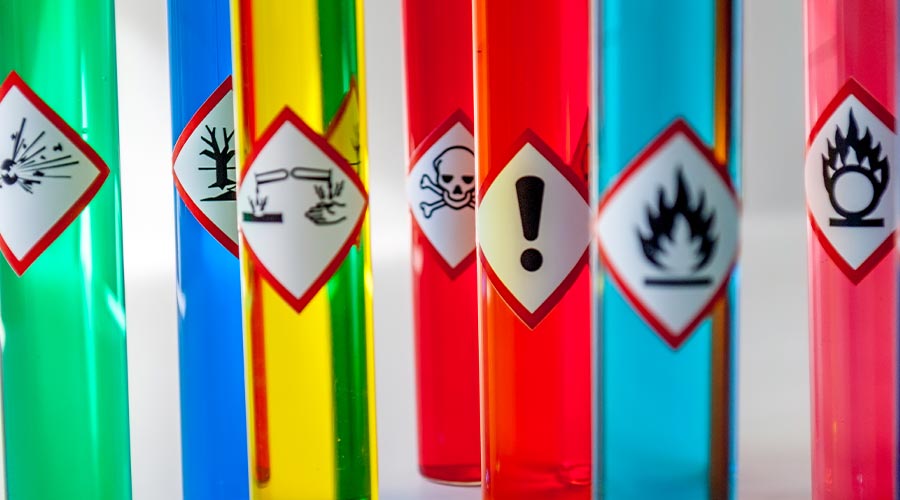
Staying up to date with safety regulations is like trying to hit a moving target. The presence of chemical hazards in facilities is not always apparent, and the requirements implemented to safeguard cleaners from these hazards are constantly evolving.
Difficulty aside, it is vital for facilities to try and strike this elusive target. Compliance with the rules of the Globally Harmonized System of Classification and Labeling of Chemicals (GHS) is not optional; in fact, the Occupational Safety and Health Administration (OSHA) requires it.
Adhering to the rules spelled out in GHS improves safety within facilities by enhancing communication about potential hazards.
“If there's one word that defines the GHS, it's safety,” says Bill Allen, territory manager for Fagan Sanitary Supply, West Elizabeth, Pennsylvania.
Allen emphasizes the important role of distributors in this continuous push for safety.
“A reputable, trusted distributor helps lead customers to greater safety,” he says. “End users should be able to trust their distributor to provide them with the products they need and the training to use those products safely.”
What is GHS?
Before GHS, each country had its own rules for classifying and communicating hazards. This led to confusion and safety risks in workplaces with chemicals.
To solve the problem, the United Nations created GHS, a standardized system for classifying chemicals and providing hazard information on labels and Safety Data Sheets (SDS). The GHS ensures manufacturers use identical hazard pictograms on chemical containers worldwide and specifies the information to put on hazard labels and SDS. This pictorial hazard representation ensures workers, regardless of location, understand the dangers associated with the chemicals they come across or use.
In 2015, the U.S. announced revisions to the GHS — prompting cleaning chemical distributors to comply with new SDS requirements, including pictograms, signal words, and hazard statements.
However, Bill McGarvey, director of training and sustainability, at Imperial Dade, Jersey City, New Jersey, warns that distributors also must check on state requirements, noting, “It’s not uncommon for states to take the OSHA guidelines and go a bit further.”
Regulatory Updates
In 2024, OSHA revised the Hazard Communication Standard (GCS) to better align with the GHS. The final rule went into effect on July 19 but allows a grace period for compliance.
OSHA’s updated HCS introduces several changes:
- Revised Classification Criteria. OSHA updated the criteria for classifying health and physical hazards, resulting in potential classification changes for certain chemicals. Now chemicals previously labeled as mild irritants might receive more stringent labeling based on updated scientific data.
-
Updated Label Requirements for Small Containers. The new rule aims to improve safety by implementing detailed and legible labels on small containers, ensuring clear identification of even minimal amounts of chemicals.
-
Safeguarding Trade Secrets. This revision ensures critical hazard information is put on SDSs while protecting trade secrets. Manufacturers will no longer be able to claim trade secrets to avoid listing ingredients in Section 3 of the SDS.
“Though withholding that information may keep it from their competitors, it also withholds the information from the end users who need it,” McGarvey says. “Now, they have to tell you the hazards associated with those ingredients.”
-
SDS Amendments. The rule change also aims to reorganize and reword some SDS sections to make them easier to understand and ensure they provide comprehensive safety data.
The group most affected by these changes is manufacturers (and importers), who will need to review their chemical classifications and adjust their chemical labels or SDS, McGarvey adds. He stresses that distributors of cleaning chemicals may not be affected by these changes since the changes center on chemicals not used in the cleaning industry.
“The new rules really address specialty chemicals, and the pictograms that reflect those categories of chemicals,” he notes.
Supply Safety Data Sheets
Distributors can keep customers safe and compliant by supplying SDS documentation for every cleaning product they purchase.
“They can also help with labeling requirements and developing a hazard communication program that includes a master chemical inventory list,” says McGarvey. “Distributors can double check that list against the SDS list to make sure their customers have all the documentation in place and available to their employees.”
Fagan Supply, for example, provides a product dashboard that contains an SDS for every product a customer uses.
“They can keep the SDS in a file on their computer, and can draw from those documents as needed,” says Allen. “We also host training sessions to help the staff go through the product datasheet to ensure they understand the dilution rates, pH level and other things about the product.”
This training also covers product certifications and their various meanings. If a product is NSF (National Sanitation Foundation) certified, for instance, workers know it is safe to use in a foodservice area.
Fagan Supply also teaches workers how to understand the SDS, especially hazard identification, First Aid, and labeling.
