People take waste receptacles for granted. They walk into a shopping mall, finish their cup of java and without thinking much about it crumple and toss it into the nearest container. Or at the ballpark, they head for the concession stand, gobble up a bratwurst, wash it down with a soft drink and automatically toss the wrapper and cup into, you guessed it, the nearest garbage can. Individuals working in industrial or health-care settings use them continuously, too, during the course of their daily routine.
As ubiquitous as it is, the waste receptacle has to be tough. Over its lifetime, in its various locations, its subject to numerous bumps and bruises, scuffs and scratches, and dents and dimples. It gets moved around. Its always filled with refuse that has to be dumped. And many times it is placed in an outdoor setting, where the elements can be unforgiving.
Manufacturers of this highly utilitarian product category research new materials that can enhance durability without sacrificing aesthetics. Theyve come up with plastic that looks like wood, synthetic paneling that looks like metal, specialized metal that wont rust and protective sprays and coatings.
Just what makes a waste receptacle durable? What materials are best for a particular environment? How can jan/san distributors help their customers maximize that products longevity?
Charles Hadaway, national sales manager for Witt Industries in Cincinnati, has some answers for these and other pertinent receptacle questions.
Bag Up Product Knowledge
Jan/san distributors should guide waste receptacle end users to the appropriate product, he says. Their knowledge of product lines should help them provide information that will help their customers make the best selection that will give them a life-cycle cost advantage. So many people complain that a product is too expensive. But if they purchase the right product and it lasts, they should consider what it costs over its lifetime not what it costs today.
Built to Last
Over the past decade, Hadaway has seen durability of waste receptacles improve. Our company and other manufacturers are essentially making the same products we were some 10 years ago but weve come up with new and stronger materials.
According to Hadaway, manufacturers of plastic receptacles make their products flame retardant, but he believes metal containers are more so. More manufacturers are trying to make their products meet flammability ratings in the United States either Underwriters Laboratories (UL)-rated or California Smoke-Tested.
It stands to reason, says Hadaway, that a metal container will stand up to more abuse than other types, both indoors and outdoors. If you galvanize a metal container, that will increase the life of the product significantly. But youre not going to need galvanized metal for an indoor receptacle.
Theres probably more research being done today on specialty products for niche markets, like the medical market. You see a lot of antimicrobial agents in products today.
Hadaway points out why containers made of stainless steel are on the market today. Some people want a stainless steel look for their receptacles. Others, such as cruise lines, want containers that wont rust. Some types of stainless steel [waste receptacles] are rust-proof, while others arent.
Hadaway says that specialized coatings help improve waste receptacle durability. There are coatings that will protect paint and make it last longer. And coatings that will treat metal to be antimicrobrial or antibacterial. Coatings can prevent rust. Our company is doing some research and experimental work to see if a Teflon coating can be effective on the inside or outside of a can. Or on a swing top, for example, to prevent trash or bacteria from sticking to it.
Tough Science
Mike Boland, owner of Alliance in Manufacturing, St. Louis, has also seen durability steadily improve over the last decade. Theres been improvement in both structural design and appearance, he says.
Engineered plastics have given us resins that are resistant to ultra-violet (UV) light, that are fireproof, and that are resistant to extreme cold and heat. So theres been an overall improvement in function. Cosmetically, we have materials that have the look of wood through stains and other topical treatments, yet they have the maintenance resilience of plastic. And we have materials for plastic containers that have the appearance of stone granite, marble, and aggregates.
Boland believes there have been a lot of advances in manufacturing because of computer technology. Computer assisted design (CAD) units now allow us to improve the durability of handles, rims and bottoms of containers areas that typically receive heavy abuse.
According to him, plastics stand up best to constant abuse. Nothing else can compare to plastic, he says. But I do believe that all container materials have their pros and cons. Plastics, for example, raise concerns in fire situations, but we do have plastic receptacles that are fireproof because of lid and door designs. We have other fire-resistant products, too, where the resin itself is fireproof and UL-approved. These are placed in critical areas such as health care institutions. And in an outdoor environment, plastic receptacles tend to deteriorate over time.
