products available.
Just Like New
Distributors provide a great service when they show customers how to make their dollar stretch by purchasing the best mop or broom for the job.
Every broom has different characteristics, says Elliott. Depending on the fibers that are used in the bristles, it will wear differently.
The most common broom is the traditional straw broom, otherwise known as a corn broom or a house broom. This kind of broom is not made of synthetic material, so it is more likely to wear down quickly.
If you continue to sweep in the same motion with a regular corn broom, the bristles will wear out on just one side, says Elliott. Thats why its important to alternate your sweeping pattern. You dont want to leave the sweeping memory on the bristles.
Synthetic brooms have to be carefully maintained as well. Some models have longer bristles that curl up like frizzy hair. End users may want to use a metal wire (which is often already on many brooms) to tighten the bristles and make a stronger, longer-lasting sweep.
Mops require regular maintenance as well. Most people dont launder their mops enough, so the mops end up just spreading old dirt around rather than cleaning the floor, says Tony Richardt, president of KRS, a distributor in Evansville, Ind.
KRS, which also serves as a commercial laundry, makes mop maintenance easy for its customers. It works out a payment plan so that customers can have mops laundered whenever necessary.
Cleaning With Color
As cross-contamination continues to be a major concern for end users, more and more manufacturers are selling brushes, brooms and mops in separate color-coded categories, especially in contamination-sensitive foodservice markets.
We recommend that our customers use a color-coded system, says Richardt. Its usually a color on the mop head, but it can also be around the handle.
In the brushes category, Elliott has been able to help facility managers prevent the spread of bacteria by recommending certain kinds of brushes for certain parts of the building.
Sponges and brushes are very similar in that they can be a breeding ground for bacteria to fester if people dont know how to maintain them. Cellulous scrubby sponges keep getting rinsed and rung out, but that doesnt mean that the bacteria is gone, he says. People need to make sure that all the junk gets removed from brushes and sponges, and use it for one particular area of the facility.
People usually think of color-coded systems as a preventative measure against spreading bacteria from one area of a facility to another (i.e. from a restroom to a kitchen), but Elliott says that they can also help keep workers accountable.
Some workers abuse mops or brooms and others dont use them enough, he says. A manager can tell which area is using the mops improperly just by looking at the color code.
Hearnley believes that color-coded systems are valuable, but only to a point. It really depends on the facility, he says. Most industrial customers, like factories, probably dont need a color-coded system. I think that any chance of cross-contamination in that kind of a setting would be pretty minute.
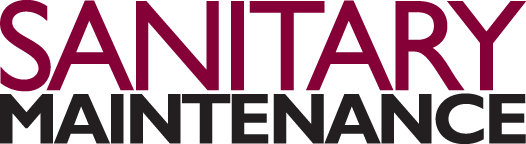
Get a Handle on Maintenance
BY Alex Runner
POSTED ON: 1/1/2003