The Purpose of Pictograms
In addition to having SDS on-hand for end users, GHS pictograms can be equally important. For their own safety, workers must be able to identify them when using cleaning chemicals.
“The entire purpose of a pictogram is to give a snapshot of the concerns with the product,” says Allen. “Not knowing these things can lead to chemical misuse and improper mixing of chemicals.”
McGarvey adds that pictograms cross language barriers because pictures are more easily understood than words.
GHS uses nine pictograms, each with a different meaning. For example, a skull and crossbones inside the red diamond shape warns that the chemical is toxic, and exposure can even lead to death. A pictogram with a chest and star in the center shows the chemical is hazardous to human health, while a flame highlights that the product is flammable.
Though all pictograms are important, Allen says the one that he advises watching for is the exclamation point in the red diamond. This indicates the chemical can irritate the skin, eyes, and respiratory track and possibly harm the environment.
“If you see the exclamation point, do not assume it’s just soap in your eye,” he says. “It could be that, but it could also be something more. The starburst in the chest area usually points to severe health hazards, so that’s critical. In any case, customers need to look at those pictograms and do some research to learn more about how to protect themselves.”
Distributors play a vital role in this understanding, Allen adds. “We need to provide thorough information to the end user so that they can be as safe as possible when using these products.”
Personal protective equipment (PPE) should also be used whether the chemical is toxic or not. Workers should always wear gloves, eye protection, masks and so on.
“They are cleaning soiled loads, and they do not know what that soil load is,” says Allen. “PPE will provide protection.”
Look at Proper Labeling
Manufacturers put pictograms on their containers, but they should also be affixed to the cleaning staff's bottles. Unlabeled spray bottles can lead to improperly mixed chemicals, product misuse, and loss of efficacy.
McGarvey emphasizes that every reusable spray bottle must be properly labeled in accordance with GHS regulations when chemicals are mixed using dilution control systems.
Most chemical manufacturers provide ready-to-use, EPA-registered product labels to distributors, who should in turn give those labels to customers.
“Those labels must be applied to spray bottles to show ingredients and any hazards they can cause,” Allen says. “A product might tell you to avoid contact with eyes, skin and clothing. Another might tell you to wash your hands thoroughly with soap and water after use and before eating.”
The labels should also be affixed to mop buckets and any carrier of chemicals to provide hazard information at a moment’s notice.
The key is to use manufacturer-supplied labels, adds McGarvey.
“When people make their own labels, that’s when they run into trouble,” he says. “I always say, ‘There is no way to fit all this information on a piece of masking tape.’ You need to have the official label.”
In addition to supplying official labels, distributors can help end users customize safety procedures even further. For example, pairing colors of chemicals with labels and cleaning tools.
Color coding in the cleaning industry most often applies to the color of a mop, microfiber cloth or mop bucket, where each color signifies where it is to be used. To give an example, red is commonly used in toilets, and dirty utility rooms; blue is for general cleaning or glass; green is for kitchens and food service applications; and yellow is used in infectious isolation areas. McGarvey suggests that color coding could be employed in labeling as well.
“You can make sure that the label matches the color of the product, further simplifying safety for frontline workers,” he says. “So, if you have a blue label and a green cleaner in the bottle, you know something is wrong. Anything you can do to make things easier for people to understand what the product is and how to use it safely helps.”
Allen also cautions against topping off chemicals in spray bottles because chemicals can lose their efficacy over time.
“We suggest dumping out diluted disinfectants at the end of the week, spraying out what’s in the trigger sprayer, and then rinsing the bottle before refiling,” he says. “Most manufacturers will tell you how long the mixed product maintains its efficacy, and then we work with them to refresh their trigger sprayer bottles within that timeframe.”
Conduct Refresher Training
According to McGarvey, distributors can provide annual refresher training on GHS, its components, and on hazard compliance programs.
Imperial Dade, for example, offers annual refresher training for customers where they go over SDS sections and what they mean, explain the various pictograms, and provide support for their hazard communication programs.
“We want to give customers some familiarity with the information because the time to look at the SDS is not when a worker has chemical in his eyes,” he says. “SDS documents do not expire within a year, so unless there is a change in formulation or something like that, the information doesn’t change. But workers should review those sheets annually, to stay fresh on the information they contain.”
The length of this training can vary, depending on what the customer wants. Allen says customers usually pick how long the training is. A typical session on PPE, SDS, labels, cleaning, job duties, and equipment is around four hours, for reference.
Distributors should instruct end users to also keep records as to which workers completed the training.
“We typically include a sign-up sheet for who was there and provide a certificate of training,” adds Allen.
McGarvey says he shares a PowerPoint presentation with all participants and quizzes participants on the material when asked.
He also supports the company in making sure its Hazard Communication Program meets all OSHA requirements. While boilerplate programs can be found online, modifications are necessary to adapt them to specific chemicals and unique state mandates.
“The master chemical list serves as a table of contents for their SDS binder,” McGarvey says. “If they use a product in their facility, they need an SDS in that binder for that chemical. We also help them with the secondary labeling issue, making sure all chemicals and secondary bottles are properly labeled. And we review the chemistry of cleaning and the specifics of their product lineup.”
This training is necessary for customers, but it also offers distributors a chance to assess the products being used. It’s an opportunity for distributors to consider if they can either reduce product usage or suggest more effective alternatives.
“We also can be on the lookout for what’s wrong within the operation,” says McGarvey. “Are people working safely? Are they using chemicals correctly? Ideally, we want to be an unpaid employee to our customers that provides great value.”
Ronnie Wendt is a freelance writer and owner of In Good Company Communications in Waukesha, Wisconsin.