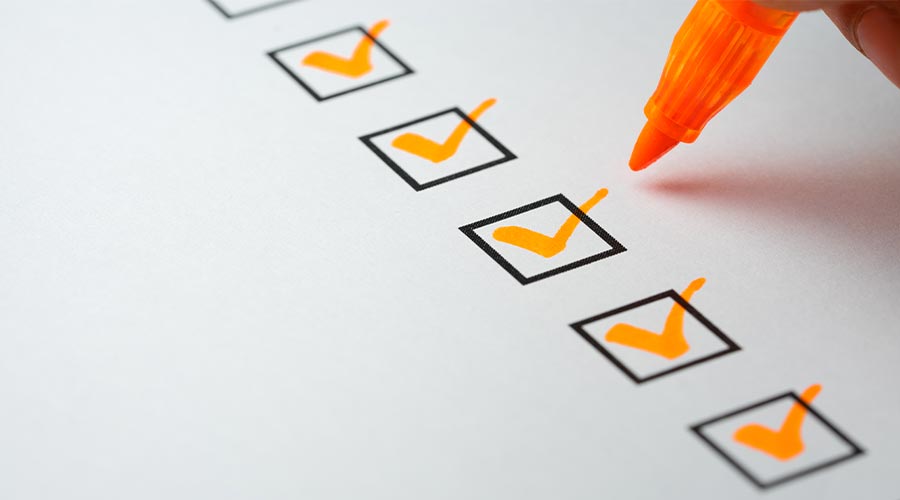
While the ongoing evolution of disinfectants is promising for infection control, Solomon stresses the importance of training end users on proper use. Specifically, following label instructions and Safety Data Sheets (SDS) is essential for the wellbeing of the facility and users of the products themselves.
“The label is the law,” says Solomon. “Frontline teams must know to read the label, understand it, and follow what it says in detail. What is the kill claim? What is the dwell time? What is the proper dilution? What surfaces can each chemical be used on? All these things need to be followed.”
When selling chemicals, distributors should also take the opportunity to educate end users on what disinfectants can be used on which surfaces. According to Solomon, using the wrong chemicals can shorten the lifespan of many materials.
“We have over-disinfected our world in the past several years and we are seeing the unintended consequences of that,” she says.
Effective cleaning also demands consistent chemical dilution. Single- or multiple-product dilution control systems — whether wall-mounted or portable with access to water — prove invaluable in maintaining consistent dilution ratios, for end users who use them correctly. This opens the door for distributors to provide valuable training services.
While working with customers, distributors should also emphasize the reduction of cross-contamination in a proper infection prevention program. For example, using the same cloths or mops across different areas or surfaces can result in the spread of germs. Helping end users implement a color-coded program helps prevent cross-contamination and enhances infection control.
Experts recommend distributors outline product bundles by color when providing these infection prevention solutions. For example, creating a product package that includes red cloths, mops, trigger sprayers, carts, toilet or grout brushes, and buckets could be an easy solution for end users looking to reduce cross-contamination in high-risk restrooms. Create a separate bundle with yellow cloths, mops, buckets and trigger sprayers for allocation of medium-risk areas. Then offer a third bundle of green products, for example, for lower-risk zones.
Of course, color coding won’t eliminate all cross-contamination threats. End users need to be trained on how to use these products in a way that will reduce or eliminate the spread of germs and bacteria. Hicks recommends end users fill buckets with properly diluted disinfectants and then drop all the clean cloths into that bucket. Train frontline staff to take one cloth to wipe a surface, then toss it into a separate container for laundering — every surface gets a new cloth.
“There is a tremendous risk of cross-contamination when a soiled cloth is dipped back into the cleaning solution,” says Hicks.
As important as it is to train end users on proper cleaning and disinfecting procedures, Gerba reminds distributors to also stress the maintenance of cleaning the tools that are being used. In this case, laundering of microfiber is essential in its performance in infection prevention programs.
“Microfiber is good at picking up bacteria, but it then accumulates in the microfiber,” says Gerba. “You have to get rid of that bacteria in the laundering process, or you will start spreading it around.”
Innovate With Technology
Technologies like spraying machines, chemicals that inhibit bacterial growth, or ultraviolet (UV) lights can also aid end users in their fight for infection control, according to Trinks.
Certain chemical agents can eliminate bacteria, mold, fungus, algae and other organisms and protect an abraded surface for up to 90 days. These products, Trinks says, can be applied with a pump sprayer, fogger, or electrostatic sprayer, and will work as well as any quaternary ammonium products out there.
“We prefer to use electrostatic sprayers because we get over 4,000 square feet of treatment per gallon of this product,” he says. “It’s highly effective. After it’s applied, you just need to go back and re-treat high-touch areas like doorknobs or elevator buttons.”
Gerba agrees, adding that spraying machines can save a lot of time for many end users. However, he warns that while they can be effective at applying chemicals that kill bacteria, they do not get to the 99.9 percent removal rate that can be achieved using a disinfectant wipe.
Ultraviolet is another technology that has caught the eye of some end users, especially since the start of the pandemic. According to Solomon, these devices use UV rays to sterilize surfaces, eliminating nearly 99.99 percent of bacteria, fungi, and viruses that can cause disease. They are used in hospitals for the room turnover but see more frequent activity in operating rooms and areas where there is a higher risk of infection.
Although effective, the machines are not widely used for two main reasons. First, the devices can be extremely expensive and require extra manpower to move around. Second, they aren’t “run and done” machines because achieving desired infection control results still requires a preliminary cleaning step.
“Users cannot run a UV device by itself and be done. They still must clean the surface first,” says Gerba. “Otherwise, it has little effect. Once surfaces have been cleaned, a UV light adds another layer of disinfecting.”
End users who are skeptical of technologies like this might challenge distributors to validate their success. One way to do that is with adenosine triphosphate (ATP) meters. Offering tools like this will arm end users with a reliable device that provides a layer of protection by measuring cleaning results. These devices identify whether a tested surfaces harbors unwanted biological material.
“Users can tell whether the cleaning crew properly cleaned and disinfected all surfaces and removed the organic matter,” Gerba says.
He cautions that ATP meters and their potential negative testing results should not be sold as a tool to use as a punitive measure against staff, but rather as a training tool and to incentive staff to perform all cleaning steps as required.
The pandemic heightened awareness of cleaning and hygiene, but it did not transform into a lasting commitment to public health. Jan/san distributors have a pivotal role to play in readying their end user customers for the next health concern by specifying the appropriate products and imparting proper training to ensure cleanliness and safety remain paramount.
Ronnie Wendt is a freelance writer and owner of In Good Company Communications in Waukesha, Wisconsin.
How Distributors Can Assist with Infection Control Programs