Steel has an Achilles heel too, because of dents and rust. And with stone aggregate products, you have to contend with high shipping costs, cleanability, breakage and high production costs. With wood products, there are high shipping and production costs, plus the eventual breakdown of the product because of weather conditions. And with fiberglass, the high shipping and production costs are somewhat balanced.
The Power of Plastic
Brian Parks, national sales manager for Toter Inc., Statesville, N.C.; credits improvements in the durability of his companys plastic receptacles to the manufacturing processes used. Our process of choice is called rotational molding, which more than injection molding or blow molding allows us to produce stronger materials. One of the drawbacks of plastic is that it would crack under [extreme] environmental conditions of heat and cold, he explains.
According to Parks, rotational molding increases the plastics environmental stress crack resistance. Its done by putting plastic in powdered or granular form into a mold, which starts to heat up as it rotates in an oven. The plastic melts and adheres to the surface of the mold.
Now Toter has patented a process called Advanced Rotational Molding, where we add UV inhibitors and UV stabilizers that enable the plastic to stand up better to the stress of heat and cold. And it wont fade in the sunlight.
As far as specialized coating goes, Parks says that his company uses low density polyethylene. With it, you get the strength and durability of heavy plastics or metal, but [also] the resilience of plastic. Thats also inherent in our rotational molding process, he says.
Parks says his company issues a non-prorated warranty of two years on its containers. But weve got containers that have been in service upwards of 20 years. The length of service will depend a lot on the abuse taken by the product while its in service. Id say the average life of a container is about 10 years.
According to Parks, distributors can best help their customers by talking and listening to them to determine and recommend the appropriate product and its appropriate application. And be sure to be budget- and value-conscious, he advises.
Layton Dotson, vice president, sales and marketing for United Receptacle in Pottsville, Pa., says his company has used a Uni-Koat powder coating to make its commercial waste receptacles more durable. Its a paint process that involves spraying a powder that actually melts into the steel. It gives them a much more resistant finish and does a lot to protect the metal against corrosion, scratches and stains. It makes for a better-looking and lower-maintenance product, he says.
Thats one of our primary ways of enhancing durability. In addition to the coating, we add a UV protectant and stabilizer because the sun can fade the finish of an outdoor receptacle.
Dotson says many of his companys outdoor products are manufactured out of galvanized steel that wont rust or corrode. Galvanized steel stands up best to the constant outdoor abuse that waste receptacles face. We make a very durable product. Many of our receptacles are situated all around the Jacob Javits Convention Center in New York, where theyve been for probably 20 years and still look good. All they do to maintain them is pressure wash them in the spring, he says.
Options Equal Profits
Although United Receptacle primarily manufactures steel waste receptacles, it has been expanding to include receptacles made of fiberglass and pre-formed concrete. That speaks to durability, he says. In addition to just using molded concrete, we inject a 5 percent air content into the concrete when its molded. That allows the concrete to expand and contract in different temperatures, and that stops the crumbling you see in ordinary concrete, he adds.
Most recently weve changed many of our products over to galvanized steel. Weve incorporated galvanized and stainless steel into virtually all of our outdoor products.
Distributors can best help end users get the most out of their waste receptacles by helping them find product lines that provide continued value and durability over the long haul, says Dotson.
Jordan Fox is a freelance writer based in Milwaukee.
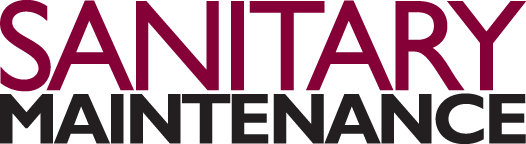
Talkin’ Trash With Industry Leaders
BY Jordan Fox
POSTED ON: 9/1/2003